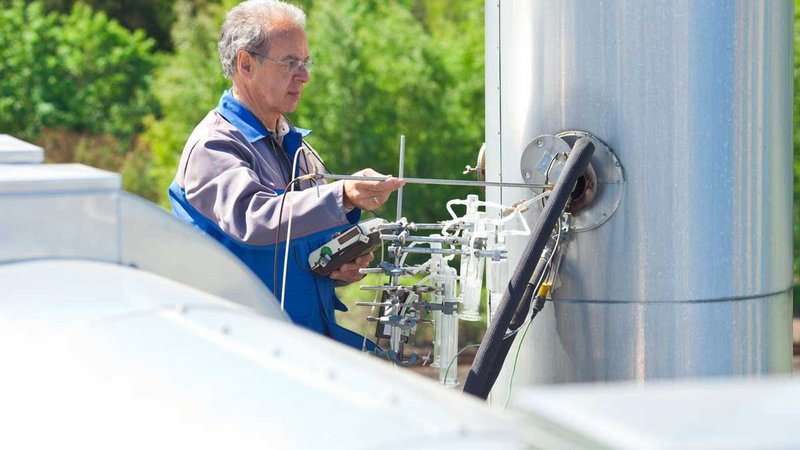
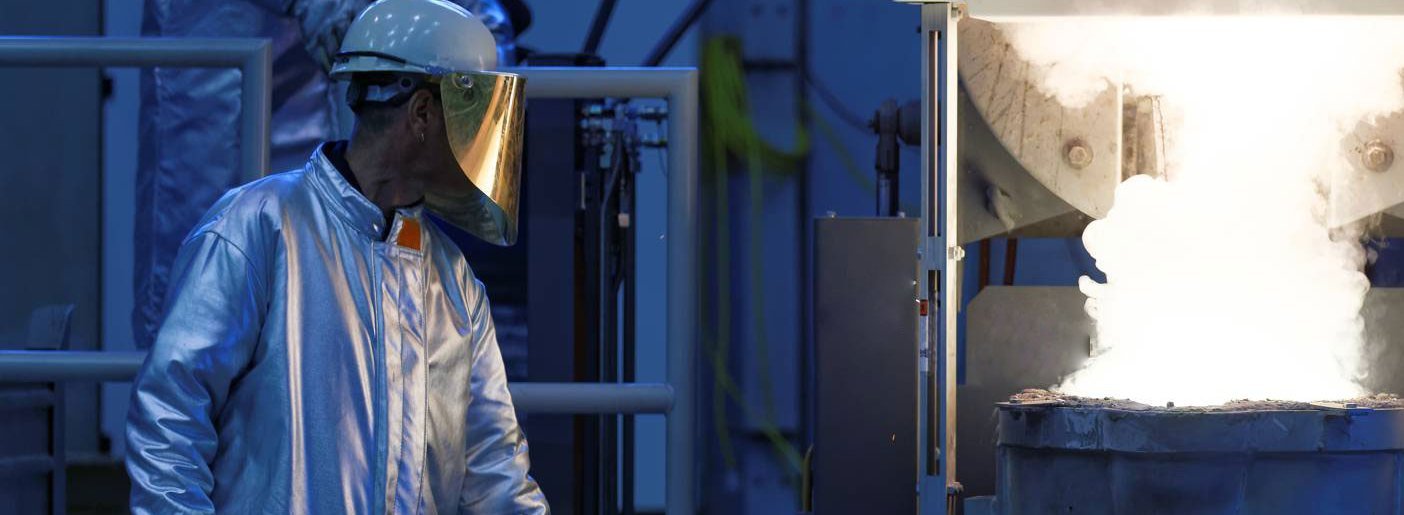
Metal casting processes: an overview
What is metal casting?
The concept of metal casting is a simple one, and one that has been around for a very long time. The earliest known example – that of a Mesopotamian copper frog – dates back over 5000 years. Simply put, it involves heating a metal or alloy until it has melted. The molten material is poured into a mould, where it solidifies. Once solid, the metal part is removed from the mould.
Casting allows the cost-effective mass production of complex parts that would be difficult or uneconomical to make in any other way. It is thus is foundational to the industrial processes that underpin modern ways of life. From generating the electricity needed to keep the lights on, to the utensils and appliances used for cooking, and pretty much all forms of transportation (to name only a few examples) castings play an essential role.
What metals are cast?
More than 100 million tonnes of castings are produced every year with China predominating production. Ferrous castings (iron in various forms, and steel) dominate the casting market. Aluminium-based castings make up much of the remainder, with volumes expected to continue to rise. Copper is the only other metal to account for more than 1 million tonnes of castings annually, while zinc and magnesium also form small but important market segments.1
Types of casting processes
Although conceptually simple, in practice casting is a complex science. Best results depend on a range of factors, which help determine the type of casting process used for any particular application. Casting processes are generally categorised by the type of mould used, which can be either expendable or permanent.
Expendable mould processes use a mould that is broken-up to release the metal part after solidification. Expendable mould processes generally allow the casting of more complex shapes, but production rates are limited by the need to re-make the moulds after each casting. In contrast, permanent mould processes use a re-usable mould, also known as a die. Permanent mould processes lend themselves to high-speed, high-capacity automated production lines; however, the geometrical complexity of casting is limited by the need to open the mould to release the piece.
Follow the links below for a detailed description of each casting process, what it’s used for, and the pros and cons.
References
1 Based on the 2021 Census of World Casting Production published by Modern Casting (December 2021).