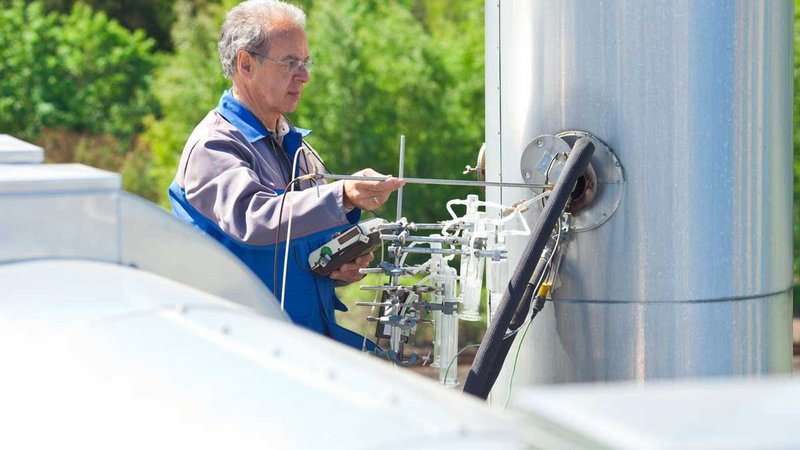
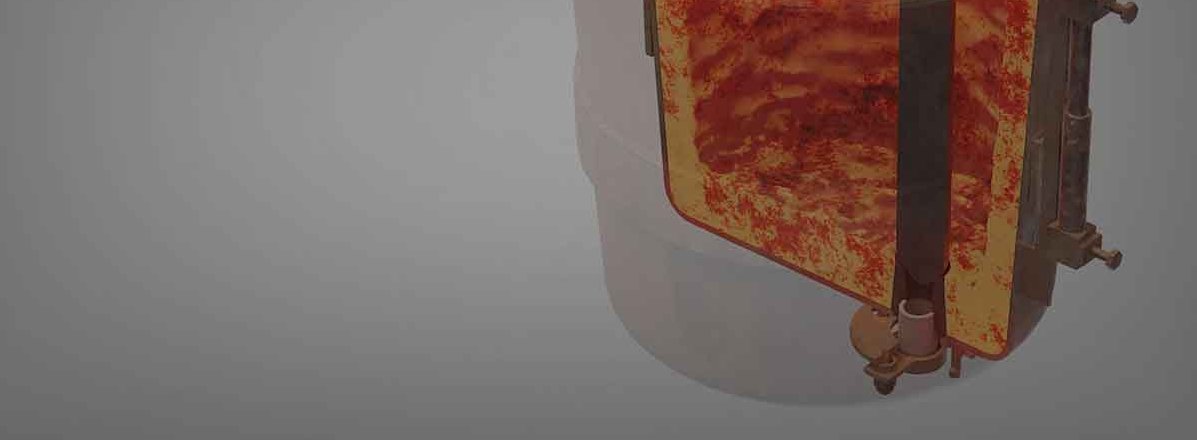
VAPEX FosFlow nozzles
A solution to rapid changes of nozzle size in bottom pour applications
- Quick change of the pouring nozzle
- Faster ladle set up
- Suitable for multiple use
- Less refractory work
Bottom pour ladles: a challenging pour
Bottom pour ladles have a number of advantages over other ladle types, such as lip pour and t-pot ladles. These include shorter casting time and lower maintenance requirements, as well as the ability to gas purge and minimise ingress of slag into the melt stream (these latter two being important for clean casting). However, bottom pour ladles are also prone to turbulence in the pour, which makes the selection of appropriate stoppers and nozzles essential.
The VAPEX FosFlow nozzle system is the latest advance to the Foseco flow control range, and allows foundries to more easily change nozzle diameter – even when the ladle is full. This makes it possible to ensure that optimum flow control is in place for each casting.
Downloads
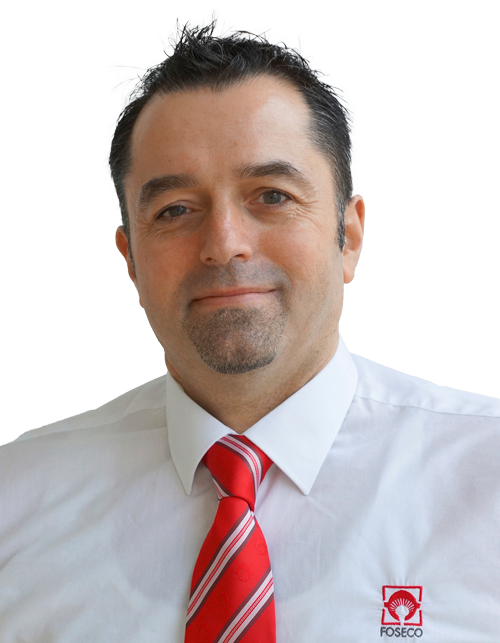
Benefits are mostly found in steel foundry applications:
- The pouring nozzle can be changed quickly
- Multiple use of the stopper & nozzle system resulting in labour cost reduction
- No cooldown of the ladle resulting in energy savings and increased ladle lining performance
Contact
Rudi Bittniok
International Marketing Manager Foundry Flow Control