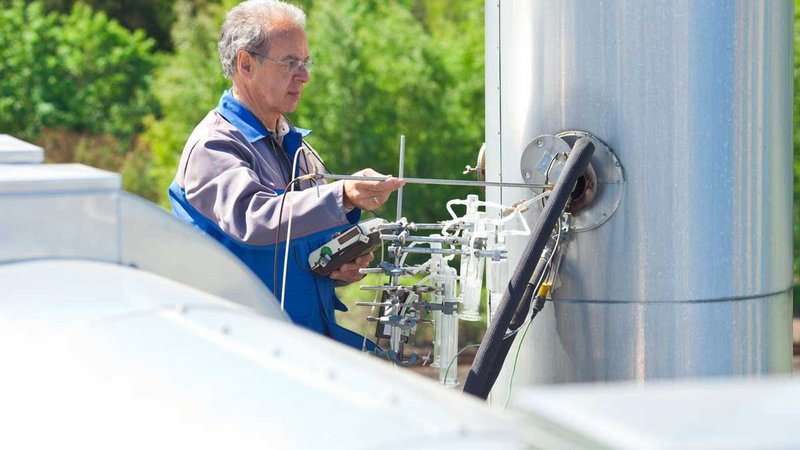
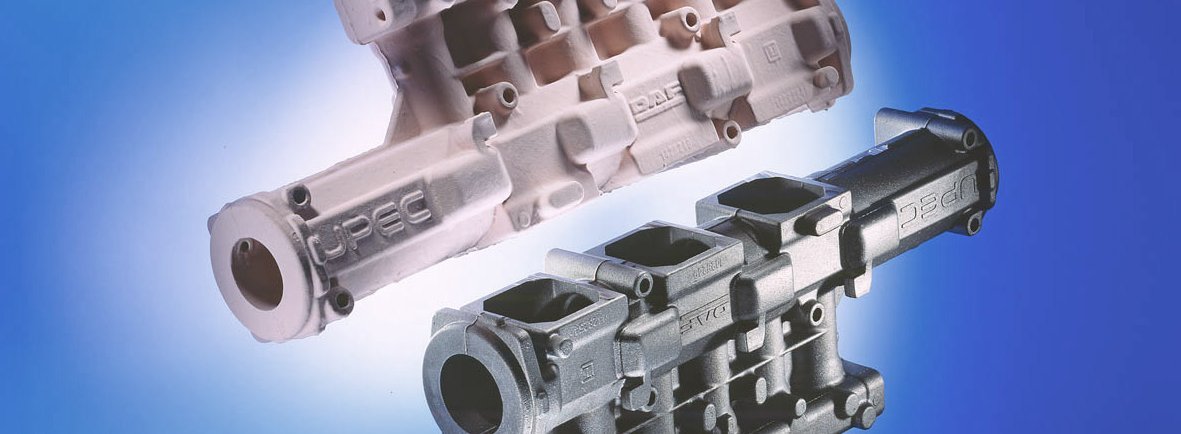
Lost-foam casting
What is lost-foam casting?
Lost-foam – or evaporative – casting was developed in the early 1950s by Canadian sculptor, Armand Vaillancourt. It entered production casting in the early 1980s, when it began to be adopted by automotive foundries to produce parts for the automobile industry, notably GM, which in 1986 announced it would manufacture the aluminium engine blocks, cylinder heads, iron crankshafts and differential cases for its new Saturn car line exclusively by lost-foam casting. Today, PSA continues to manufacture engine components for its brands (Peugeot, Citroën, Opel and Vauxhall) using the lost-foam process.
The process shares characteristics with both investment (lost-wax casting) and sand casting methods. Where investment casting uses wax to create the pattern, lost-foam casting uses an expanded polystyrene (EPS) foam. Unlike investment casting, however, the pattern is not removed before pouring, as the heat of the molten metal is sufficient to vaporise the EPS as the mould it filled.
Similarly to sand-casting methods, lost-foam casting uses sand to create the mould around the pattern. However, unlike in other sand-casting processes, no sand binders are required in lost-foam casting. Instead, the pattern is placed into a steel box (or flask); loose sand is then poured into the flask and compacted around the pattern to form the mould.1
The lost-foam casting process
Lost-foam patternmaking
The lost-foam casting process begins with the creation of the EPS patterns (or pre-forms). Pre-expanded polystyrene is moulded in an aluminium die and heated; this causes the polystyrene beads to expand further and fuse. The die is then cooled to allow the pattern to be ejected, after which the pattern is aged until stable for casting (the pattern will slightly contract as it cools fully). This may take several days at ambient temperature, but can be shortened to hours if patterns are cured in a heated environment.
As the casting will reproduce every detail of the pattern, patternmaking is the critical step for ensuring the accuracy and finish of the cast piece. It must be dimensionally accurate, taking into account the abovementioned shrinkage. The patterns – which are relatively delicate compared to other casting patterns and moulds – must also be carefully handled so as to avoid distortions or damage.
The density of the EPS is similarly important. The lower the density, the easier it is to ensure complete filling of the mould, but the poorer the surface finish and the greater the risk the pattern will distort during handling and sand compaction. A high density will, however, increase resistance to the flow of molten metal, making it difficult to ensure complete filling of the mould, and particularly of thin sections. EPS density must balance these factors, being the minimum possible to achieve the specified surface density and pattern strength.
A final consideration is the foam itself. High carbon irons, such as ductile irons, are prone to lustrous carbon defects when cast using EPS patterns. This considerably limited the applicability of lost-foam casting in the early years of the technology. However, the development of EPS-PMMA copolymers for lost-foam patternmaking has changed this. These copolymers vaporise completely under heat, eliminating the residues that caused the lustrous carbon defects when using EPS.
Assembling the patterns
After aging, the patterns are assembled for casting. If the pattern comprises multiple pieces, these are now glued together. The use of such multiple-part patterns allows the production of highly-complex geometries; however, care must be taken to avoid excess glue extruding from the join, as this will be reproduced as a surface defect in the casting.
Multiple smaller patterns are usually assembled into a cluster around a central foam piece, called a tree, to allow for concurrent casting of multiple pieces. Larger pieces are cast singly. The patterns are then covered in a ceramic refractory coating – usually by dipping into a ceramic slurry bath.
Coatings and sand investment
Coatings, such as SEMCO perm and STYROMOL water-based coatings from Foseco, play an important role in many casting processes, acting as a protective barrier between the mould and the molten metal. The coatings used for lost-foam castings have some additional roles, however. They must be relatively strong, when dried, so as to stiffen the pattern and reduce the risk that it will distort during sand compaction. They must also be permeable to allow the escape of liquid and gaseous ESP residues during mould filling.
How permeable depends on the application:
- In high-temperature applications, such as iron casting, coating permeability is tailored to the specific demands of the customer and casting application, and controls the filling speed of the of the mould; it therefore represents a critical factor within the overall process. In addition, as large volumes of gas are produced quickly as the pattern vaporises, permeability will be higher when compared to lower-temperature processes, to avoid metal blowback up the sprue.
- In lower-temperature processes, such as aluminium casting, the patterns degrade to form residues of lower molecular weight polymers and monomers. In addition allowing the escape of gases from the melt, the coating must therefore also be capable of absorbing these residues quickly enough to avoid slowing the filling process (and causing misruns), but with sufficient control to prevent turbulence in the pour.2
After coating, the patterns are ready to be mounted to a pouring funnel (sprue) and placed into the flask. Dry, loose sand is then poured around the pattern.
As the sand is added, the box is vibrated to compact the sand and ensure it flows into any cavities in the pattern. The level of vibration should be sufficient to ensure the patterns are fully encased, but avoid damage to or distortion of the patterns. It should also be remembered that sand cannot be induced to flow against gravity! The patterns must therefore be placed so that any cavities are filled either horizontally or downwards.
The sand itself should be free flowing to facilitate pouring into the flask and full encasement of the pattern. It must also be permeable to allow the release of any gases and liquids residues produced during the pour (see above). Relatively coarse, spherical-grained sands are therefore preferred.
Filling and shake-out
At this point, the moulds are ready to be filled with the molten metal. The method of filling will vary with the application. In low-temperature castings (such as aluminium), selecting a coating with optimum permeability (see above) allows sufficient control of the fill to allow direct pour. In iron casting applications, however, the higher density and heat of the melt means pours are usually bottom-gated in order to achieve adequate control of the filling process. A vacuum may also be employed to maintain accurate casting dimensions and help remove the gases during pouring.
After the metal has solidified, the flask is dumped onto a shakeout conveyor, and proceeds through the shakeout area to remove loose sand and coating. Because no binder is used in the process, the sand is easy to reclaim and recycle. Individual castings are removed from the tree (when used) and the ingates removed. The castings are then ready for final machining, although due to the high-quality of casting provided by the lost-foam process, this step may be eliminated (or, at the very least, reduced to a minimum).
What is lost-foam casting used for?
Most metals can be cast using the lost-foam method; the most successful applications are therefore those that can take advantage of the specific benefits of the lost-foam process. The predominant use of lost-foam casting remains the manufacture of automotive parts – the application for which it was originally developed – where it has proved successful for the casting of complex pieces in a range of metals.
- High dimensional accuracy
- High surface finish, and no joining lines or flash associated with mould and core assembly
- Reduced grinding and machining
- Ability to make highly-complex castings
- Does not require additives, binders or cores
- A wide range of casting sizes can be produced (from 0.5kg to tens of kilograms)
- Castings are generally lower strength
- Low-strength patterns are vulnerable to damage and distortion
Note
1 In contrast, full-mould casting uses a bonded sand with a polystyrene pattern.
2 Extreme turbulence may result in mould collapse, but even minor turbulence impacts the quality of the case, resulting in defects such as blowholes, oxides and inclusions.
Further reading
Brown, J.R. (ed.), Foseco Ferrous Foundryman’s Handbook (Butterworth Heinemann; 2000), Chapter 12: Sands and green sand, pp. 146-166.
Brown, J.R. (ed.), Foseco Non-Ferrous Foundryman’s Handbook (Butterworth Heinemann; 2000), Chapter 12: Sands and sand bonding systems, pp. 149-166