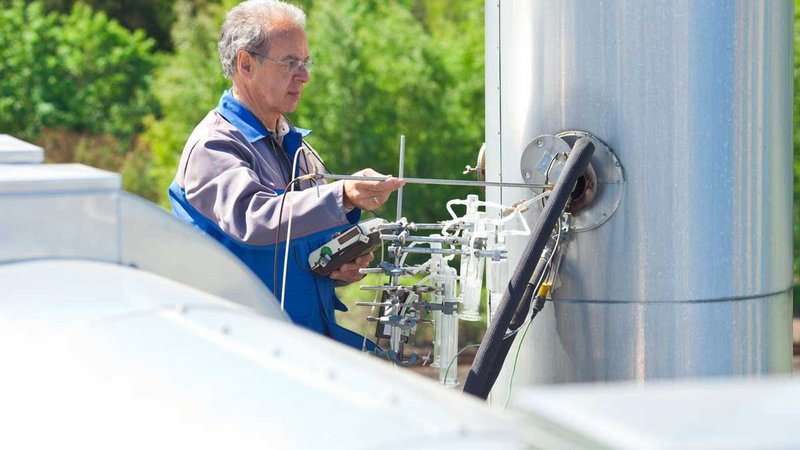
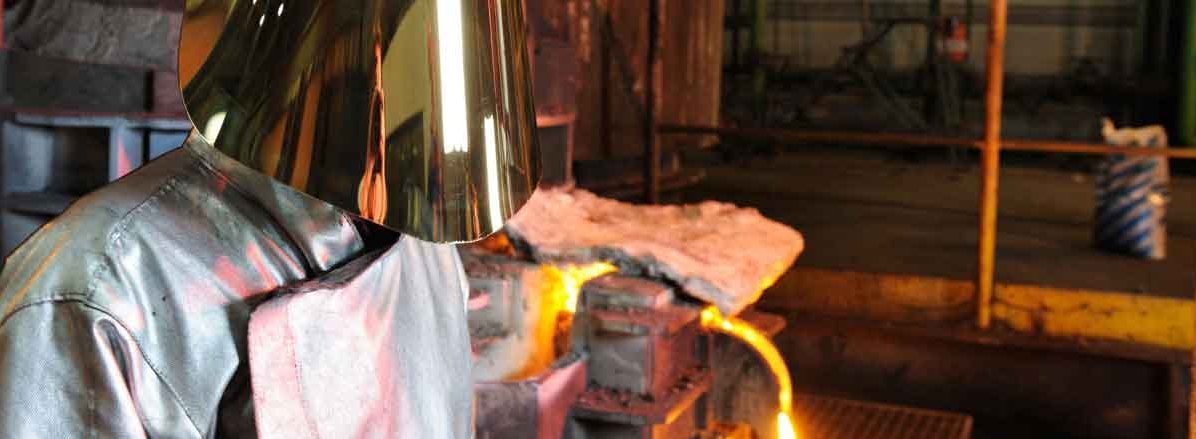
Furnace linings for foundries
- Excellent refractories
- Consistent performance
- Clean furnace systems
- Quick installation
- Slag resistance
- Linings for steel coreless induction furnace
- Linings for iron coreless induction furnace
- Iron and steel melting ancillary refractories
- Linings for aluminium coreless induction furnace
- Linings for cupola furnaces
- Linings for holding and pouring furnaces
- Linings for dosing and low-pressure aluminium furnaces
- Linings for tower and reverberatory melting furnaces in aluminium foundries
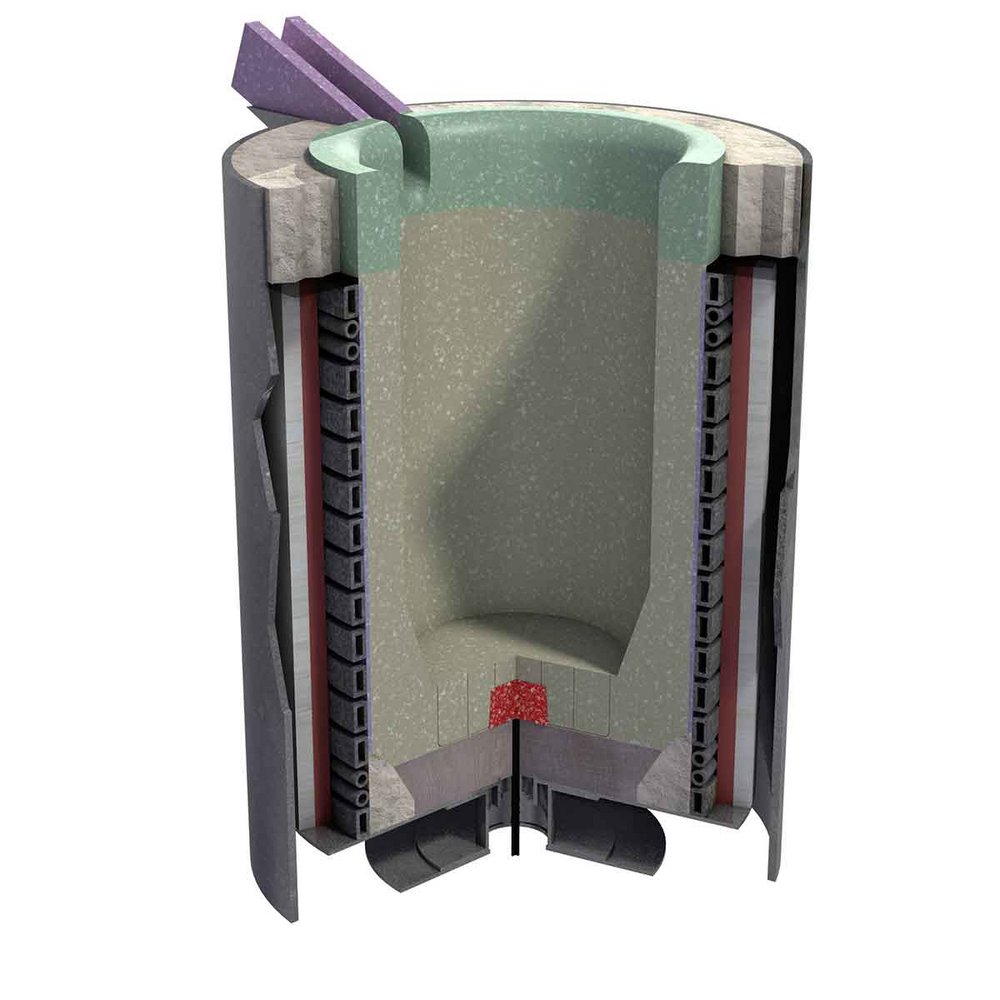
Coreless induction furnace linings for steel foundries
Most steel foundries melt scrap in coreless induction furnaces. In larger steel foundries, electric arc furnaces may also be used.
Primary lining
KELLUNDITE high purity alumina spinel forming, dry-vibration refractory materials are designed for lining coreless induction furnaces melting steel alloys.
Capping material
KELLUNDITE 97CAP is a high alumina spinel forming dry topping material that ensures a seamless transition of the refractory without joint.
BLU-RAM are ready-to-use high alumina chemically bonded plastic materials.
Spout material
- BLU-RAM phosphate bonded plastic
- CRITERION low cement castable
Casting clean: today’s solutions and opportunities
Learn more about improving casting quality in steel casting applications in our white paper Casting clean: today’s solutions and opportunities. This paper cuts through the noise and brings clarity to the clean steel debate: an overview of common casting defects is followed by a detailed review of the technologies currently on offer to reduce casting defects and improve cast quality at each stage of the steel casting process.
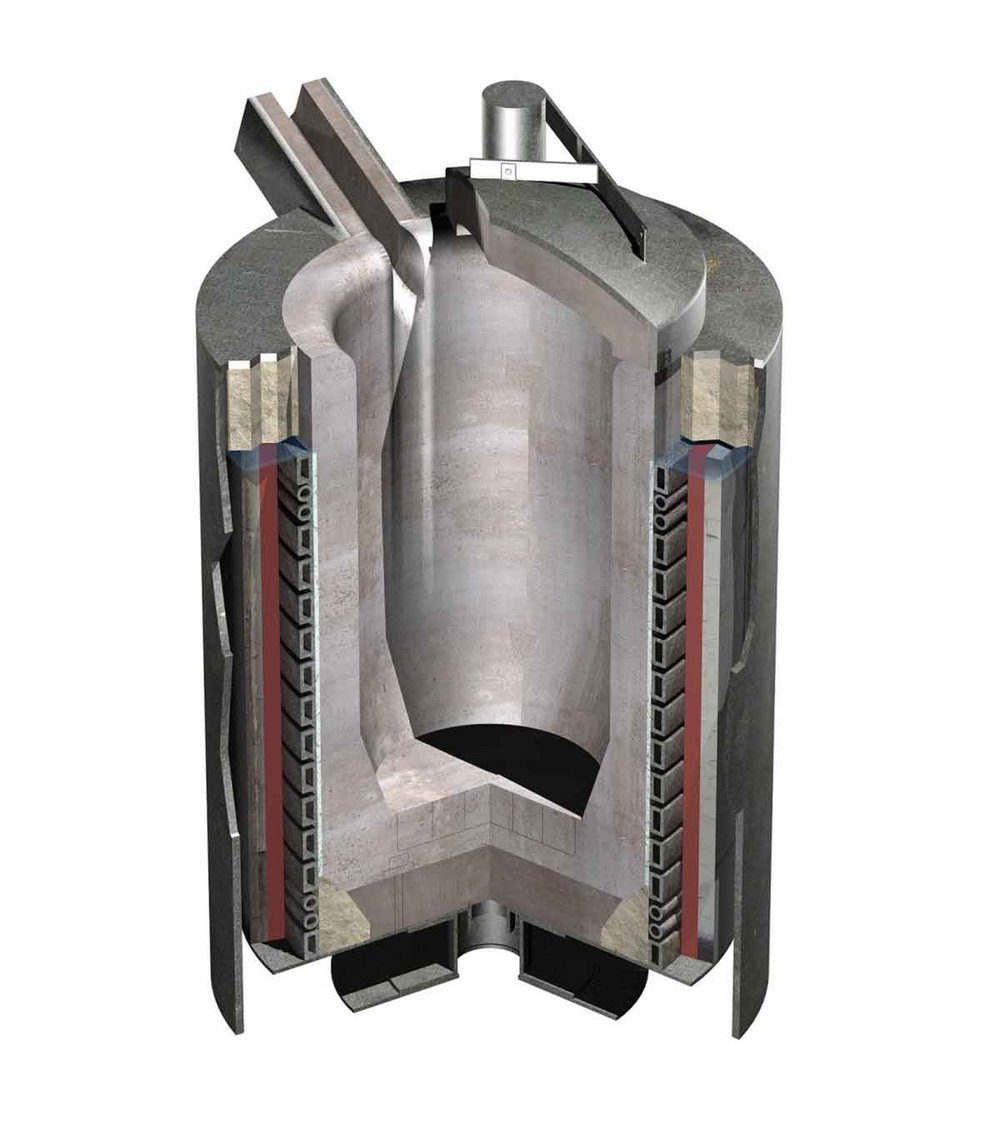
Coreless induction furnace linings for iron foundries
In most iron foundries, the primary melting process is by cupola or coreless induction furnace.
Primary lining
SG iron melting
SILCOR linings are high purity, graded quartzite (silica) based dry-vibration refractories enriched with fused silica. Used for lining high powered, medium frequency induction furnaces melting low silicon SG based iron, SILCOR improves:
- lining life
- productivity
- metal cleanliness
- lining security
SILCOR is exclusively supplied by Foseco and can be used as a complete lining.
Iron melting
KELLUNDITE refractories are an alumina based, mullite forming, dry-lining alternative to quartzbased silica linings for grey and ductile iron. With the health and safety issues associated with the installation and removal of silica-based refractories, KELLUNDITE materials provide a cost-effective, alternative lining solution.
Capping & spout materials
BLU-RAM and DURACRETE ready-to-use, chemically bonded plastic materials vary in alumina content from 45-85%.
Benefits include:
- ease of installation
- very low moisture content
- excellent adhesion to existing linings
- high resistance to infiltration
Iron and steel melting ancillary
Coil protection
SUREBOND COILCOTE alumina based, cement bonded grout for coating the induction coil.
Slip plane:
- COIL PROTECT woven glass phlogopite mica
Patching and repair:
- X-9 Plaster fine-grained phosphate bonded patching material
- DURACRETE phosphate bonded soft plastic material
Lid Material
- CERCAST mid alumina, conventional castable
- TRIAD no cement castable
Coreless Induction Furnace for aluminium foundries
Coreless induction furnace linings for aluminium melting are required to exhibit excellent nonwetting properties and operate successfully over a range of melting and casting temperatures for aluminium alloys.
KELLUNDITE high alumina dry-vibration refractories are used for induction furnaces melting aluminium. They include the addition of a special aluminium resistant agent to provide a clean furnace lining with minimum dross build-up and sticking, enabling easy and non-aggressive cleaning.
KELLUNDITE dry topping prevents crack propagation and ensures a seamless transition from the furnace body to capping area.
Spout material
- BLU-RAM phosphate bonded plastic
- ALUGARD precast refractory
Lid Materials
- CERCAST 1500AL castable with good volume stability and non wetting additives
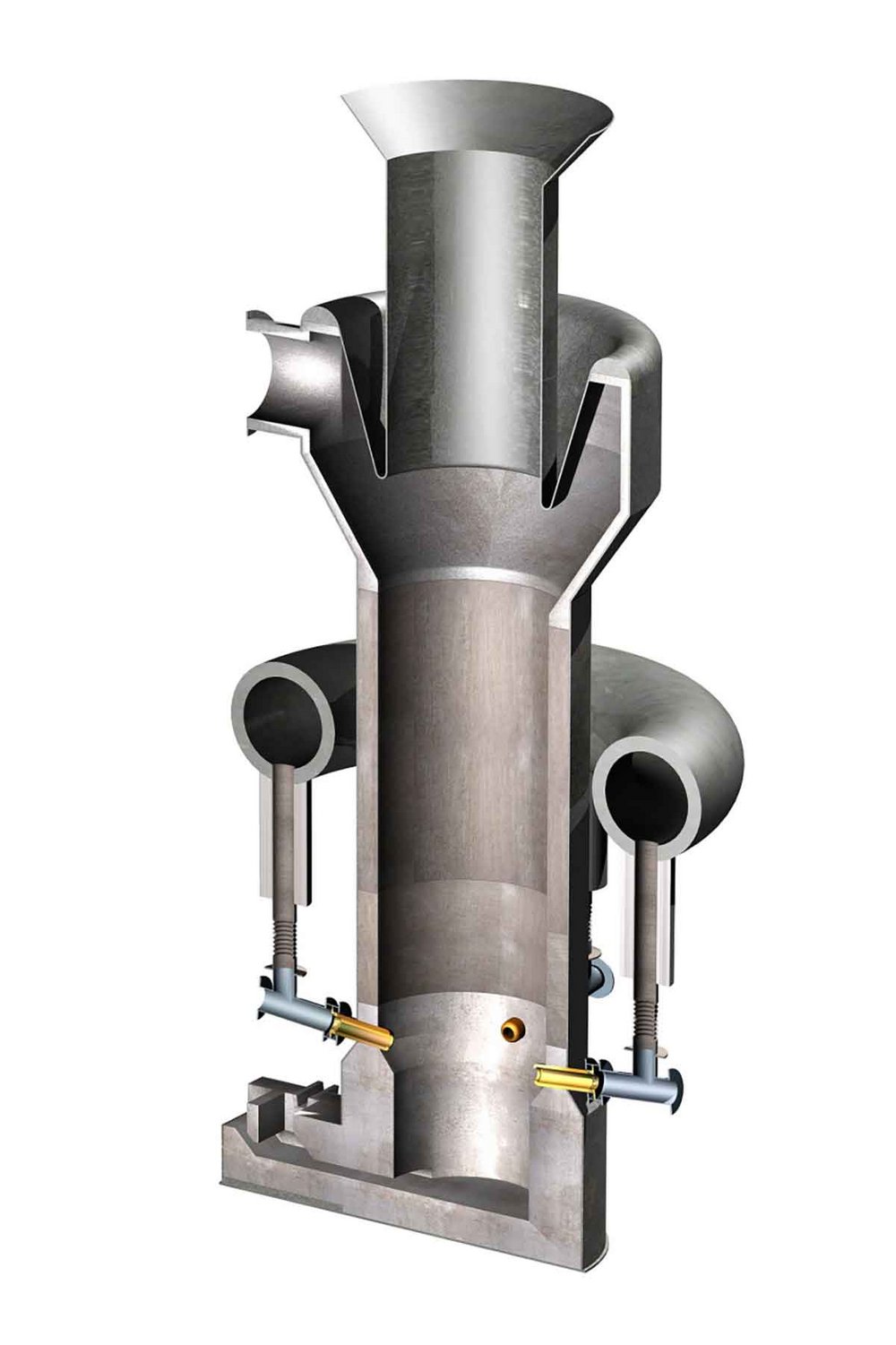
Long campaign cupola melting in iron foundries
Long campaign cupolas are the principal melting unit of most modern automobile and pipe foundries worldwide.
TRIAD Z 189 is a no cement castable based on high purity alumina aggregates enriched with SiC & Graphite. It does not contain dangerous metallic additives that can lead to Hydrogen Generation and potential explosion risk. The TRIAD Z 189 castable is designed for use in long campaign cupolas in the lower portion including the well, syphon, and taphole areas where most erosion occurs due to constant contact with high temperature iron and slag. Find out more
RAMWELL linings are an alumina based range of pitch-free, clay bonded, graphitised ramming material containing between 10% and 20% silicon carbide.
HYDRA-MAX linings are a range of ultra-low cement bonded castables based on fused and calcined alumina, containing between 15 and 55% silicon carbide and graphite. HYDRA-MAX refractories are pitch-free versions.
ULTRAGUN SC linings is a high performance gunning materials containing silicon carbide.
The final choice of products is determined by whether the furnace is a “lined” or “liningless” cupola and by operating conditions in order to improve
- lining performance
- slag resistance
- speed of installation
- dry-out time
- resistance to sculling
- metal cleanliness
- lining security
Channel holding and pouring furnaces in iron foundries
Channel furnaces are used in iron foundries to hold large quantities of iron melt between the melting station and the casting station. Pressure pour furnaces are used for holding iron at temperature whilst casting into moulds on an automated casting line.
Ultra-low cement technology with CRITERION and SPINCAST will bring extra performance, slag resistance by using high alumina and spinel aggregates.
Self-flowing cast DURAFLO, high alumina castable is a universal lining for both body and spouts with the added advantage of being self-flowing for ease of installation and sleeve repairs.
For the cover CERCAST mid alumina conventional castable with high volume stability and ease of installation or LITEWATE insulation castables for back layer insulation arerecommended.
Inductor boxes
Inductors for both channel furnaces and pressure pour furnaces are invariably lined with dry-vibratable materials.
MAGNAVIBE spinel-forming, magnesia based, dry-vibratable refractories are suitable for high powered inductors.
KELLUNDITE spinel-forming, alumina based, dry-vibratable refractories should be used for smaller inductors or as a universal inductor lining.
Linings for dosing and low-pressure aluminium furnaces
INSURAL precast furnace lining system
Traditional furnace lining systems involving the application of wet refractory mixes typically require time-consuming dry-out and sintering operations prior to metal charging. In addition to significant furnace downtime, such lining systems also typically lead to hydrogen pick-up in the aluminium melt for the initial period following furnace installation.
The INSURAL furnace lining system, combining highly insulating and durable components, is the ideal solution for today’s aluminium melting operations. A dry, preformed engineered lining system.
Benefits include:
- No sintering or dry-out program
- Reduced furnace downtime
- Lower energy costs
- Improved melt quality
- Greatly reduced hydrogen evolution on start-up - rapid achievement of target melt density
- Low corundum growth - easy to clean and maintain
Foseco supplies a full range of consumable ceramic products for dosing furnaces, produced in a variety of INSURAL technical grades as well as other ceramic materials, for example:
- Filling funnels
- Dosing tubes
- Launders
- Thermocouple and Heating Element Sheaths
Traditional cast linings
Dosing and low-pressure furnaces are usually small and the cast furnace bath is done in a single pour. The bath linings can be cast in TRIAD AL or ALUGARD castable.
Many furnaces use crucibles to hold aluminium. The main advantage is that the crucible can be easily changed and casting can commence immediately, without the need for prolonged drying of the furnace linings and reducing the risk of hydrogen pick-up. Crucibles also ensure that the aluminium is uniformly heated through the crucible wall by electric resistance heating. Foseco offer a wide range of crucibles for all types of furnaces.
Challenges for high-pressure die casting (HPDC) foundries
The high-pressure die casting (HPDC) market is evolving as auto makers increase both the amount and complexity of aluminium parts involved vehicle production. The change brings new opportunities for HPDC foundries – but also new challenges. Foundry consumable suppliers such as Foseco have a key role in helping their customers overcome these issues and take advantage of the next stage in HPDC evolution. In this white paper, we discuss:
- Current trends in HPDC including lightweighting and megacasting
- The challenges posed by these trends
- How we are supporting foundries take the next steps in HPDC
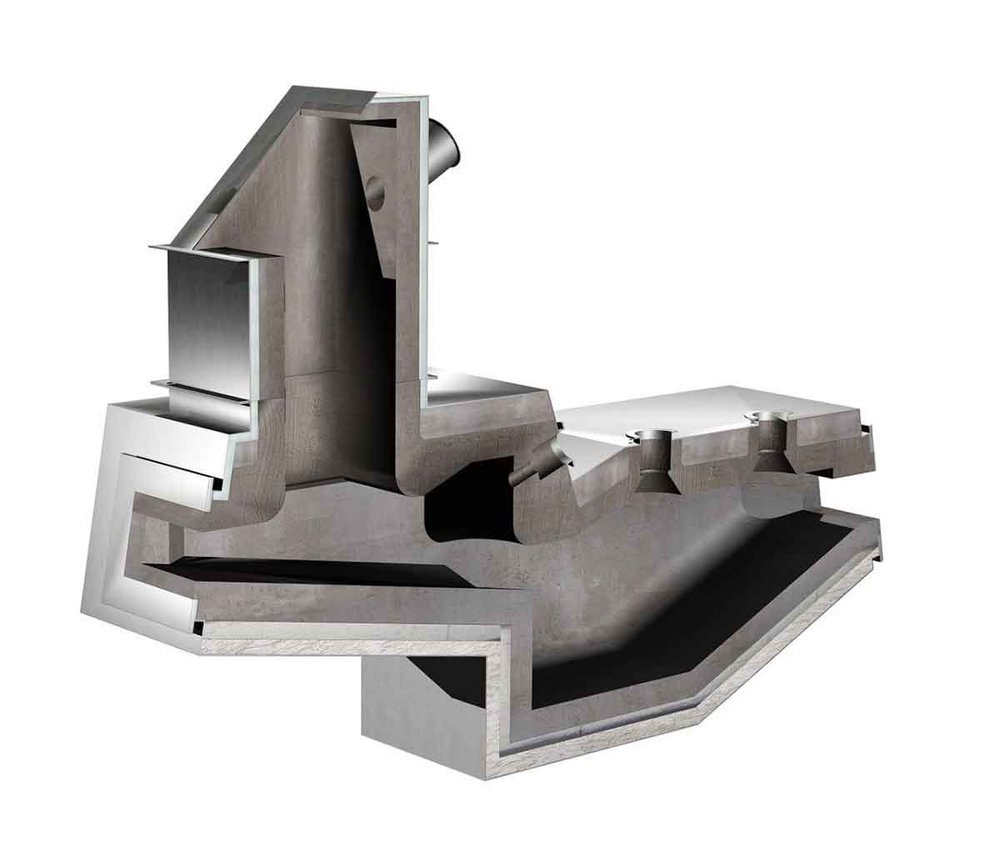
Linings for tower and reverberatory melting furnaces in aluminium foundries
Tower melting furnaces are commonly used in aluminium foundries. They consist of a vertical melting shaft with a connecting holding bath. Unlike tower melters, reverberatory furnaces are usually single chambered furnaces.
ALUGARD aluminium resistant castables are used to line these types of furnaces. There are a variety of grades, specifically developed for different applications and conditions found in aluminium handling and containment. ALUGARD materials are termed “non-wetting” due to their ability to “repel” molten aluminium, resulting in no reaction between the metal and the refractory.
TRIAD AL high alumina cement-free castable offers exceptional resistance to aluminium wetting and penetration. It has all the characteristics of normal TRIAD castables:
- Easy to mix
- Easy to install
- Reduced bake-out time.
The product is suitable for all metal contact areas, including bath, lower sidewall, ramp and sill.