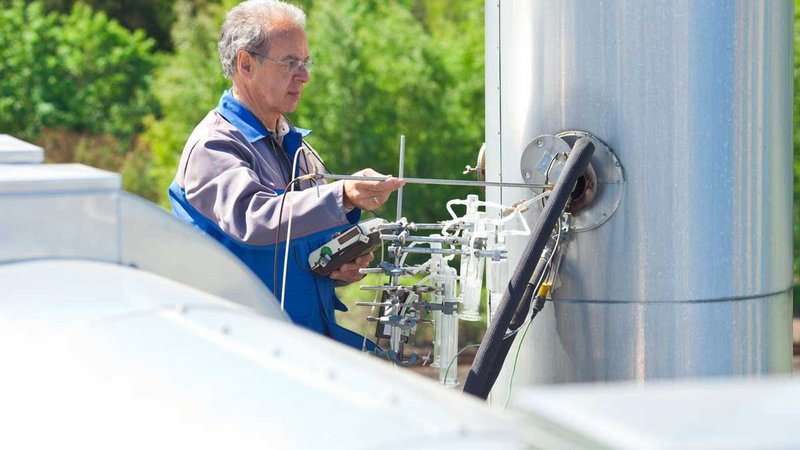
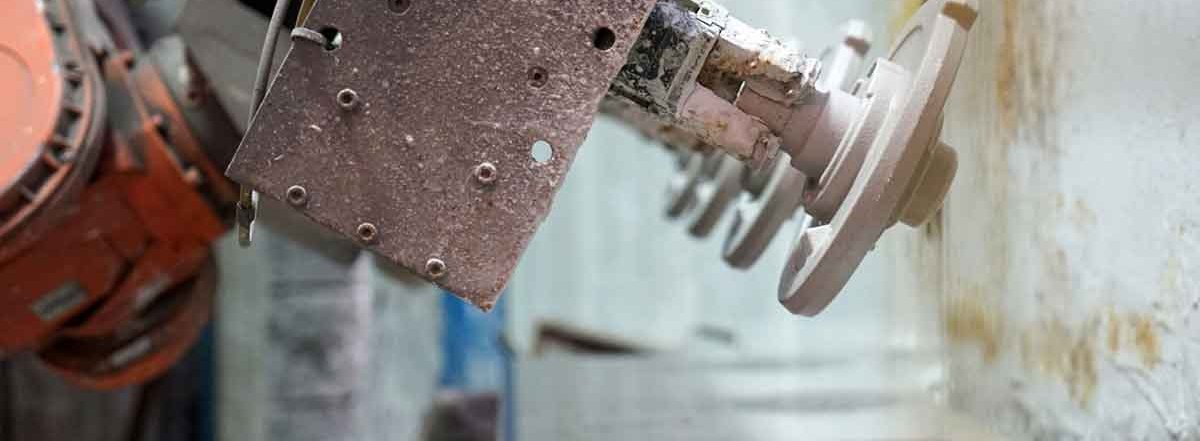
Coatings for high production cores and moulds
- High insulation
- Excellent application characteristics
- Controlled penetration of refractory fillers into the core substrate
- Refractory filler selection for superior casting quality
SEMCO water-based coatings
Water-based coatings are a more environmentally-friendly alternative to solvent-based coatings, but this brings new challenges, most notably the susceptibility of water-based coatings to attack by microorganisms such as bacteria and fungi.
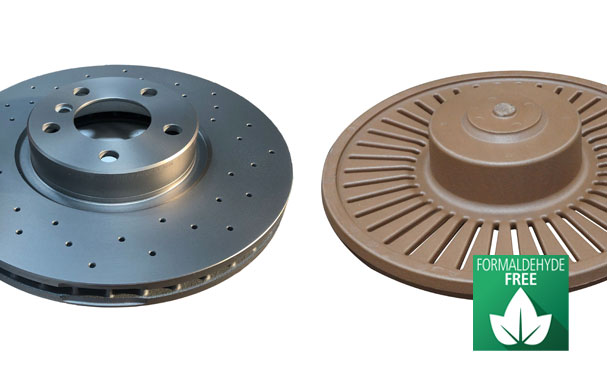
SEMCO FF water-based coatings reducing formaldehyde emissions
SEMCO FF coatings are designed to eliminate evolved formaldehyde; reducing foundry emissions and supporting foundries’ compliance with the latest EU regulations. SEMCO FF coatings do not use biocides that release formaldehyde, especially within the coating drying process, when emissions are most concentrated. They therefore support foundries in complying with the new regulations and avoid the need for costlier and more complicated investments in new or upgraded gas treatment systems.
Find out more about reducing formaldehyde emissions from water-based coating
SEMCO CC water-based colour change coating
SEMCO CC water-based coatings with colour change on drying technology support the optimisation of the drying process; energy costs can be saved, CO2 emissions are reduced and processing times minimised. Another advantage for the caster is that in case of high humidity, which has a negative influence on the actually dry cores, the colour of the cores will reverse. This colour indicator can be applied for almost all of our water-based coatings on a wide variety of binder systems. You can use this technology for cores and moulds in iron, steel and non-ferrous foundries.
Find out more about colour change coatings that help to reduce energy costs
SEMCO IC inner cleanliness coatings for the latest engine technology
SEMCO IC coatings are focussed on delivering “Inner Cleanliness”, these coatings will help automotive foundries to deliver the increasing quality demands specified for the next generations of emission-reduced and performance-enhanced internal combustion engines. SEMCO IC removes remaining particulate in all complex channels of engine blocks and heads most efficiently and hence leads to longer lasting oil or cooling liquids in an engine. This results in extend engine performance and at the same time reduced emissions.
Find out more about coatings supporting the transition to lead-free bearings
Supporting the transition to lead-free bearings in large diesel engines: the challenge for foundries
The EU has restricted the use of lead-containing bearings in diesel engines. This poses a challenge for engine makers, who traditionally used lead in bearings to achieve satisfactory engine reliability. Its qualities as a dry lubricant protected the bearings from particulate contaminants, such as those left over from the casting process (moulding sand, and residues from the binder and the coating itself).
To support the transition to lead-free bearings, SEMCO IC coatings are designed to significantly improve the removal of such casting debris from even the most complex of castings. In doing so, these coatings continue to set new standards when it comes to the ultra-low number of particles remaining in the as-cast condition.
The latest generation of SEMCO IC coatings is also formulated so that any remaining coating particles are softer than the bearings. This eliminates the risk of wear to the bearing from coating residue.
RHEOTEC water-based coatings
RHEOTEC coatings are water based coatings designed for dipping of cores which are then oven dried. The coatings can be supplied as powders, concentrates or ‘ready-for-use’ slurries. They help to provide a clean ‘as cast’ surface finish on the internal passages of iron castings.
The RHEOTEC XL range of water-based coatings have been designed specifically by Foseco to address the needs of the foundry producing grey iron components, helping to eliminate sand expansion defects such as veining and finning, and reducing rework.
ACTICOTE water-based coatings
These coatings have been developed to actively influence the surface metallurgy of the casting:
ACTICOTE CG coatings for compacted graphite iron castings are designed to reduce the formation of flake graphite within the surface of the cast component, whilst also providing a highly refractory layer that prevents burn-on, metal penetration and other common casting surface defects. The use of ACTICOTE CG enables foundries to meet the design requirements for components cast in CGI and allows engineers to optimise component specifications to reduce weight whilst enhancing mechanical properties.
ACTICOTE TS coatings for thin walled grey iron castings are highly insulating, allowing for the pouring of thin sections at lower casting temperature and enabling a slower cooling that allows for better precipitation of the flake graphite. The use of ACTICOTE TS enables the production of light weight, thin walled complex castings.
TENO solvent-based coatings
TENO solvent-based coatings are available in a wide range of application rheologies and refractory combinations that offer superior performance for individual foundry requirements.
Coatings for green sand moulds
HARDCOTE SF800 is a water-based coating especially designed for green sand mould application. It helps to minimise mould erosions and improves the metal flow through thin castings. Typical defects such as metal penetration are suppressed, resulting in a smooth and burn-on free casting surface. The product does not require drying prior to casting.
HARDCOTE W100 is a water-based surface stabiliser for green sand moulds to prevent sand inclusions. HARDCOTE W100 is suitable for the spraying of greensand moulds for the production of light to medium sectioned castings. The product does not require drying prior to casting.
TRIBONOL powder coatings are a range of mould and core coatings for electrostatic deposition. The electrostatic method of application circumvents problems of solvent vapour, flash hazard and lengthy oven drying. It is a totally dry process.