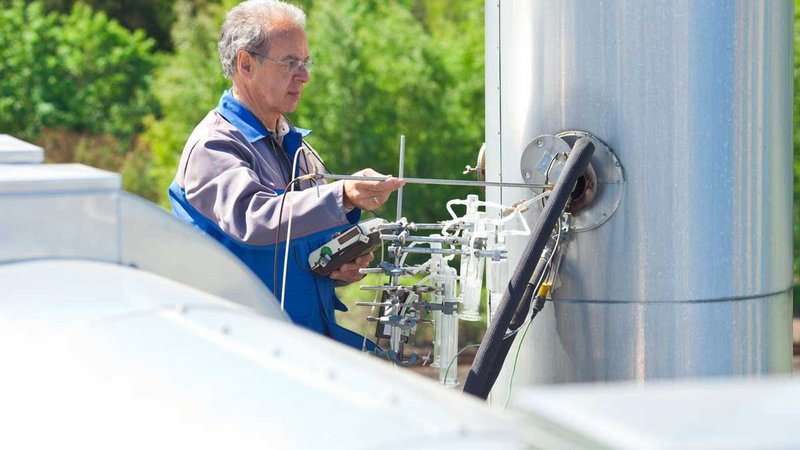
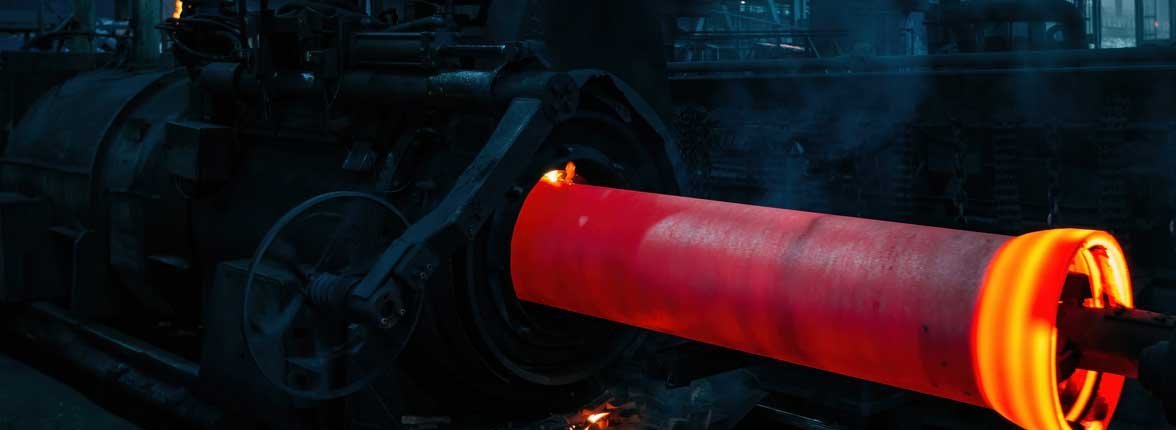
Centrifugal casting
What is centrifugal casting?
The use of centrifugal force in casting is not a new idea: artists of the 16th Century are thought to have used the technique to create castings with high clarity of detail. It wasn’t until the early 19th Century, however, that the first centrifugal casting machine was developed by Englishman, A.G. Eckhardt.
By the middle of the century, the process appears to have been adopted by German industrialist, Alfred Krupp, to cast wheels for railroad cars. In the 20th Century, the technique was applied to the manufacture of cast iron pipes, and the casting of pipes continues to be a major application of centrifugal casting today.
The centrifugal casting process
The defining feature of centrifugal casting – also known as spin casting and rotational casting (rotocasting) – is the use of a rotating mould, which throws the molten metal against the mould wall. This allows the casting of pieces with rotational symmetry, such as pipes and rings, wheels and pulleys, although asymmetrical pieces can also be produced.
Types of centrifugal casting processes
There are three types of centrifugal casting methods:
- True centrifugal casting
- Semi-centrifugal casting
- Centrifuging or centrifuged casting
True centrifugal casting
True centrifugal casting uses a hollow, cylindrical mould, rotated about a vertical or horizontal axis. It is used for the production of hollow, cylindrical castings, without the use of a central core, since the metal is held around the wall of the mould by centrifugal force during solidification. The thickness of the casting is thus controlled by how much molten metal is added to the mould.
At the same time, the rotational force drives out gaseous inclusions from the melt, eliminating porosity defects and producing castings with a dense structure. Light non-metallic inclusions are driven to the inner surface and can be removed by machining.
A final feature of true centrifugal casting is direct pouring into the mould, without the need for gates and runners. This results in very high yields that can reach up to 100%.
Both vertical and horizontal techniques can be used to cast a range of non-ferrous and ferrous materials. Horizontal moulds are generally used to cast long cylindrical shapes, e.g., rolls, pipes, sleeves, tubes or liners. Vertical moulds are used for shorter castings, e.g., rings or bearings, as well as non-cylindrical and specialty pieces, such as cones, valves and propellers. The use of mould inserts is also possible with vertical moulds, allowing the production of castings with flanges, bosses or other types of surface detail,
True centrifugal casting will generally use permanent dies, which must be properly prepared before casting. The inner surface of the die must be cleaned, heated and coated with a refractory between castings. The coating – such as SPUNCOTE coatings from Foseco – is usually sprayed onto the heated die to ensure even coverage, and has a range of jobs:
- Protecting the die from the molten metal.
- Controlling heat transfer and solidification rate.
- Acting as a release agent.
The coating will also help determine the outer surface texture. For example, cylinder liners for aluminium engine blocks require a textured outer surface. This can be achieved by post-cast machining; however, a speciality coating, such as SPUNCOTE SP from Foseco, can be used to produce an appropriately-textured surface on the as-cast piece. Finally, the coating should be formulated to leave as little residue in the mould after casting. This keeps die cleaning times to a minimum, speeding up cycle times and improving productivity.
Once coated, the molten metal is poured into the rotating mould via a pouring spout. This spout should be lined and coated to protect against the molten metal, should be pre-heated before pouring to minimise metal retention, and should be periodically inspected for any residual metal, slag or loose refractory that might break into the melt and cause inclusions.
An exothermic material may be added to the inner diameter after pouring to ensure unidirectional solidification from the outside in. When solidification is complete, the casting is removed from the mould for machining. Typically, the outside diameter will be machined to remove any surface roughness and to maintain concentricity with the bore, although in some applications an as-cast outer surface is acceptable (see above on SPUNCOTE SP coatings).
The inside diameter will be machined to remove the inner layer of the casting, where inclusions and porosity defects are likely to have formed (having been driven into the centre by the rotational force – see above) and to ensure cylindricity – particularly in vertical casts, which tend to form a parabolic internal diameter due to the competing effect of gravitational and centrifugal forces on the liquid metal.
A final note here: when casting alloys that are sensitive to oxygen exposure, e.g., nickel-cobalt super alloys, or when surface detail is a particular concern, centrifugal casting in a vacuum can be used.
Semi-centrifugal casting
Semi-centrifugal casting is a variation of true centrifugal casting where the mould is completely filled with molten metal, which is supplied through a central sprue. Parts cast using a semi-centrifugal process will retain rotational symmetry, but will not have the central, cylindrical void achieved by true centrifugal castings. It is most often used for casting pieces such as pulleys and wheels for tracked vehicles.
Moulds used in semi-centrifugal casting are more likely to be made of sand, than to be permanent dies. As with true centrifugal casting, the outside of the casting will have a dense, impurity-free structure. The quality will decrease toward the central section, which may be machined out. When a central bore is required, a sand core can be used.
Centrifuged casting (centrifuging)
Centrifuging is used when the benefits of centrifugal casting are required for non-symmetrical pieces. The molten metal is poured via a central sprue into the mould (usually sand); it then travels under force via radial runners and ingates to the mould cavities, which are located around the circumference of the mould. The cavities themselves could be any particular shape. The key is that molten metal is forced into them by rotation of the mould, ensuring even the most detailed or thinnest cavities are filled completely.
The rotational force continues to act on the casting during solidification, ensuring that gaseous and non-metallic inclusions migrate from the mould cavity, back toward the sprue, producing a dense, inclusion-free casting. When solidification is complete, the casting is knocked out and the runners/ingates – those areas where impurities are likely to have collected – machined off.
What is centrifugal casting used for?
Centrifugal casting is one of the more flexible casting methods. Both ferrous and non-ferrous materials can be cast in this way, as can duplex castings, where one metal is cast on the outside and another on the inside (e.g., combinations of hard and soft cast iron, carbon steel and stainless steel). It is also not a particularly expensive process, and is therefore popular in markets where good quality products are required at low manufacturing costs.
As a rough guide:
- True centrifugal casting is used to manufacture cylindrical pieces – from pipes to street lamp posts. Although the inner diameter will always be circular, external contours are not limited to circular forms: elliptical, hexagonal or fluted forms are possible.
- Semi-cylindrical casting is used to produce disc-like pieces, e.g., gears, fly-wheels and track wheels.
- Centrifuging is used to manufacture relatively small, intricately-detailed pieces, where the rotational force is needed to ensure complete filling of the mould cavity without inclusions.
- High quality with few (if any) inclusions or porosity defects
- High strength castings due to high density, uniform grain structure
- Can be used for a wide range of casting applications and metals/alloys
- Reduced rejects and machining costs
- No cores required to create hollow cylindrical shapes
- No need for gates or runners, increasing yield
- Very large parts can be produced with horizontal moulds
- High output
- Lower equipment and manufacturing costs than other casting methods
- Inner diameters will need machining for accuracy, surface finish and to remove areas of defects
- Not suitable for casting alloys prone to specific gravity separation, such as lead-bronze
- Limited to cylindrical-type forms
Foseco products for green sand foundries
- High exothermic spot feeder sleeves
- Exothermic-insulating feeder sleeves
- Insulating sleeves
- Direct pour technology
- Exothermic powders
- Filters for steel castings
- Filters for iron castings
- Filters for aluminium and copper castings
- Metal treatment products for ferrous alloys
- Equipment for ferrous metal treatment
- Metal treatment products for non ferrous alloys
- Equipment and consumables for non ferrous melt treatment
- Ladle linings
- Furnace linings
- Stoppers & nozzles