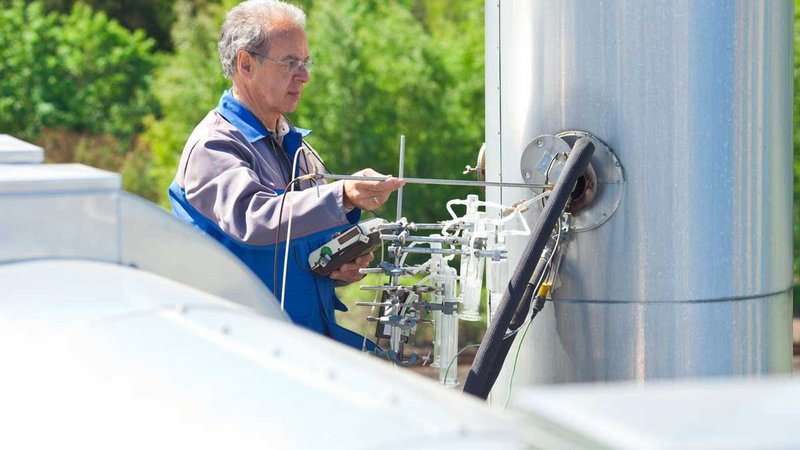
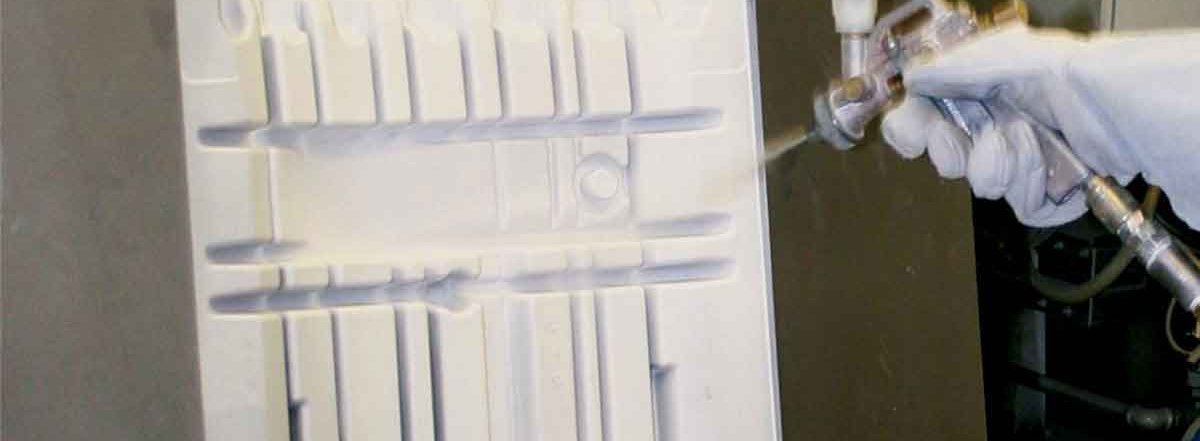
Die coatings for permanent mould casting
- Equal filling of the die
- Controlled heat transfer
- Good surfaces of the castings
- Long life time
Compared to sand moulds, the use of a permanent metal mould requires completely different conditions for filling the metal alloy and for its solidification; the function of the die coating – a semi-permanent layer deposited on the walls – is to control these processes and to facilitate release of the casting, prolong die life, etc. In die casting, coating selection and its method of application are at least as important as other factors, such as the design of the die, type of alloy, temperature of the metal and so on.
Standard DYCOTE die dressings
DYCOTE permanent mould coatings are blends of insulating and/or lubricating refractory materials with inorganic binders. They are formulated to meet a wide variety of performance and production requirements such as insulation, durability, surface texture and lubricity.
Foseco’s DYCOTE range of die dressings are suitable for gravity and low pressure diecasting of aluminium and other non ferrous alloys.
DYCOTE DURA long-life die dressings
DYCOTE DURA are a range of two-part die dressings with a novel binder system and are available in a range of grain sizes to meet the different casting, surface finish and insulation requirements. The adhesive characteristics and erosion strength of the coating can increase lifetime by a factor of 3.
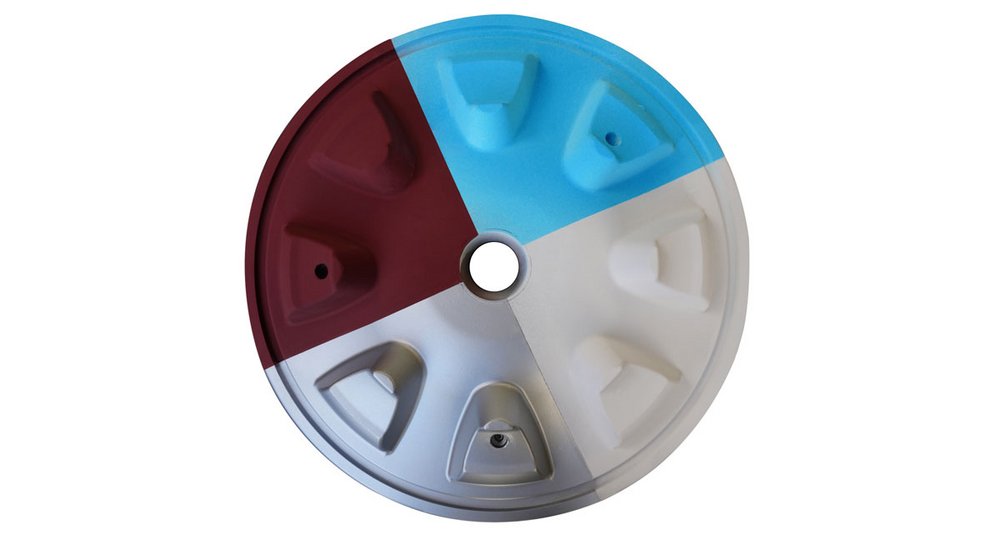
DYCOTE SAFEGUARD
DYCOTE SAFEGUARD products are nano-ceramic coatings designed to be applied on top of existing insulating DYCOTE base coatings, and have been proven to increase lifetime by up to 300%. Best results are achieved when applying DYCOTE SAFEGUARD using the Foseco DYCOTE SPRAYGUN which ensures consistent and uniform coating layer application.
The longer lifetimes achieved with DYCOTE SAFEGUARD coatings reduces the need for production interruptions to touch up and replace the die coating, thereby reducing downtime and maximising productivity.
CARRY & MIX system
CARRY & MIX is a mobile unit designed for the preparation of DYCOTE die dressings. The unit provides users of DYCOTE with a simple and clean method of mixing the coating, maintaining the quality during standing and loading the spray unit..
The coating can be applied using several methods:
- Brush
- Spray
- Immersion
For dies the quickest and most suitable method is spray application. Brush application is reserved for plain areas (runners and risers) where the lining must be much thicker, or for small details that must be coated in a different way from the rest of the die. Immersion application is mainly used for copper alloys, where the coating also has to cool the die.