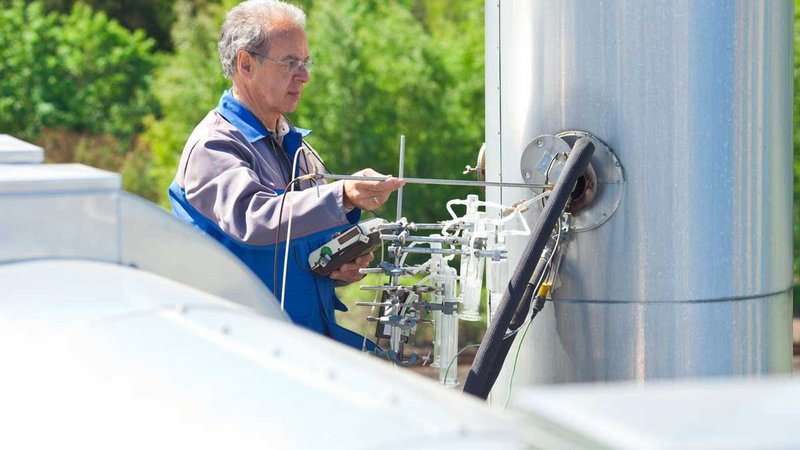
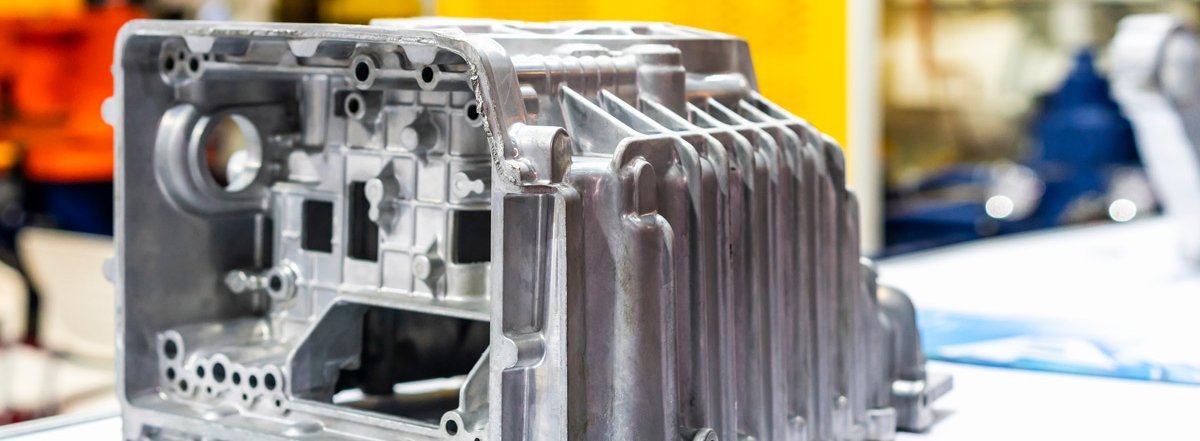
High-pressure die casting
What is high-pressure die casting?
Die casting involves the use of a permanent mould (or die), instead of expendable (or lost) moulds made from sand or wax. Since its development in the mid-19th Century, die casting processes have evolved from simple gravity-fed systems to systems in which the molten metal or alloy is injected into the die under pressure.
These pressurised processes originally operated at low pressures of around 0.1MPa/14.5psi. Advanced through the 20th Century, however, gradually increased the pressures involved, and modern high-pressure die casting (HPDC) machines can now operate at pressures up to 100MPa/14500psi.
Die design is crucial to the success of a HPDC process. Not only must the die be manufactured to the correct dimensions, it must also be able to withstand the large forces involved. For this reason, HPDC dies are made of high-performance tool steels. The runners and gates, as well as the die heating and cooling system, must also be carefully designed to facilitate optimal filling and die temperature control, which ensure high production rates can be achieved.
Dies come in two halves, one moving and one fixed. Ejector pins ensure the die is correctly assembled for each casting, as well as facilitating the release of the moving half after the casting has solidified. Due to the high pressures involved in the process, the two die halves must be locked together during the injection and solidification stages. More complex designs can also be manufactured via the use of hydraulically-activated loose-pieces or through a three-plate tool design.
The HPDC process
HPDC systems are highly-automated processes, and are designed for fast cycle times (less than one minute). Insulating refractory linings of the dies are therefore not used in HPDC processes (unlike in low-pressure and gravity die casting), as high heat transfer is needed to cool the casting as quickly as possible. The die must however be lubricated between each cycle to protect the die from metallurgical attack and erosion by the molten alloy, as well as to prevent seizing of the HPDC machine and facilitate removal of the casting. Often a high dilution factor is used; the high water content helps to accelerate cooling of the die surface.
Metal is usually melted in a bulk furnace, before being transferred by ladle to individual holding furnaces at each die casting machine. From the holding furnace, the molten metal is automatically metered into a sleeve, which holds sufficient metal (a shot) to produce one casting. A plunger forces the molten metal into the die, where it is held, under pressure, during solidification. The pressure is then released, the die is opened, and the casting ejected.
Due to the high dimensional accuracy of HPDC castings, post-cast processing is minimal, if required at all.
What is HPDC used for?
Although HPDC dies are expensive, they can have a life of more than 100,000 casting cycles. This makes the process most suitable for long-run applications. Couple this with the very fast production rates, and HPDC is an attractive option for mass production casting processes, such as those used for the manufacture of aluminium auto components. Indeed, HPDC dominates the aluminium casting sector, accounting for the production of a majority of aluminium castings worldwide, where it is used for the production of large-volume, lightweight, near net-shape casting applications.
What is the difference between HPDC and low-pressure die casting?
How is the HPDC process developing?
As casting demand from the light vehicle market evolves through electrification and light-weighting, the HPDC sector has seen growing focus on alloy development, melt preparation techniques (e.g., through appropriate degassing treatment cycles), die designs and process controls. The aim is to reduce internal defects, improve heat-treatability, raise the resultant casting properties, such as elongation and fatigue, and so expand the range of applications for which this casting method can be deployed.
Melt cleanliness is crucial to these trends. Various melt treatment products are available from Foseco that help in this regard, including degassing, modification, melt cleaning, covering and drossing fluxes, and melt transfer equipment. In addition, furnaces must be kept as clean as possible to avoid contamination. Selection of appropriate lining systems is thus an important concern for modern, high-performance HPDC processes, with options including:
- ALUGARD aluminium-resistant castables for melting furnaces are non-wetting and inert in contact with liquid aluminium, resulting in a clean furnace lining and optimum refractory life.
- INSURAL insulating linings offer a range of benefits for the holding furnace, including significant energy savings, improved melt quality (low corundum growth and hydrogen pick-up) and ease of installation and cleaning.
- High-volume, high-speed process
- High casting precision, surface finish, and uniformity
- Minimal post-casting processing
- Low costs per piece
- Casting of very thin wall sections possible
- Fully automated
- High tooling costs
- Susceptible to gas porosity defects
- Challenging to heat treat
- Limited coring, meaning complex internal geometries are not possible
Foseco products for HPDC foundries
Challenges for high-pressure die casting (HPDC) foundries
The high-pressure die casting (HPDC) market is evolving as auto makers increase both the amount and complexity of aluminium parts involved vehicle production. The change brings new opportunities for HPDC foundries – but also new challenges. Foundry consumable suppliers such as Foseco have a key role in helping their customers overcome these issues and take advantage of the next stage in HPDC evolution. In this white paper, we discuss:
- Current trends in HPDC including lightweighting and megacasting
- The challenges posed by these trends
- How we are supporting foundries take the next steps in HPDC
Further reading
Brown, J.R. (ed.), Foseco Non-Ferrous Foundryman’s Handbook (Butterworth Heinemann; 2000), Chapter 9: Pressure diecasting of aluminium alloys, pp. 108-117