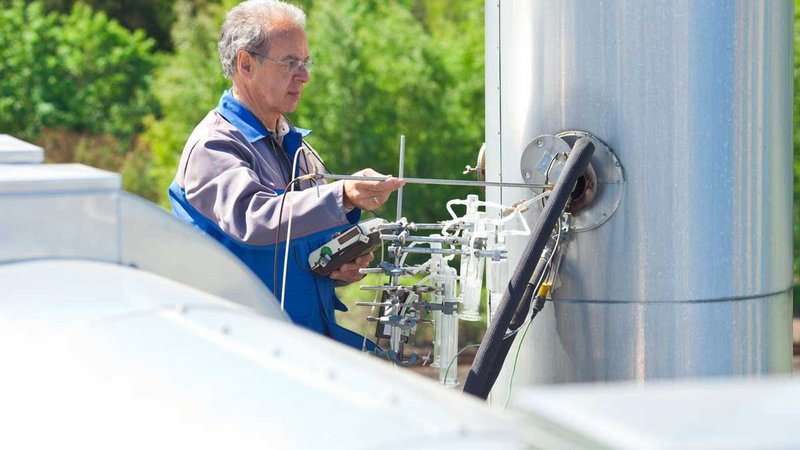
Innovation - It's in our DNA
The history of Foseco is a story of innovation. In Birmingham, UK in 1932, Eric Weiss and Dr Kossy Strauss set up Foundry Services Ltd – the company that would become Foseco. Dr Strauss was a chemist, and with Eric Weiss on the commercial side, their mission was to provide products and services that truly supported the foundry industry.
Together with Vesuvius, Foseco have developed and introduced countless innovations to improve the profitability and performance of the foundry industry established a number of process technologies that are common practice today. Before Foseco there were no insulating or exothermic feeding systems, no ceramic foam filters and no rotary degassing of aluminium melts.
Today, Foseco innovation is centred around the challenges facing the industry including:
- Sustainable product and process technologies to reduce waste, emissions and improve the working environment.
- Energy saving technologies to save costs, optimise melting and reduce carbon footprint.
- Process control technology and Industry 4.0 to optimise product application, improve casting quality and reduce the requirement for scarce labour resources.
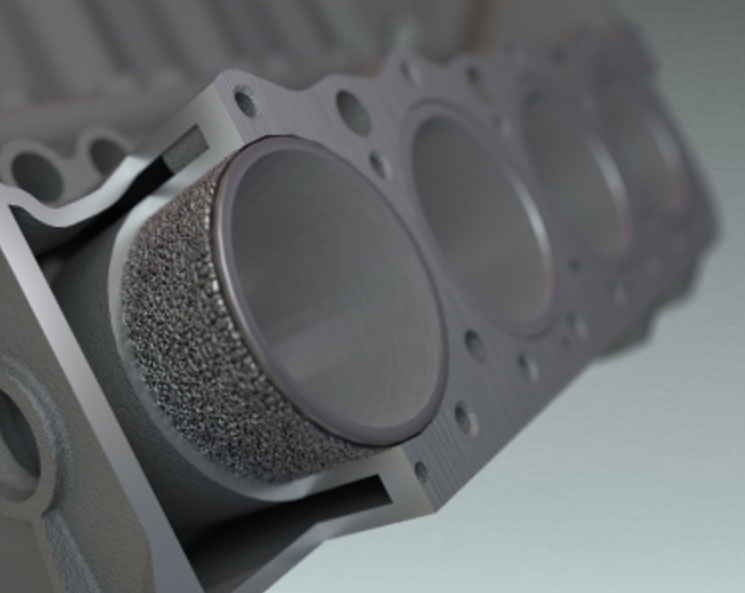
Our latest innovations
All Foseco products are born from the need to find better ways of producing better castings more efficiently and economically, and are the result of close collaboration with foundry operators the world over. Our approach is built on close personal relationships where it matters most - on the foundry floor. Our aim is simple: We have developed the most comprehensive and innovative product and service portfolio in the business and we want our customers to gain real economic value from these developments.
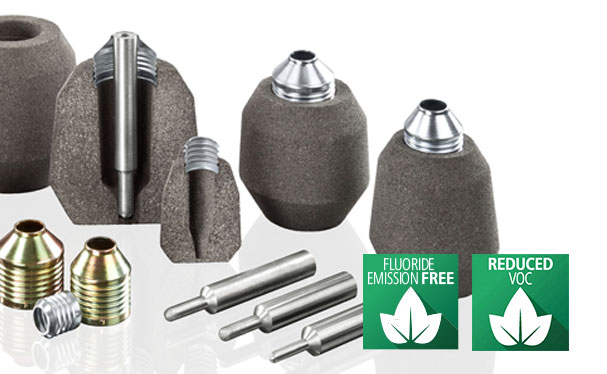
Sustainable solutions
We are committed to growing its contribution to a sustainable world, through products and services that improve safety, maximise environmental performance, reduce greenhouse gas emissions, and contribute to the circular economy. Our products have the potential to help customers reduce and avoid greenhouse gas emissions when compared with their current practices by amounts that far exceed the emissions required to manufacture and distribute them.
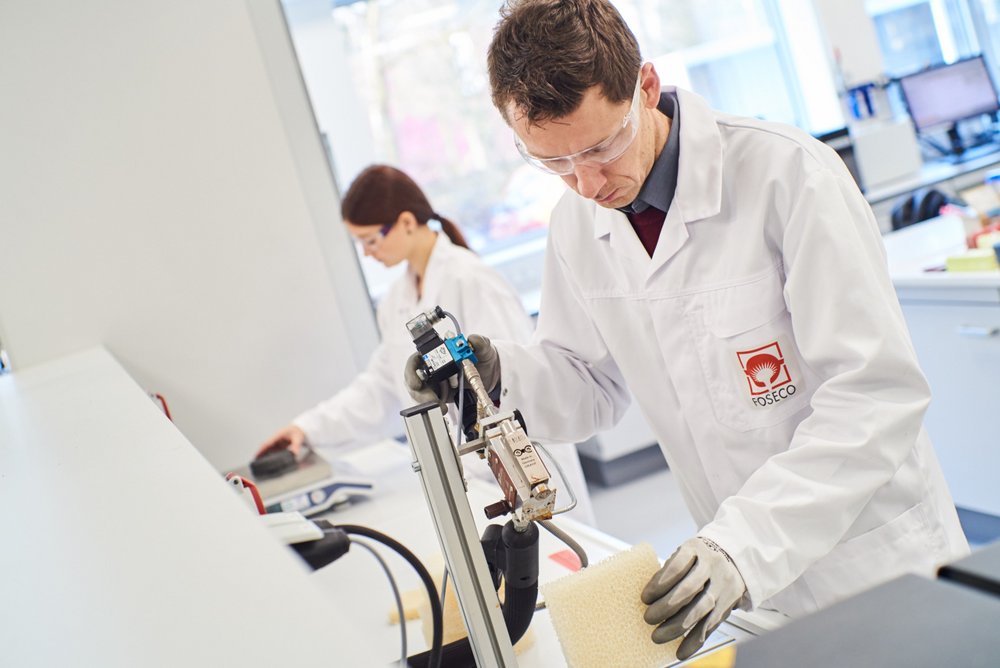
Research & development
Today, Vesuvius continues to lead innovation in the steel and foundry industries, with 17 research and development centres, including the Global Foundry R&D Centre at Enschede. The company has also established a technical services division to explore new ways of integrating continuous data capture into its solutions to give customers the insights they need.
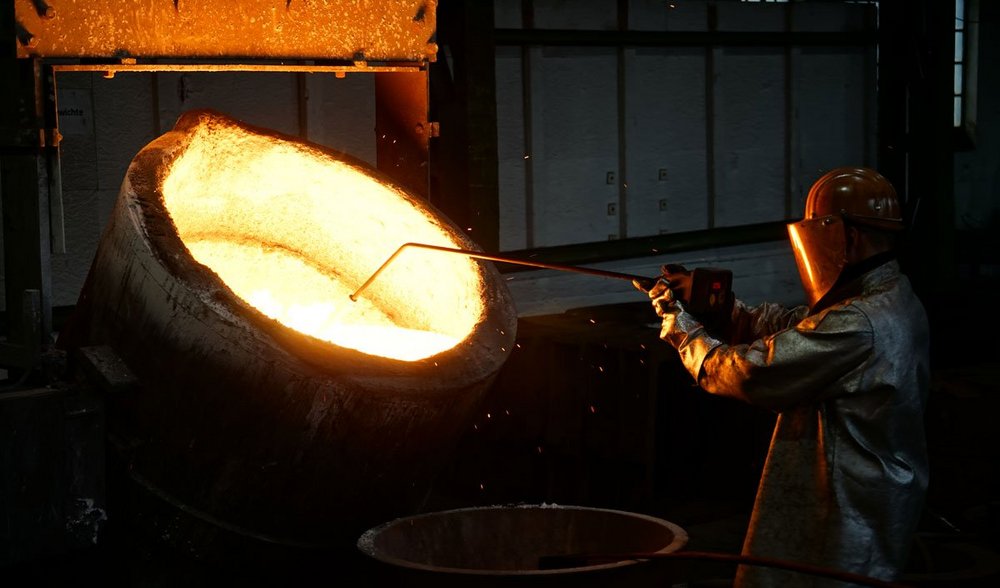
Energy efficiency
It is more important than ever for foundries to control and minimise their energy consumption costs in order to remain competitive. While the industry has long contributed to sustainability in some areas, notably through the recycling of iron, steel and aluminium scrap, there is still much room for improvement in other areas, such as increasing energy efficiency. Therefore, technologies and solutions that reduce energy consumption are becoming increasingly important. The good news is that today there are many ways to achieve this through the use of modern foundry consumables.
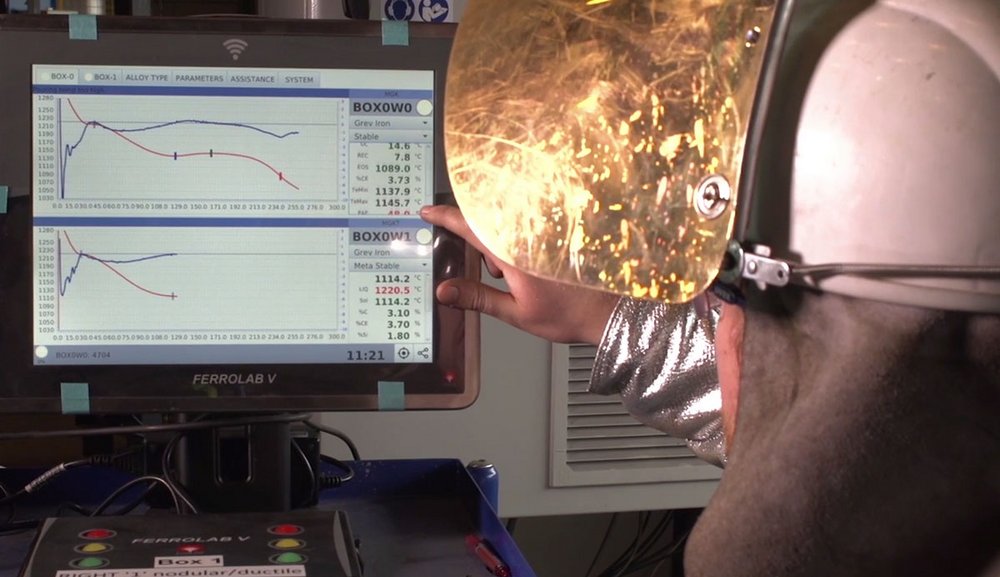
Process control and Foundry 4.0
Controlling the application of Foseco consumable products is vital to ensure optimum performance. Automation of process steps also reduces the need for operator involvement freeing up resources to be used elsewhere. This is an increasing area of focus for Foseco with examples such as:
- SMARTT fully automated Melt Treatment Stations for the degassing and treatment of aluminium alloys.
- Automated coating density control for consistent coating application and surface finish by use of the Intelligent Coating Unit.
- The Foseco Pro module to be used in combination with MAGMASOFT ® casting simulation software to ensure the correct application of Foseco sleeves and filters in the production of new and improved casting applications.
- FERROLAB V sophisticated thermal analysis software tool that leads to uniform iron quality, less variation in the properties of castings and ultimately allows a reduction in the amount of castings rejected.