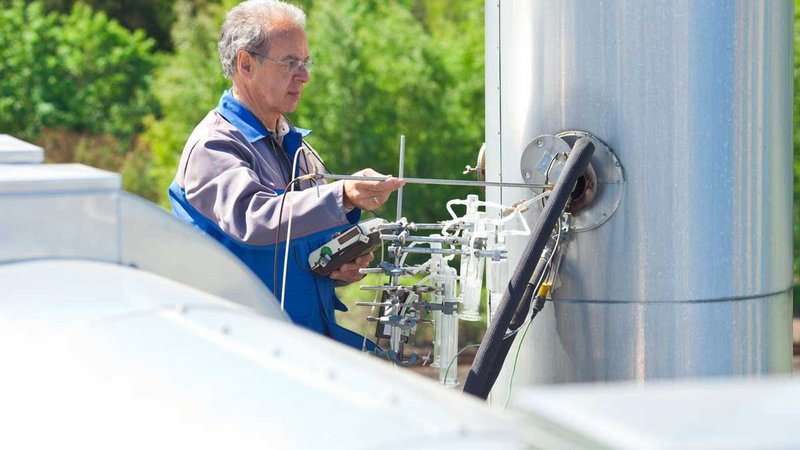

Green sand casting process
Green sand casting: an introduction
A centuries-old casting method, green sand casting continues to be one of the most commonly-used casting methods for both ferrous and non-ferrous casting today.
Due to its flexibility and low cost, green sand casting processes are used to produce a wide range of casting products – from engine blocks and components to frying pans and manhole covers, and almost everything else in between.
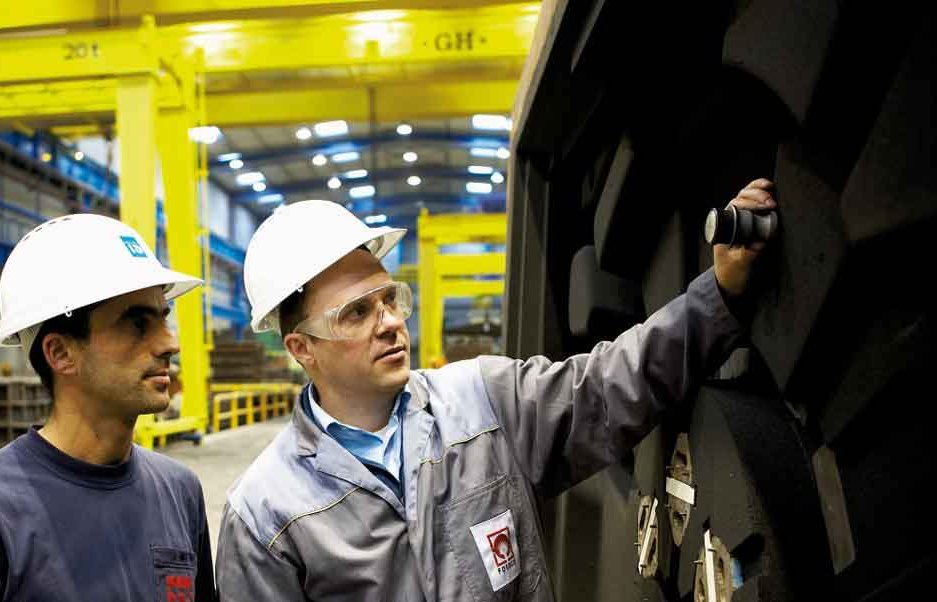
The green sand mould
Green sand moulds are made using a moist, clay-bonded sand, alongside various other additives. Typical green sand moulds contain a base sand, usually a high-silica (SiO2) sand with a clay bonding material (bentonite) and water.
The sand grains themselves should be relatively spherical to facilitate flow and compaction of the green sand mix during the mould making process. Average grain size should be about 220-250 μm with a maximum fines content below 2% to ensure a good surface finish, at low binder levels, while also providing sufficient gas permeability to allow the escape of steam and other gases during casting.
In addition, anthracite (coal) dust is traditionally added to increase the refractoriness of the green sand mix, improve mould permeability, ease stripping and achieve a higher surface finish, although this is not required when casting aluminium.
More recently, coal dust replacements have been developed that are easier to handle (no dust) and result less emissions during casting. Other additives and binders may be used to increase the strength and toughness of the green sand, or to provide superfine surface finish.
Non-silica sands are used for some specific casting applications. For example, zircon (Zr SiO2) sand is used with chemical binders for high-quality steel casting and for some critical iron castings. Zircon sand is also used for the Cosworth® sand casting process, which is used to cast aluminium alloys with high dimensional accuracy, high strength and density. Chromite (FeCr2o4) sand has a natural chilling properties and is used to avoid expansion defects in steel casting, while olivine (MgSiO4) sand is used for the production of austenitic manganese steel castings.
Traditionally, green sand moulds have not been coated. However, the growing need for an effective coating solution to improve cast surface quality has led to the development of HARDCOTE SF800 coating. Specifically designed for the high speed production lines commonly used in the manufacture of grey and ductile iron castings, and occasionally other alloys, this innovative product integrates seamlessly into the production environment, enabling the surface coating of moulds without compromising productivity.
A final note about the name: it is the moisture, not the colour, of the sand that gives the process its name. Like freshly-cut ‘green wood’, which retains its natural moisture, ‘green sand’ is uncured, and still contains a large amount of water when the molten metal is poured in.
The green sand casting process
Or more accurately, green sand casting processes, as there are a number to choose from. What is common to all, however, is that the green sand mix is compressed and a casting pattern impressed into that hardened block. How this is achieved can vary, with both vertical and horizontal moulding options available.
Horizontal green sand moulding
Horizontal green sand moulds – whether made via the traditional flask process or the matchplate (flaskless) – comprise two parts: the cope at the top and the drag at the bottom. In the flask process, the cope and drag are formed separately by compressing the sand onto the pattern; the cope is then placed on top of drag afterwards. In the matchplate process, the cope and drag are formed simultaneously in the same mould chamber using a double-sided pattern (the matchplate) that sits between the two halves as the chamber is filled with sand and compressed.
Vertical green sand moulding
In vertical green sand casting, a moulding chamber is formed by two pattern plates on either side, and filled with sand from above. The pattern plates then move together to compress the sand and form the mould. To release the mould, one of the plates moves out and up, allowing the mould to be pushed out of the chamber and into contact with the previous mould; this creates the moulding cavity. As new moulds are formed, the line of moulds (mould string) is pushed towards the pouring zone.
Pouring, mould removal and re-use
In both vertical and horizontal processes, interior surfaces are created by cores of pre-cured sand, which are placed into the mould before it is sealed and locked into place. These cores can be coated with a specifically-engineered coating, such as those offered by Foseco, to protect against metal penetration and burn-on defects, and to aid knock-out.
Molten metal is then poured into a pouring basin set in the top surface of the mould. It then flows down a funnel-shaped sprue and feeds into channels, or runners, which take the molten metal to the mould cavity itself via the in-gate.
Various feeding systems products are utilised to enhance the solidification time of feeders in order to avoid shrinkage defects and improve casting yields. Feeding systems are specific to the type of metal cast and available for cast iron, steel and non-ferrous casting applications. Ceramic foam filters help to reduce turbulence in the pour, which can result in re-oxidation and subsequent inclusions in the final casting.
When high end quality is a particular requirement, filtration systems may also be used to remove any remaining inclusions as the melt enters the mould. Both feeding systems and filtration ultimately help to improve casting yield, while reducing costs associated with fettling and clean-up.
A number of other channels will run from the top of the cavity to the top surface of the mould. The molten metal will flow up into the larger of these cavities, known as risers, during pouring, before contracting back into the mould cavity as it cools and solidifies. Narrower holes, or vents, allow gasses and air in the cavity to escape as the mould is filled.
When the casting has solidified, the sand is shaken off and cores pulled away. This process may be aided by a release agent, such as PARTISAL. In ferrous casting, a magnetic separator then removes any remaining metal particles. Screens are used to remove non-magnetic metallics, lumps of core and other unwanted materials, and the sand returned to a storage hopper for re-use. Regular addition of new sand and removed of burned sand ensures the green sand mix maintains performance.
- Suitable for most ferrous and non-ferrous metals and alloys
- Simple, low cost production
- High productivity
- Can handle complex shapes
- Flexible to a wide range of part sizes, shapes or weights
- Scalable for large production runs
- Automated mould production reduces process times
- Quick and easy prototyping
- Limited dimensional accuracy
- More prone to casting defects
- Lower mould strength
- Moulds cannot be stored for long periods
Summary
Sand casting is ideal for small production batches. It also offers great versatility in the design of the final casting. There are two types of sand that can be used in the sand casting process, either resin sand or green sand. Find out more about the resin-bonded sand casting process.
Recommended products for green sand foundries
To guarantee the best quality and low maintenance in green sand foundries, we always recommend "link to product" to use as the perfect feeder sleeve.
- High exothermic spot feeder sleeves
- Exothermic-insulating feeder sleeves
- Insulating sleeves
- Direct pour technology
- Coatings for high production cores
- Coatings for jobbing cores and moulds
- Equipment to apply coatings
- Speciality coatings
- Filters for steel castings
- Filters for iron castings
- Filters for aluminium and copper castings
- Gas-setting resins
- Moulding material
Further reading
Brown, J.R. (ed.), Foseco Ferrous Foundryman’s Handbook (Butterworth Heinemann; 2000), Chapter 12: Sands and green sand, pp. 146-166.
Brown, J.R. (ed.), Foseco Non-Ferrous Foundryman’s Handbook (Butterworth Heinemann; 2000), Chapter 12: Sands and sand bonding systems, pp. 149-166