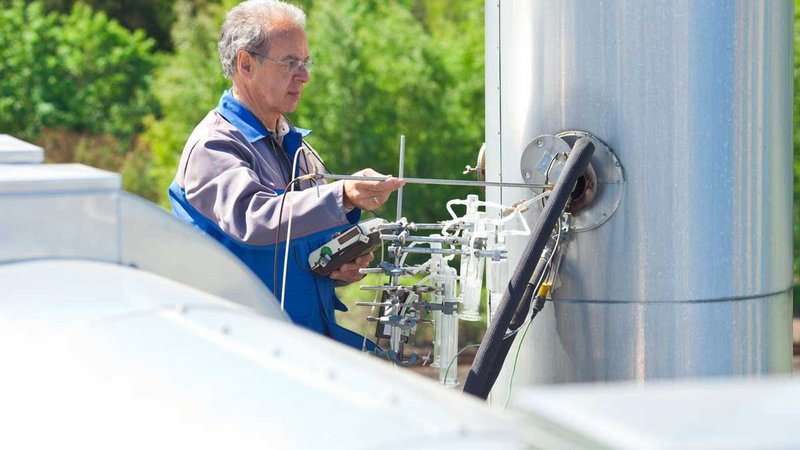
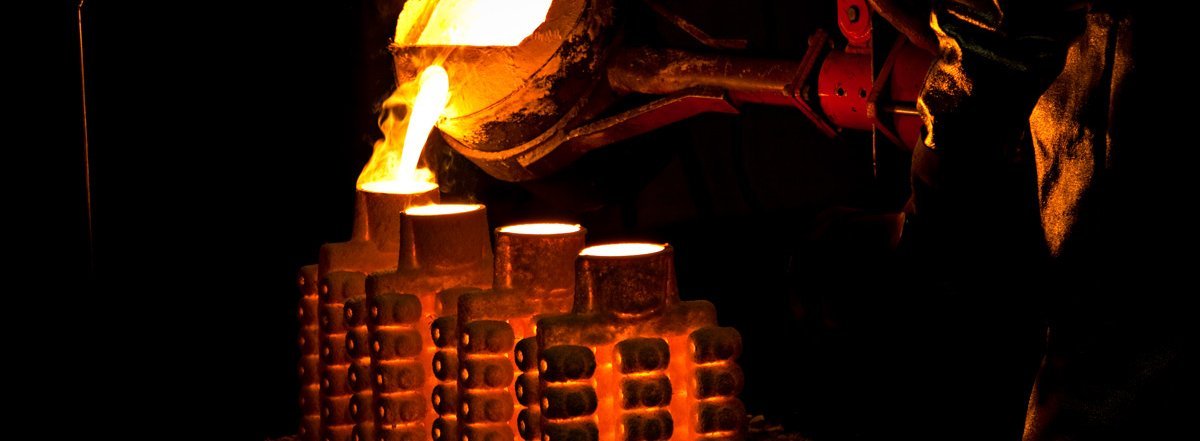
Investment casting process
What is investment casting?
Investment casting (or lost wax casting) has existed in various forms for millennia. Both ancient Egyptian and Chinese cultures used the technique to produce art and sculpture. Since the mid-20th Century, the process has been successfully adopted in the manufacture of high-performance engineering and medical components.
Modern investment casting moulds are made from a refractory ceramic material (e.g., alumino-silicates, alumina, silica or silica sol-bonded zircon) using an expandable wax pattern. When the ceramic has hardened, the wax is removed, leaving a ceramic shell; this shell then becomes the mould. The term ‘investment casting’ comes from the fact that the wax is ‘invested’ – in the archaic sense of being surrounded by or covered in – ceramic. The use of the expandable wax pattern means investment casting is also known as lost-wax casting.
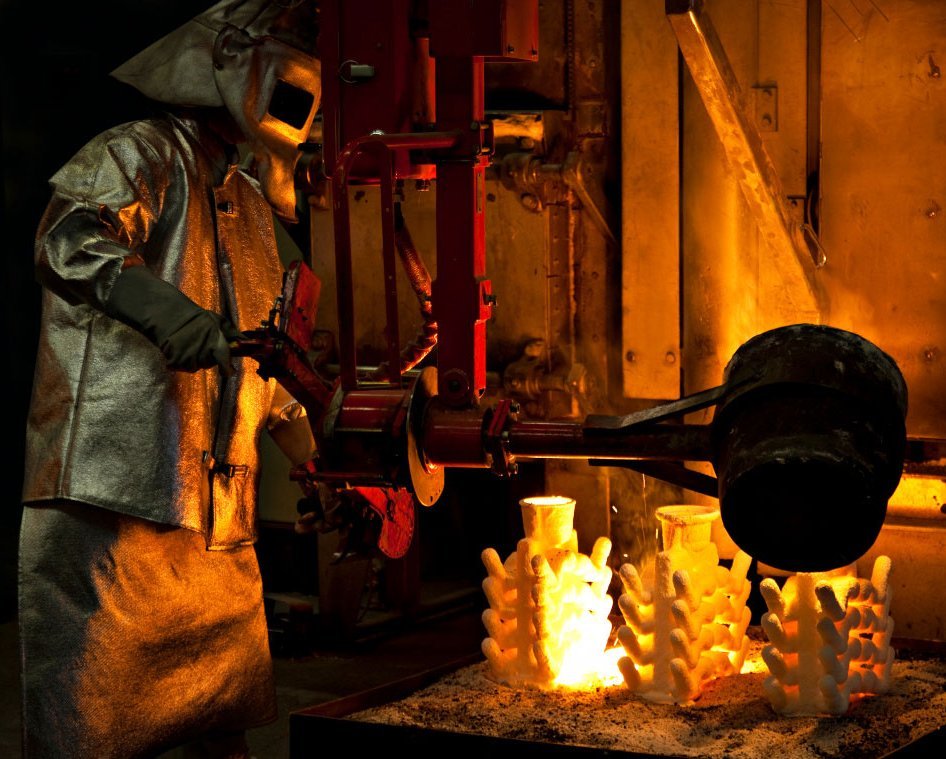
The investment casting process
The first step in the investment casting process is the production of a master die (or tool). Wax is injected into this master die to create the expendable wax patterns. Multiple patterns can be assembled around a sprue to form a ‘tree’, allowing multiple pieces to be cast simultaneously.
These wax pattern trees are dipped into a ceramic slurry, covered with a sand stucco, and allowed to dry. This process is repeated until a layered ceramic shell, with sufficient strength to survive the casting process, is created. The precise tolerances of the ceramic shell will depend on factors such as the size of the end castings.
When the ceramic shell has hardened, it is heated – usually in a steam autoclave – so that the wax melts and drains out. This wax can be collected, reconditioned and reused. Subsequent firing in a kiln burns off any residual wax, as well as curing the ceramic, to leave a mould suitable for pouring. The metal is poured while the mould is hot to ensure the melt does not solidify (or ‘freeze off’) before it has filled the entire mould.
After pouring, the metal is allowed to cool. The shell is then removed, usually by mechanical means in the foundry’s knockout operation. Mould and core debris may also be removed using caustic chemicals, although this approach is becoming less common due to the environmental and health challenges it poses. After knockout, the casting is cut from the tree (when used) and goes for cleaning/finishing and any post-cast treatment (e.g., heat treatments).
As the moulds are created from smooth wax patterns, as-cast surface finish is very high in investment casting. There is also no joining line, since investment casting moulds are single pieces. This contrasts with sand casting techniques, where the moulds are made of two halves. The need for secondary machining is therefore much lower than with some other casting methods, and may be eliminated altogether.
What is investment casting used for?
Investment casting can be used with a wide variety of metals, alloys and super-alloys – from stainless and carbon steels to aluminium, copper and brass, even glass. The ability to create complex castings, with high degrees or accuracy and surface finish, means it is ideal for producing high-quality components for high-tech and engineering applications, such as aerospace and defence, automotive, medical and orthopaedics, oil and gas, and power generation.
The use of investment casting in such highly-demanding applications, however, puts pressure on foundries to ensure stringent quality standards are met. High metal cleanliness and casting quality control are therefore vital elements of any investment casting process.
For example, the use of exothermic topping materials – such as FERRUX (for steel alloys, nickel/cobalt superalloys) and FEEDOL (for aluminium alloys) – helps the foundry control the thermal properties of the metal during cooling, preventing premature solidification and ensuring predictable feeding. Meanwhile, the use of high-efficiency filters – such as STELEX ZR or STELEX ZR ULTRA – removes impurities and improves casting quality, without negatively effecting the rate at which the mould is filled, a factor that had previously limited the use of filtration in investment casting applications.
- Applicable for most alloys
- Ability to accurately cast very intricate shapes
- Very high surface finish
- Reduced need for post-cast processing
- High casting integrity and mechanical strength (thermal creep resistance)
- Higher initial costs associated with die production
- Limited to smaller casting sizes
- More complex than other casting methods, requiring high precision control of the various processes involved
Distinction to other casting processes
Investment casting is a expendable mould casting process, as the ceramic mould is knocked out after the metal has hardened. In other manufacturing processes, the mould materials can be reclaimed to make another mould. This is the case with sand casting. There are two types of sand casting processes existing, either resin-bonded or green sand casting. The investment casting and lost foam casting process are quite similar in that they use patterns to create ceramic shells that hold the molten metal to make parts. However the materials to make the patterns are different.