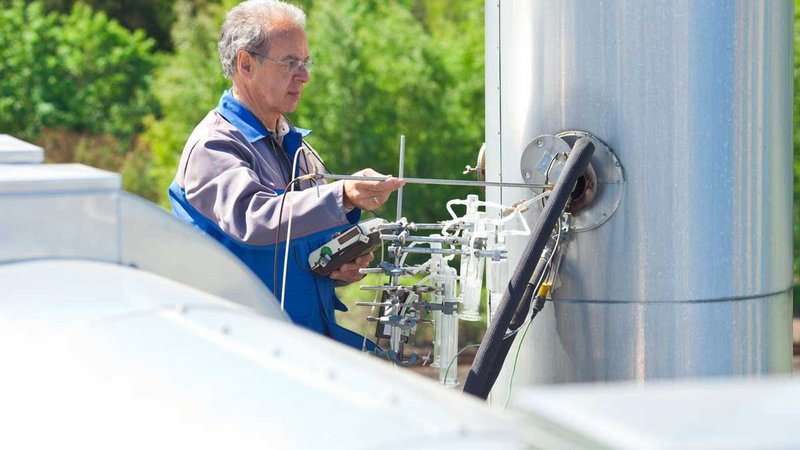
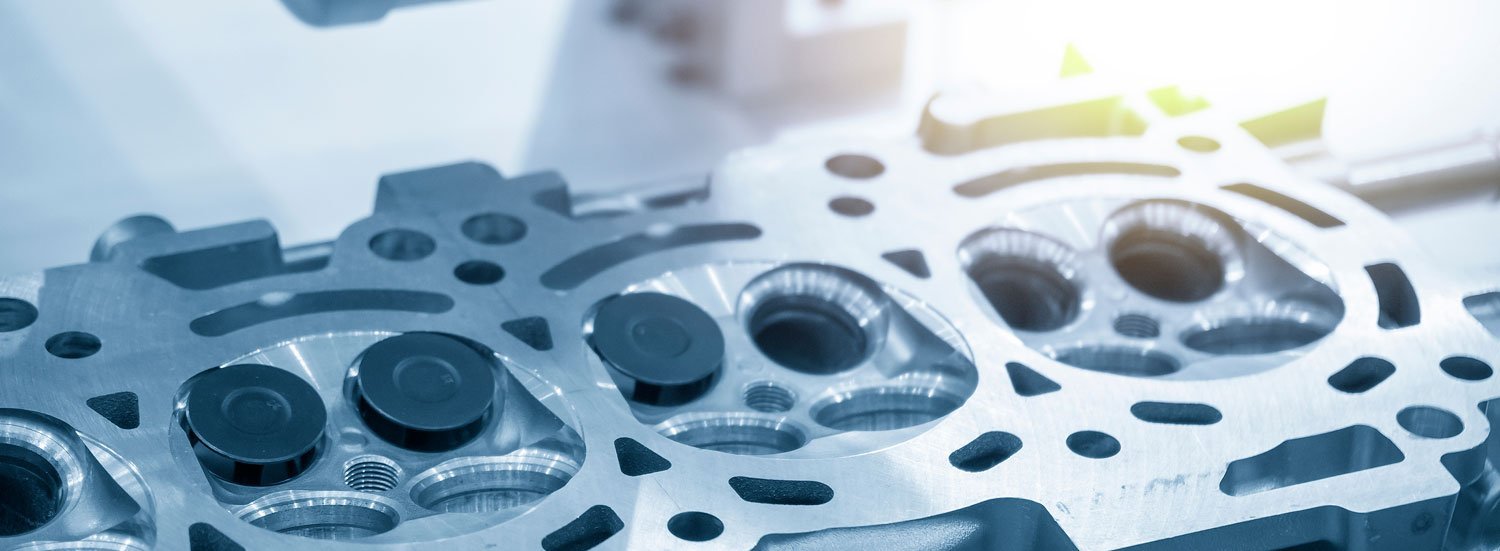
Gravity die casting
What is gravity die casting?
Gravity casting is one of the oldest known processes for manufacturing in metal and alloys. Its name simply refers to the fact that the molten material is poured into the mould under the influence of gravity alone.
Early, small-scale, artisanal gravity casting processes generally used an expendable mould material. The mid-19th Century, however, saw the invention of die casting, which utilizes a permanent mould (or die), manufactured from cast iron or steel. Unlike expendable moulds, dies can be used many thousands of times. Originally developed for the printing industry, gravity die casting has since been taken up for the mass production of high-quality castings for a range of industries.
Dies generally feature two sections, one of which will be fixed in place, and can be either vertically or horizontally parted. Whatever their design, dies must allow easy removal of the solidified casting, which may require multiple moving parts to facilitate the stripping of more intricate castings. Die design must also make provision for venting of the gases released during pouring, since – unlike expendable mould casting processes – the die itself in impermeable.
Permanent steel cores can be used for internal surfaces, and provide a fully-reusable (or full mould) process; alternatively, resin-bonded sand cores may be used. The combination of dye with sand mould is known as a mixed mould casting or semi-permanent mould casting.
When castings involve intricate, multi-part cores – such as cylinder heads – a core package may be preassembled and placed into the die to maintain cycle speed.
What is the difference between gravity and pressure die casting?
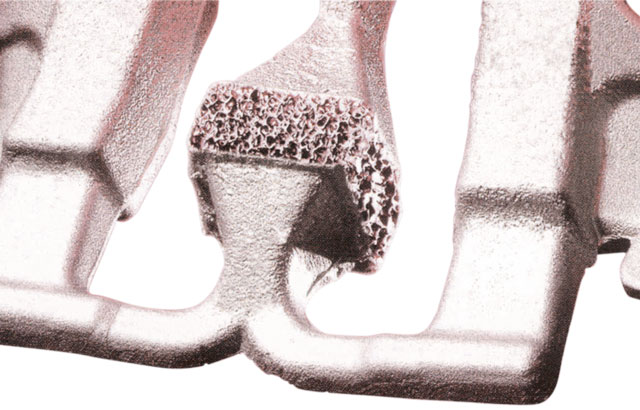
The gravity die casting process
Gravity die casting ranges from traditional hand-operated processes to carousel or linear production lines with automated die assembly and pouring. The process starts with preparation of the dies, which must be heated and sprayed with a refractory coating. Once the die is prepared and cores are loaded, the die is then closed ready for the pouring of the metal.
Traditionally, the melt is poured into the assembled die via a downsprue. A series of runners takes the molten material down and below the cavity, which is filled from the bottom. This method of filling helps reduce turbulence and frothing of the melt during the pour, and so preventing oxide inclusion defects, but it can create difficulties when it comes to achieving correct thermal gradients and directional solidification of the casting. The use of water cooling circuits and high conductive steels can help overcome this challenge, as can selection of the appropriate die coating (see below).
The use of ceramic foam filters such as SIVEX and SEDEX, is common in the runner bars as a means of controlling the metal flow to reduce turbulence and to prevent oxides and inclusions from flowing into the casting. SIVEX FC foam filters were especially designed for Aluminium alloys so that foundries can remelt their runner bars with Filters in-house. Contrary to silicon carbide filters, SIVEX FC filters will float into the dross when remelting runner bars, this leads to an easy removal of SIVEX FC from the melt without creating any detrimental inclusions. Strong cost savings arise from the use of SIVEX FC when making cylinder heads or larger Aluminium castings. Risers are normally designed into the part at critical locations to allow for liquid metal feed to areas of high mass to prevent srinkage related defects. Insulated feeders can be used to further enhance the solidification profile and the integrity of the final casting.
Alternatively, the use of these same foam filters and insulated feeders may allow for a direct pouring process. For example, the KALPUR unit from Foseco combines insulating feeder sleeves with SIVEX filters to ensure a consistent, steady flow into the dye, as well as ensuring optimum thermal gradient. KALPUR units also remove the need for a separate gating system, reducing material consumption per pour, and subsequent machining and remelting costs.
When the metal or alloy has solidified, the die is opened and the casting ejected. It is then processed to remove any sand cores from inside as well as the gates and runners (when present), before going for any additional treatment (e.g., heat treatment).
The importance of the die coating
The die coating (or dressing) performs several crucial roles and is formulated to meet the specific requirements of the casting. The general role of the coating is to:
- Protect the face of the die
- Ease release of the casting
- Control heat flow
- Provide good surface finish
- Lubricate the moving parts of the die
- Prevent build-up of residues on the face of the die
Controlling the flow of heat from the molten metal to the die is particularly important in die casting. Because the dies are thermally conductive, there is a risk that heat will be lost too quickly from the melt. This may result in cold defects, such as cold laps, seams and misruns.
Insulating die dressings, such as the DYCOTE and DYCOTE DURA products supplied by Foseco help control heat flow and ensure the metal completely fills the die at sufficient temperature to prevent defects. DYCOTE dressings also promote easy release of the casting from the die.
A coating is only effective, however, if applied in a controlled and consistent manner. Dies must be thoroughly cleaned before application, then heated to a uniform temperature, before the coating is applied. The coating mix itself must also be properly prepared. Systems, such as the Foseco “Carry and Mix” mobile unit, are available to provide a simple and clean method of mixing and maintaining the quality of the coating. For maximum control, the coating is usually sprayed onto the heated die, e.g., with a DYCOTE SPRAYGUN.
Although the use of cast iron or steel dies naturally ensures a high-quality of finish, this is somewhat impacted by the coating. For example, thinner, flatter surfaces need an angular dressing to facilitate good metal flow. This results in a rougher surface finish; however, a smoother coating could risk misruns in these areas. In heavier sections, less-textured coatings may be used and will usually last for several casting cycles before needing to be touched-up or replaced.
What is gravity die casting used for?
Gravity die casting is best suited to non-ferrous alloys with low melting points, such as alloys of aluminium, magnesium, zinc and copper.
Metals are typically fully treated in gravity die casting operations, for which Foseco offers a full range of products for degassing, grain refining and modification, and melt cleaning, covering and drossing.
- Good surface finish
- High mechanical properties (fine grain size and low gas porosity)
- Good dimensional accuracy
- Simple process (short cycle times)
- Lower tooling costs than pressurised die casting
- Consistent product quality
- Can cast a range of alloys
- Higher tooling costs than sand casting
- Lower wall thickness limit of 3mm to 5mm
- Unsuitable for casting alloys with high melting points
Foseco products for gravity die casting foundries
- Die coatings
- Direct pour technology
- Coatings for high production cores
- Coatings for jobbing cores and moulds
- Equipment to apply coatings
- Speciality coatings
- Filters for aluminium and copper castings
- Metal treatment products for non ferrous alloys
- Equipment and consumables for non ferrous melt treatment
- Ladle linings
- Furnace linings
- Crucibles and retorts
- Gas-setting resins
- Moulding material
Further reading
Brown, J.R. (ed.), Foseco Non-Ferrous Foundryman’s Handbook (Butterworth Heinemann; 2000), Chapter 12: Sands and sand bonding systems, pp. 149-166