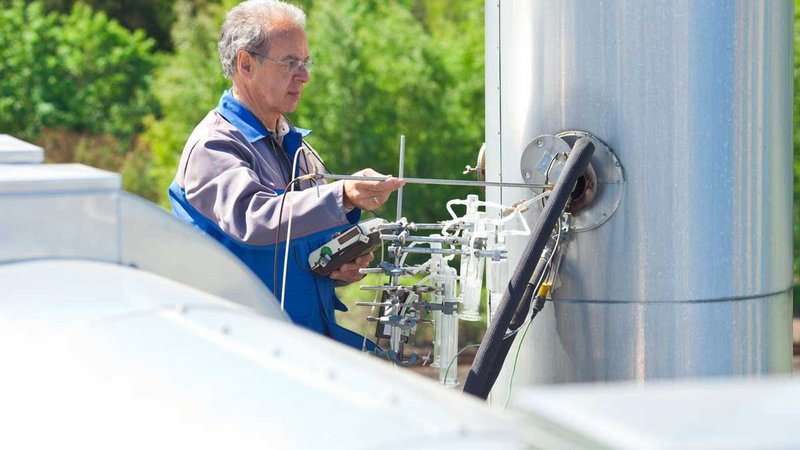
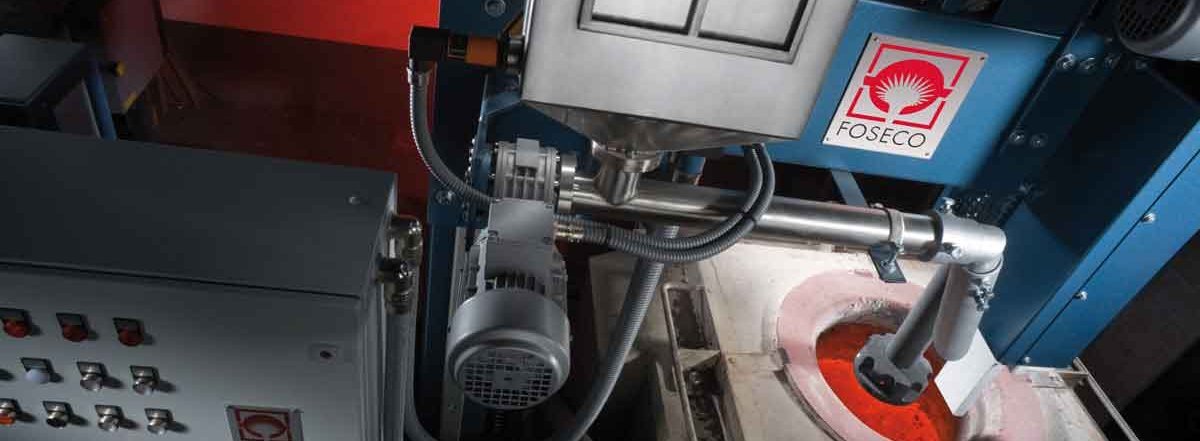
Equipment and consumables for melt treatment of aluminium alloys
- Hydrogen removal
- Oxides and inclusions removal
- Controlled upgassing
- Highly efficient rotor designs
- Reliable and consistent equipment
- Consistent mechanical and physical properties
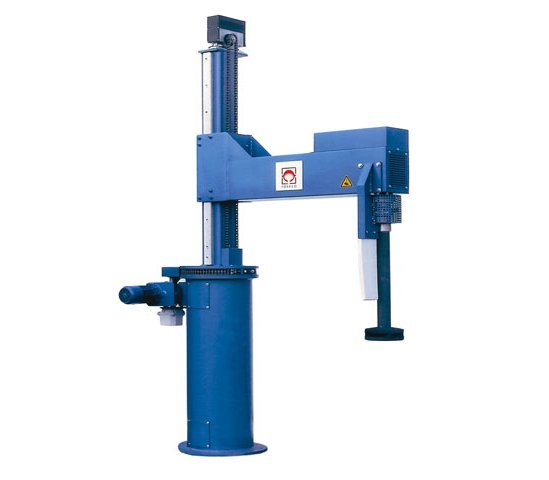
FDU rotary degassing equipment
FDU degassing units are an automated metal treatment system for the environmentally-friendly degassing and cleaning of aluminium and copper alloys.
FDU units use the impeller principle with a patented rotor which creates fine inert gas bubbles and mixes them with the melt. These fine bubbles are distributed homogenously throughout the melt without disturbing the surface maximising the contact area between the gas and the melt. The effectiveness of the Foseco FDU means that higher levels of degassing and cleaning can be achieved and treatment times can be reduced.
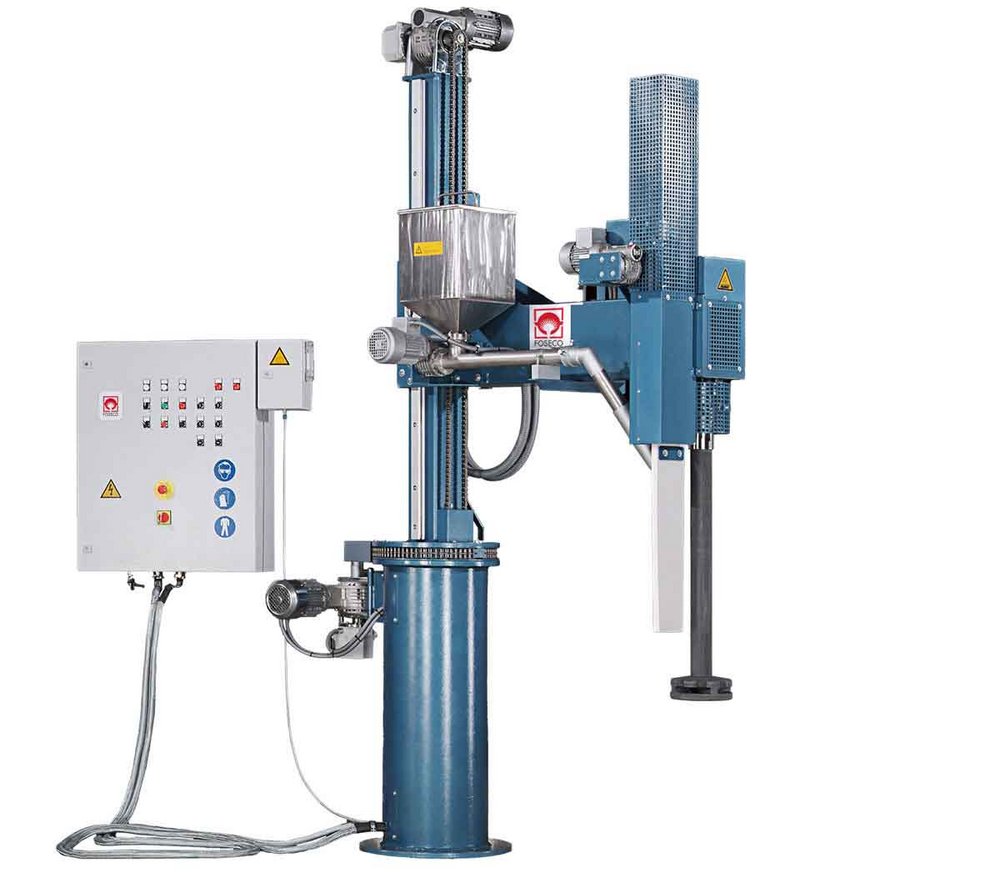
Metal Treatment Station (MTS) one-step automated treatment system
The MTS 1500 is based upon FDU rotary degassing technology, with the additional capability of adding a range of melt treatment products.
The addition of these treatment products uses a unique method, whereby the fluxes are fed from a dispensing unit into a vortex deliberately created by the spinning rotor. This vortex is carefully controlled to ensure a very efficient mixing of the treatment products.
Metallurgical benefits
- Improved melt cleanliness
Environmental benefits
- Using less consumables (flux, inert gas)
- Reducing the amount of dross produced
Health and Safety benefits
- Reducing operator involvement in the melt treatment process
Economic benefits
- Reducing treatment costs
- Improving performance
SMARTT Degassing
SMARTT Degassing is a software module for FDU and MTS devices that predicts the best treatment practice based on ambient conditions, melt temperature, rotor design and alloy composition.
The SMARTT software determines rotor speed, inert gas flow rate and treatment time and transfers this data to the degassing unit before treatment begins to ensure a constant quality level and reliable results for degassing and upgassing processes.
Challenges for high-pressure die casting (HPDC) foundries
The high-pressure die casting (HPDC) market is evolving as auto makers increase both the amount and complexity of aluminium parts involved vehicle production. The change brings new opportunities for HPDC foundries – but also new challenges. Foundry consumable suppliers such as Foseco have a key role in helping their customers overcome these issues and take advantage of the next stage in HPDC evolution. In this white paper, we discuss:
- Current trends in HPDC including lightweighting and megacasting
- The challenges posed by these trends
- How we are supporting foundries take the next steps in HPDC
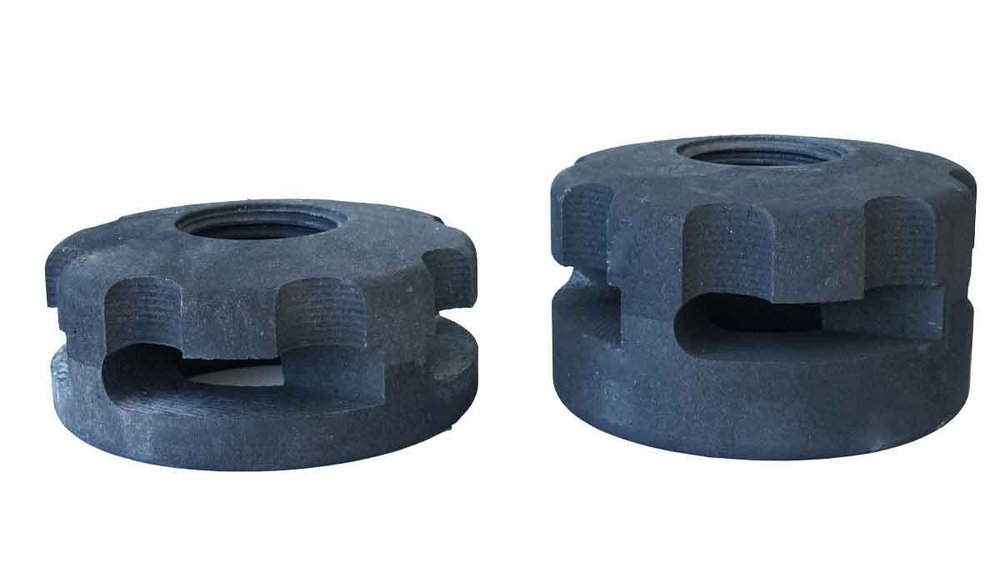
Graphite shafts and rotors
Graphite rotors are used in combination with the corresponding graphite shafts. Both rotors and shafts are vacuum impregnated to ensure a long life. Foseco’s high-performance, patented XSR and FDR rotor designs provide exceptional melt treatment.
XSR graphite rotor
The XSR rotor type can be combined with all graphite shafts. Turbo cuts in the upper section of the rotor further reduce the size of the inert gas bubbles thus maximising the surface area of the bubbles for a given volume of treatment gas.
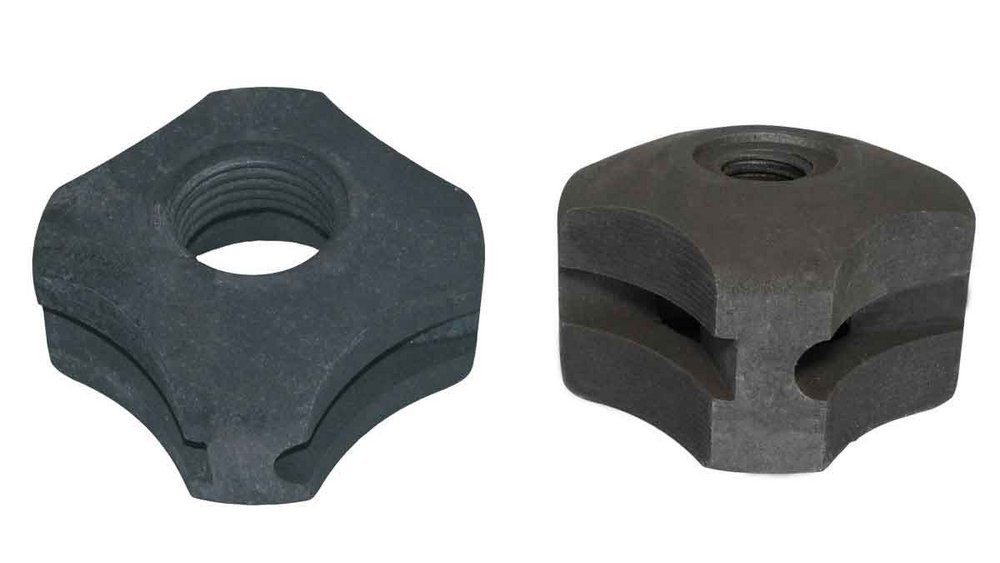
FDR high-performance rotor
The FDR rotor has been specifically designed to offer good degassing performance and optimal melt homogenisation during MTS 1500 application. Furthermore it is suitable for degassing of ladles or crucibles with difficult geometries.
The XDR and FDDR high efficiency rotors are a further development of the XSR and FDR range. They are characterised by a special design, whereas the additional rotor height offers a wide range of advantages. The degassing of the melt takes place with substantially higher efficiency. An additional advantage is the longer life of the rotor by reducing the rotor speed.
DIAMANT long life degassing consumables
While graphite is well-suited to aluminium degassing and treatment, the inherent sensitivity to oxidation leads to erosion of the parts, particularly in high production environments.
DIAMANT degassing consumables are produced using a new isopressed ceramic material that can achieve service life increases in excess of 200% compared to graphite in demanding, high production metal treatment applications.
DIAMANT consumables have been designed to retain the positive features of graphite degassing parts while enhancing oxidation resistance and strength.