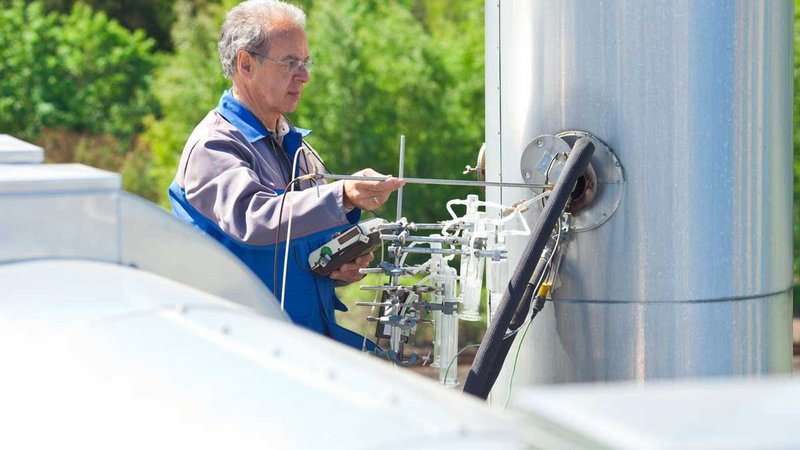
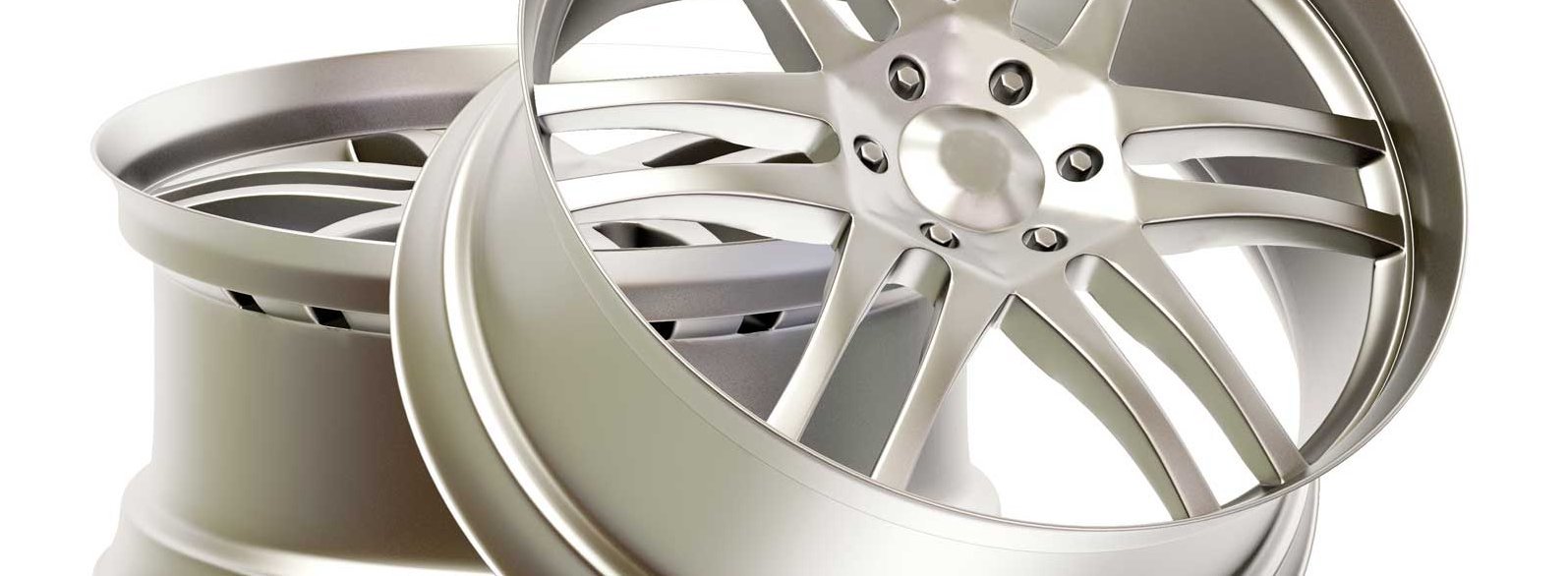
Low-pressure die casting
What is low-pressure die casting?
Die casting was invented in the mid-19th Century for use in the printing industry. In contrast to traditional casting methods, which used an expendable (or lost) mould of sand or wax, it used a re-usable mould, known as a die.
In the early years, die casting relied on the force of gravity alone to fill the dies; however, in the early 20th Century, low-pressure die casting (LPDC) was developed. In contrast to gravity die casting, the LPDC process uses low-pressure air (typically about 0.1 MPa/14.5 psi) to force the molten metal into a die.
LPDC dies are usually manufactured to be re-used over many thousands of casting cycles. The main frame is manufactured from cast iron, with areas of the die that are exposed to wear or concentrated heat normally made from hardened tool steel. Die design must also make provision for venting of the gases released during pouring, since – unlike expendable mould casting processes – the die itself in impermeable.
When the castings involved are more intricate – such as cylinder heads – a core package may be preassembled and placed into the die to maintain cycle speed.
Thermal balance is a crucial factor in LPDC die design, since the casting must solidify in from the extremities towards the riser (from which the molten metal enters the die cavity) in order to avoid shrinkage defects. Achieving this is perhaps the most challenging part of LPDC casting, and it is sometimes necessary to cool parts of the die with air or water to ensure correct solidification. Traditionally, this was something of a trial-and-error process, but modern simulation software now allows foundry engineers to accurately model solidification to ensure appropriate die thermal management.
What is counter-pressure die casting?
Counter-pressure casting is a variation to the LPDC process in which the pressure in the die is lowered (instead of raising the furnace pressure) to produce a pressure imbalance that draws the molten metal into the die.
The LPDC process
The LPDC process begins with preparation of the dies, which must be coated (or dressed) with a suitable refractory (see below). Dies are first heated, and then coating is sprayed on. The lower (fixed) part of the die is mounted to a base plate, and fixed to the top plate of the crucible. Corner tie bars on the base plate allow the other (moving) die half to be slid into place, and the two halves are clamped together. The die may also carry hydraulically-operated core pulls for the placement of core packages.
At this point, the die is ready to be filled. In the LPDC process, the dosing furnace is contained inside a pressure vessel. A riser (or stalk) is suspended from the furnace top plate down into the melt. When the melt has reached and stabilised at the required temperature, dry compressed air is injected into the pressure vessel via an inlet valve. This causes the molten metal to flow up the riser and fill the dye.
By carefully controlling the pressure, the flow of molten metal into the die can be managed for a smooth, turbulence-free fill. This reduces oxidation and porosity defects.
With the furnace under pressure, the casting solidifies quickly. The pressure is then released, and any molten metal remaining in the riser falls back into the crucible. The die is opened, and the casting released for clean-up and any additional treatment stages (e.g., heat treatment).
The importance of the die coating
The die coating (or dressing) performs a number of crucial roles, and is formulated to meet the specific requirements of the casting. The general role of the coating is to:
- Protect the face of the die
- Ease release of the casting
- Control heat flow
- Provide good surface finish
- Lubricate the moving parts of the die
- Prevent build-up of residues on the face of the die
Insulating die dressings, such as the DYCOTE and DYCOTE DURA range from Foseco, help manage the thermal balance of the die (see above). For example, on sections that require chilling, only a very thin layer is applied to allow maximum heat transfer. In contrast, thin metal sections will receive a thicker coating to ensure the molten metal retains sufficient heat (and thus remains liquid enough) to completely fill these areas.
A coating is only effective, however, if applied in a controlled and consistent manner. Dies must be thoroughly cleaned before application, then heated to a uniform temperature, before the coating is applied. The coating mix itself must also be properly prepared. Systems, such as the CARRY & MIX mobile unit, are available to provide a simple and clean method of mixing and maintaining the quality of the coating. For maximum control, the coating is usually sprayed onto the heated die, e.g., with a DYCOTE SPRAYGUN.
Although the use of cast iron or steel dies naturally ensures a high-quality of finish, this is somewhat impacted by the coating. For example, thinner, flatter surfaces need an angular dressing to facilitate good metal flow. This results in a rougher surface finish; however, a smoother coating could risk misruns in these areas. In heavier sections, less-textured coatings may be used.
Coatings will usually last for several casting cycles before needing to be touched-up or replaced.
Lining the riser and furnace
The riser is subject to continuous movement of molten metal. Lining system must therefore be robust enough to withstand the severe strains this entails. The DYCOTE range includes dressings formulated for extremely good resistance to erosion and the maintenance of a tenacious bond, while INSURAL precast refractory tubes, inserted into the riser, not only protect but also keep the liquid metal hot.
INSURAL precast refractory shapes are also available for the riser cap (nozzle) and for the furnace, where they have been shown to improve melt quality by minimising the formation of corundum. Depending on the chosen insulation concept, INSURAL furnace linings also offer the potential to significantly reduce energy consumption, and thereby the CO2 footprint of the process.
What is the difference between LPDC and high-pressure die casting?
What is LPDC used for?
LPDC is predominantly used to cast aluminium alloys. Typical applications include:
- Heavier/more complex automotive parts (e.g., wheels, cylinder heads, engine blocks, manifolds and housings)
- Critical aerospace castings
- Electric motor housings
Typically, metals are fully treated in LPDC operations, for which Foseco offers a full range of products for degassing, fluxing, grain refining and modification, and melt transfer.
- Complex geometries possible
- Good mechanical strength
- Good surface finish
- High dimensional accuracy
- Well-suited to automation
- Lower tooling costs than HPDC
- Slower casting cycles compared to HPDC (lower productivity)
- Higher tooling costs compared gravity die casting
- Unsuitable for casting alloys with high melting points
Foseco products for LPDC foundries
- Direct pour technology
- Coatings for high production cores
- Coatings for jobbing cores and moulds
- Equipment to apply coatings
- Speciality coatings
- Filters for aluminium and copper castings
- Metal treatment products for non ferrous alloys
- Equipment and consumables for non ferrous melt treatment
- Ladle linings
- Furnace linings
- Crucibles and retorts
- Gas-setting resins
- Moulding material
Further reading
Brown, J.R. (ed.), Foseco Non-Ferrous Foundryman’s Handbook (Butterworth Heinemann; 2000), Chapter 12: Sands and sand bonding systems, pp. 149-166