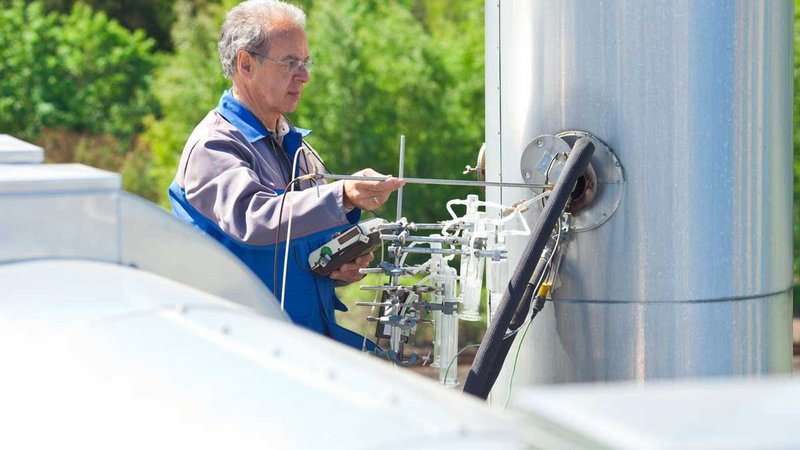
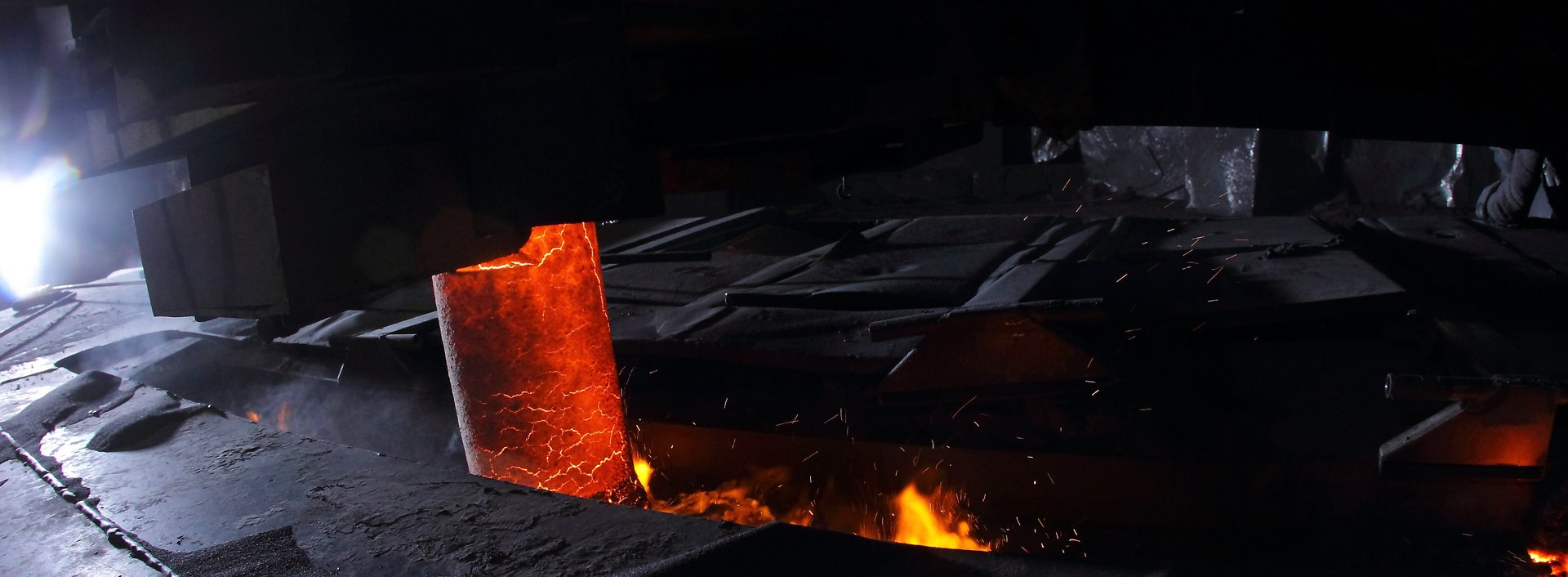
KALPUR direct pouring technology
- Higher yield from the elimination of running systems and hence a reduced metal requirement
- More room on the pattern plate for further castings or reduction in mould box size
- Enhanced directional solidification
- Less scrap, in-house and at the customer
- Reduced fettling and cleaning
- Reduced welding and repair
- Improved surface finish
- Better machinability
The KALPUR direct pour unit combines a filter and feeder sleeve into a single unit. Liquid metal is poured directly into the unit which connects directly with the casting cavity. The KALPUR process can be used for steel, iron and aluminium by choosing the appropriate feeder and filter types. It is suitable for hand-moulded castings, and horizontal and vertical automatic moulding lines. The KALPUR process eliminates the need for a conventional running system. In addition, by allowing the foundryman to pour directly into the casting, directional solidification is improved.
KALPUR for iron
KALPUR units for iron castings consist of a specially designed KALMIN insulating feeder sleeve or a KALMINEX exothermic/insulating feeder sleeve and a SEDEX or STELEX PrO ceramic foam filter. This allows castings to be successfully poured directly through the feeder.
KALPUR for steel
KALPUR direct pouring units for steel castings consist of specially designed KALMIN or KALMINEX feeder sleeves and STELEX PrO or STELEX ZR ceramic foam filters. The choice of filter will depend on alloy, casting temperature and filter capacity considerations.
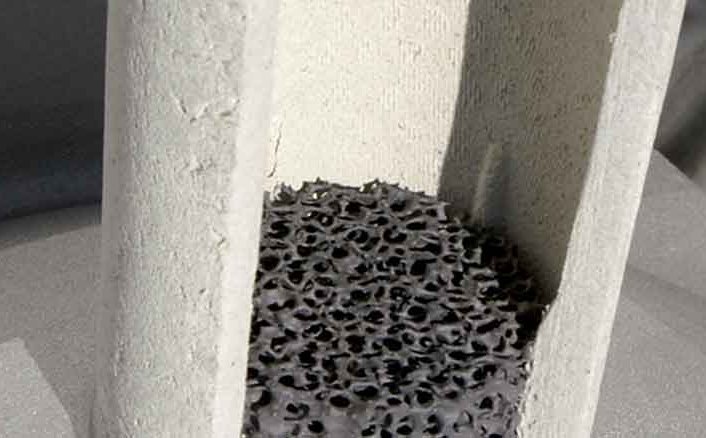
KALPUR direct pouring unit for non ferrous
The SIVEX FC (aluminium) or SEDEX (copper base) filter smoothes the metal stream, controlling the filling, and the insulating feeder material of the KALPUR helps to increase the feeding efficiency.