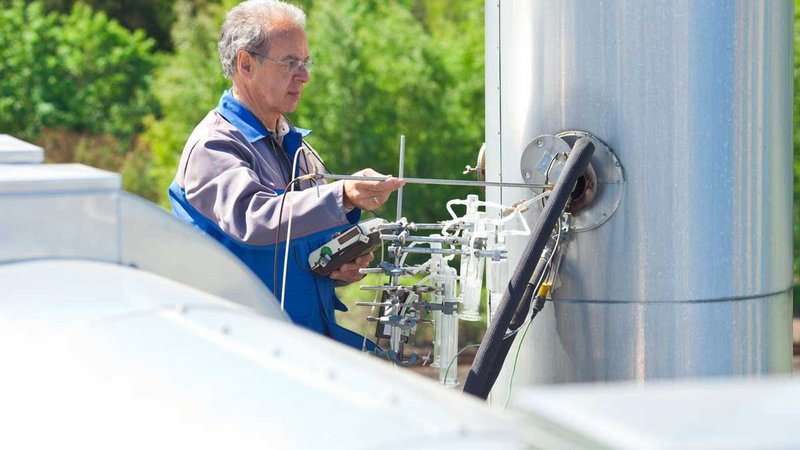
Bottom Pour Ladles
-
The ladle is fitted with a pouring nozzle in its base, closed by a refractory stopper rod. The metal is drawn from the bottom and is therefore slag-free, and non-metallics such as deoxidation products are able to float out of the melt. The metal stream flows vertically downwards from the ladle so that there is no movement of the stream during pouring. The disadvantage is that the velocity and rate of flow change during pouring as the ferrostatic head changes.
Unless a reusable system is fitted, the nozzle and stopper rod assembly must be changed after each use, thereby increasing the turn-round time, costs and the number of ladles required to handle a given output of metal.
The stopper rod may also distort or erode making it impossible to shut off the stream completely. It is not practical to handle less than 100 kg of steel due to the chilling effect of the stopper rod assembly. The flow from a bottom pour ladle depends on the size of the nozzle and the height of metal in the ladle so the flow rate and velocity of the metal stream reduces as the ladle empties. The nozzle/stopper rod is an excellent on-off valve but is not an effective flow control valve. Attempts to use it to control flow result in breakup of the metal stream with consequent risk of reoxidation of the steel.
However it is possible to calculate the discharge rate and metal velocity for each ladle and nozzle and its variation throughout the pour so that ladles can be suited to the mould sizes that are being cast.