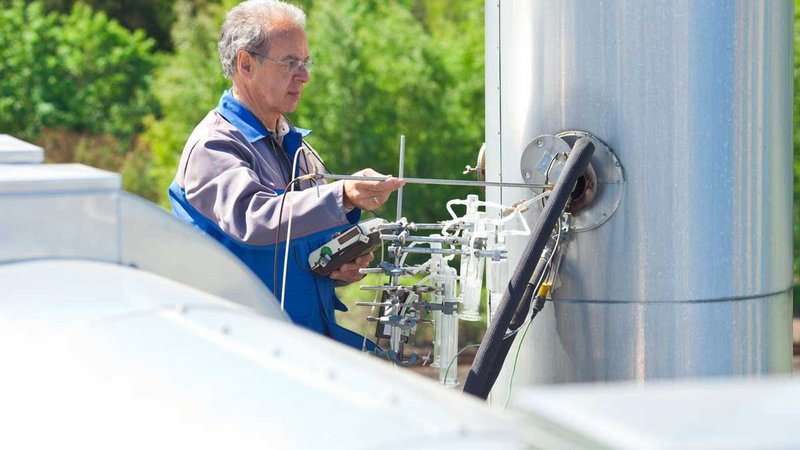
Dross
-
The dross consists of magnesium silicate films and magnesium sulphide particles.
Magnesium silicate is formed during the magnesium treatment by reaction between MgO and SiO2. Where high silicon nodularisers are used such as MgFeSi, more magnesium silicate is formed than when using pure magnesium nodularisers. The magnesium sulphide is usually present as clouds of fine individual particles. The silicate dross films, and MgS clouds are usually found together.
During Mg treatment, oxides and sulphides are formed in the iron, resulting in dross formation on the metal surface, this dross must be removed as completely as possible before casting. It is important to remember that the residual magnesium in the liquid iron after treatment oxidises continuously at the metal surface, causing loss of magnesium which may affect the structure of the graphite spheroids, moreover the dross formed may result in harmful inclusions in the castings.
Since treatment of iron with Mg always produces some MgO and MgS dross, care must also be taken to avoid dross entering the casting.
A magnesium silicate dross is formed which may give rise to defects at or just below the casting surface, usually on the upper surfaces of the castings. For this reason, it is common practice to filter ductile iron castings through ceramic filters.
The severity of dross defects is influenced by: Magnesium content – as residual magnesium increases, the dross increases. The initial sulphur content – high initial sulphur increases dross. The cerium content of the iron – cerium oxidises preferentially, reducing magnesium silicate formation. Mould conditions – high moisture content increases dross. Carbon and aluminium contents – both promote dross if increased.
Certain properties, particularly fatigue strength, are strongly influenced by non-metallic inclusions. The effects of large inclusions such as dross films are severe in both ferritic and pearlitic ductile iron, because notches are formed at which failure can begin. Dross defects at as-cast surfaces will reduce fatigue life substantially, reducing the fatigue limit by about 20–30% (Table 17.1). This is of great significance for castings such as crankshafts which fail by fatigue.
Coarse inclusions such as sand grains, large pieces of slag and dross films are trapped on the front face of the filter