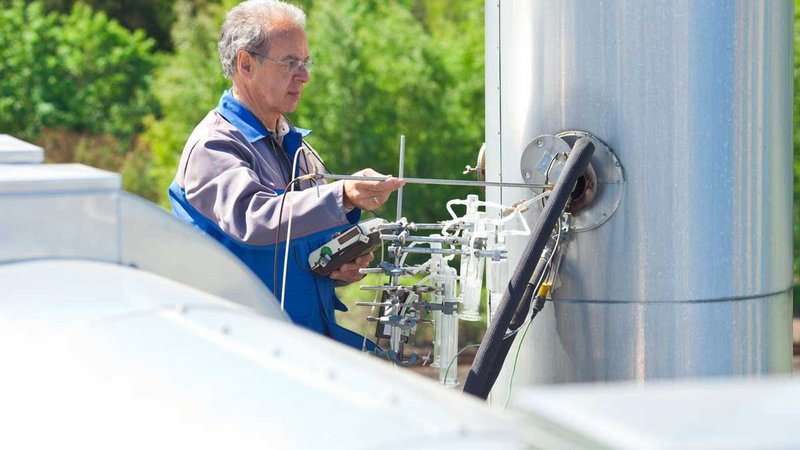
Linings Break Off
-
The refractory linings of cold blast cupolas have a short life of less than 24 hours, so cupolas are operated in pairs, each used alternately while the other is re-lined.
The Cr–Fe oxides formed during melting attack silica lining materials, so alumina linings should be used.
Basic linings of dolomite or magnesite are the most used in steel foundries.
Linings are made from refractory ramming mixes.
The ladle lining in an iron foundry is normally expected to last for a full shift, in which time it may be used between 50 and 100 times. The lining material must therefore be of good quality and be applied carefully. If ladles are used daily on high production plants, the old lining should be removed completely from the ladle body, which should then be coated lightly with a ganister wash and the new lining material rammed into position round the former. The material must be properly vented, by hanging rods between the ladle shell and the lining. These are removed before drying to allow easy passage of steam from the lining. The greater the capacity of the ladle, the thicker should be the lining.
Linings can be damaged by incorrect drying. Properly designed ladle heaters are better than simple gas-torches. The initial drying must be slow, to avoid cracking, the gas flame can be increased in intensity as the lining heats up. When the ladle is completely dry, it is ready for pre-heating. The lining temperature should be raised to about 900–1000°C before filling with molten metal. Heat losses are greatest when the ladle is filled for the first time after pre-heating or if it is only used intermittently, since heat from the metal is used in heating the refractories to temperature. If ladles are used continuously, temperature losses stabilise to a predictable value as heat is lost by radiation from the metal surface and by conduction through the ladle
The use of the KALTEK ladle lining system avoids the above problems.