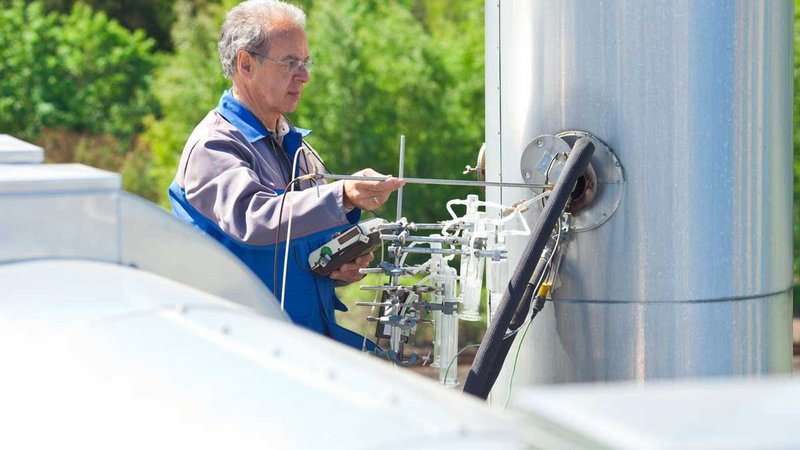
Self-hardening process
-
In the self-hardening process (also known as self-set, no-bake or cold-setting process) clean, dry sand is mixed with binder and catalyst, usually in a continuous mixer. The mixed sand is vibrated or hand-rammed around the pattern or into a core box; binder and catalyst react, hardening the sand. When the mould or core has reached handleable strength (the strip time), it is removed from the pattern or core box and continues to harden until the chemical reaction is complete.
As self-hardening mixtures; sand, binder and a hardening chemical are mixed together; the binder and hardener start to react immediately, but
sufficiently slowly to allow the sand to be formed into a mould or core which continues to harden further until strong enough to allow casting.
The method is usually used for large moulds for jobbing work, although series production is also possible.Self-hardening resin binder systems are furanes (FUROTEC and ESHANOL binders), phenolic-isocyanates/phenolic-urethanes (POLISET binders), alkaline phenolic resin, ester hardened (FENOTEC binders) or phenolic acid-set systems (FEN-O-FEN binders).