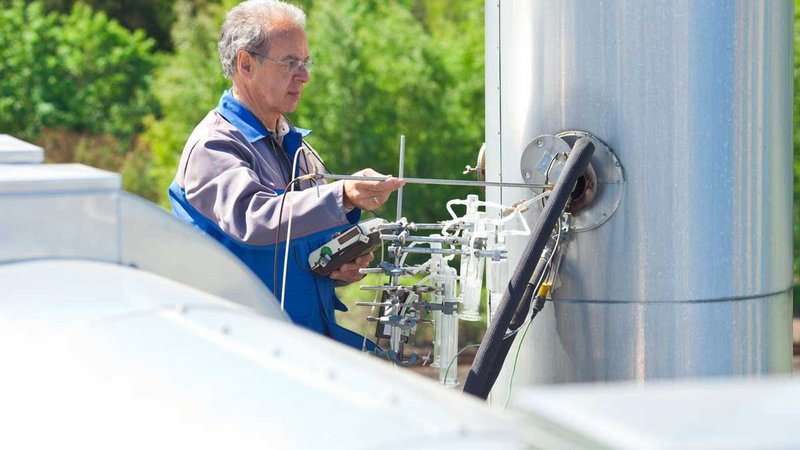
Shrinkage
-
During the cooling and solidification of most metals and alloys, there is a reduction in the metal volume known as shrinkage. Unless measures are taken which recognise this phenomenon, the solidified casting will exhibit gross shrinkage porosity which can make it unsuitable for the purpose for which it was designed. To some extent, grey and ductile cast irons are exceptions, because the graphite formed on solidification expands and can compensate for the metal shrinkage. However, even with these alloys, measures may need to be taken to avoid shrinkage porosity.
To avoid shrinkage porosity, it is necessary to ensure that there is a sufficient supply of additional molten metal, available as the casting is solidifying, to fill the cavities that would otherwise form. This is known as ‘feeding the casting’ and the reservoir that supplies the feed metal is known as a ‘feeder’, ‘feeder head’ or a ‘riser’. The feeder must be designed so that the feed metal is liquid at the time that it is needed, which means that the feeder must freeze later than the casting itself. The feeder must also contain sufficient volume of metal, liquid at the time it is required, to satisfy the shrinkage demands of the casting. Finally, since liquid metal from the feeder cannot reach for an indefinite distance into the casting, it follows that one feeder may only be capable of feeding part of the whole casting. The feeding distance must therefore be calculated to determine the number of feeders required to feed any given casting. The application of the theory of heat transfer and solidification allows the calculation of minimum feeder dimensions for castings which ensures sound castings and maximum metal utilisation.