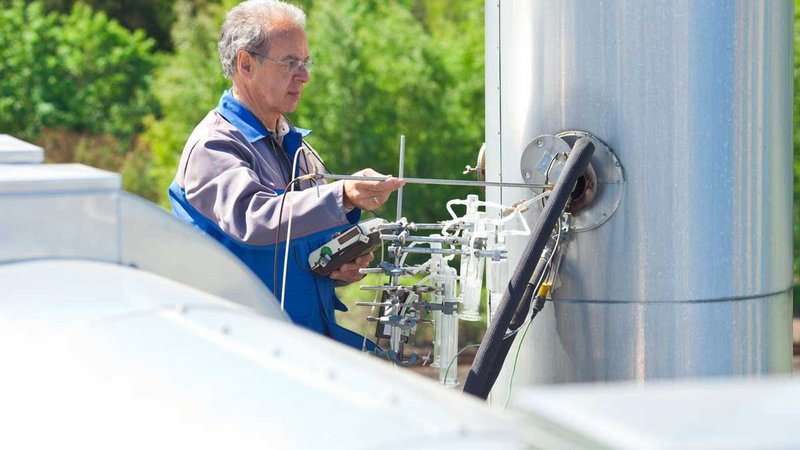
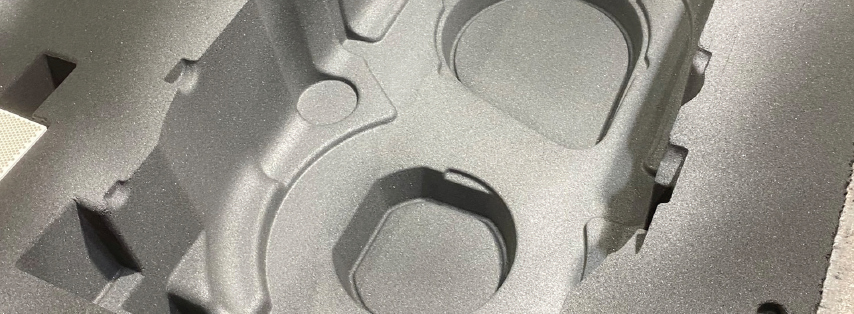
Preventing Sand Inclusions and Metal Penetration in Casting: Strategies and Foundry Coatings
03 Jun 2024
Casting processes are vital in many industries, from automotive to aerospace, where precision and quality are paramount. However, achieving flawless castings, free of defects such as sand inclusions and metal penetration, is a significant challenge. In this comprehensive exploration, we'll look at common casting defects, effective prevention strategies and the role of advanced coatings such as HARDCOTE SF800 in taking casting quality to new heights.
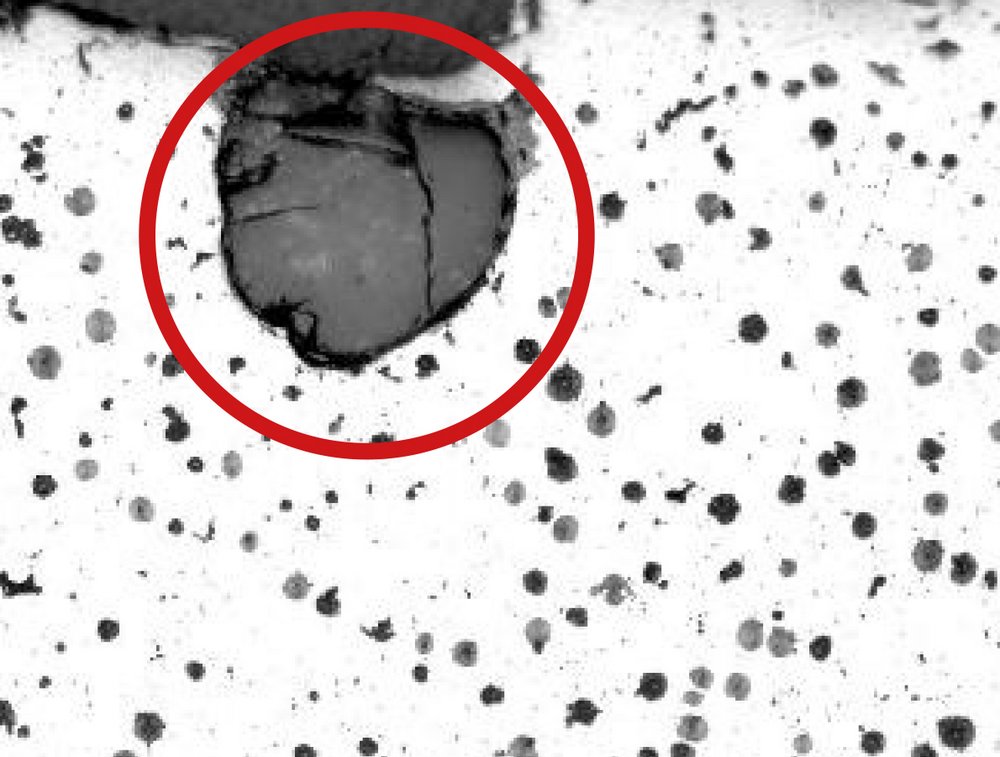
Understanding defects
Sand inclusions and metal penetration are two of the most common defects found in castings. Sand inclusions occur when sand particles from the mould become embedded in the casting material during the pouring process. Metal penetration, on the other hand, is the intrusion of molten metal into the mould surface, resulting in defects such as rough surfaces and dimensional inaccuracies. Factors such as mould erosion, inadequate compaction and thermal stresses contribute to the formation of these defects, jeopardising casting quality and structural integrity.
Common causes of sand inclusions and metal penetration
Sand inclusions can sometimes be accompanied by gas bubbles and slag inclusions. They can also become trapped beneath the surface of the casting and remain hidden until machined. Loose sections of sand that are washed out of the mould can lead to metal protuberances on the casting. Other possible causes include poorly formed gates, low sand compaction and insufficient binder in resin-bonded moulds and cores.
But how to prevent these defects?
Several strategies can help prevent sand inclusions and metal penetration in castings:
- Proper mould design: Designing moulds with optimised gating and riser systems can minimise turbulence and prevent sand erosion during pouring.
- Mould compaction and quality control: Ensure adequate compaction of moulding sand and implement strict quality control measures to inspect moulds for defects prior to pouring.
- Use of binders and additives: Use correct additions of binders and additives to improve the strength and cohesion of moulding sand to reduce the risk of sand segregation during casting.
- Temperature control: Maintain proper sand temperatures to prevent rapid curing of binders leading to poor compaction and low mould strength.
- Operator Training: Train operators in proper moulding techniques and pouring procedures to minimise the risk of sand inclusions.
- Refractory coatings: Apply a suitable refractory coating to prevent interaction between the molten metal and the sand mould surface.
By implementing these strategies, foundries can improve casting quality, minimise rework and optimise productivity.
The role of foundry coatings
Foundry coatings play a critical role in preventing sand inclusions and metal penetration by providing a protective barrier between the molten metal and the mould surface. These coatings, which consist of refractory materials suspended in a carrier fluid, promote mould stability, improve surface smoothness, provide thermal insulation, reduce metal penetration and improve release properties. Application of the correct foundry coating at a specified layer thickness is essential in effectively preventing sand inclusions, metal penetration and other casting defects. In response to the evolving needs of the industry, innovative solutions have emerged as game-changers in the quest for flawless castings.
HARDCOTE SF800: A game changing coating
An exemplary innovation in casting technology, HARDCOTE SF800 coating represents a significant leap forward in the quest for casting excellence. Designed to improve the surface finish of castings produced in green sand moulds, HARDCOTE SF800 offers a wide range of benefits. Its unique, surface hardening formulation prevents sand erosion and reduces the risk of sand inclusions; metal penetration is prevented by the filling of the pores at the green sand mould surface. By forming a carbon-based film, HARDCOTE SF800 prevents sand adhesion to the casting surface, improving mould strip and reducing the need for cleaning, reworking and blasting. In addition, its easy application and rapid absorption into the mould surface ensures seamless integration into the production environment, improving productivity without compromising casting quality.
The bottom line
In the competitive landscape of modern manufacturing, achieving superior casting quality is paramount. By understanding common defects and implementing effective prevention strategies, foundries can minimise rework and optimise productivity. Innovations such as HARDCOTE SF800 coating demonstrate the industry's commitment to continuous improvement and customer satisfaction. By adopting advanced coatings and technologies, foundries can improve casting quality, meet stringent specifications and thrive in today's dynamic market environment.