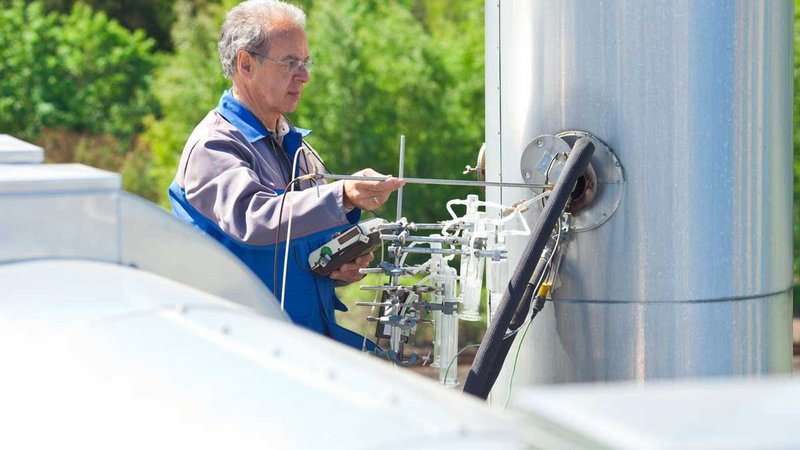
Aluminium casting alloys
-
Aluminium casting is dominated by the automotive industry. Roughly two thirds of all aluminium castings are automotive where the use of aluminum castings continues to grow at the expense of iron castings. Although aluminium castings are significantly more expensive than ferrous castings, there is a continuing market requirement to reduce vehicle weight and to increase fuel efficiency. It is this requirement which drives the replacement of ferrous parts by aluminium. Aluminium castings are widely used in cars for engine blocks, heads, pistons, rocker covers, inlet manifolds, differential casings, steering boxes, brackets, wheels etc. The potential for further use of aluminium in automotive applications is considerable. European cars in 1992 had 50-60 kg Al castings and this is expected to double by year 2000. The growth in electric vehicle production is fuelling demand for aluminium casting production today. New aluminium components, such as battery housings, are required in ever increasing volumes. Car manufacturers are also expanding their use of lighter cast aluminium parts for structural components in order to compensate for the added weight of the battery.
When aluminium alloys are cast, there are many potential sources of defects which can harm the quality of the cast part. All aluminium alloys are
subject to:- Shrinkage defects
- Gas porosity
- Oxide inclusions
Aluminium alloys can be cast by several processes:
- Sand casting
- Chill casting, i.e. gravity die (permanent mould casting) or low pressure die casting, in a metal die using sand cores
- High pressure die casting
- Lost foam
- Investment casting may also be used for aerospace castings
Casting alloys are designed to be cast by one or other of these techniques, although some alloys are suitable for more than one casting method.