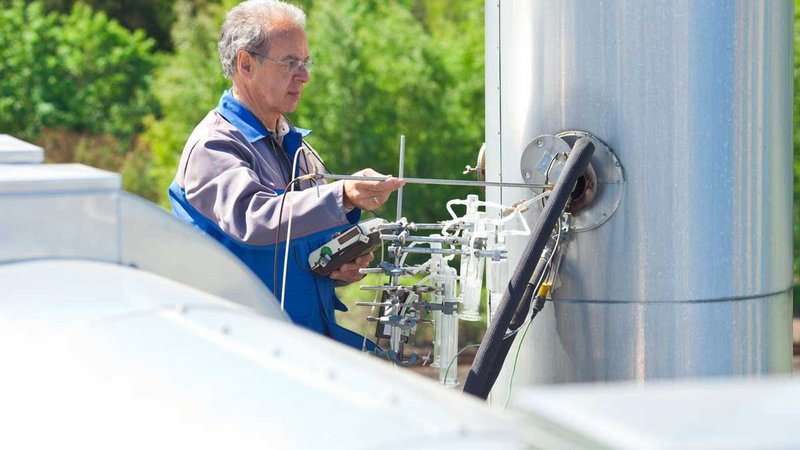
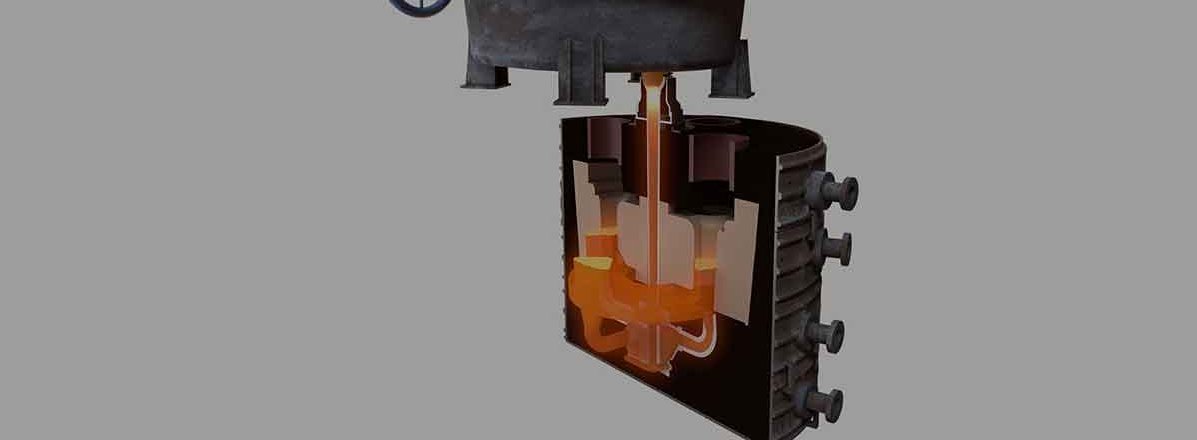
HOLLOTEX Shroud
Turbulence control and filtration for large steel castings
- No air entrainment
- Reduced unacceptable X-ray and MPI defects
- Reduced repair requirements
- Pouring temperature reduction
- Improvement in mechanical properties
Metal stream shrouding and filtration of steel castings
HOLLOTEX Shroud is a new process that can be effectively applied in steel foundries. A shroud is positioned in the mould, the bottom of the shroud protrudes into a filter box located at the base of the mould. When the ladle is in position, the shroud is mechanically lifted so there is a seal between the nozzle and the shroud. The metal flows from the nozzle, through the shroud into the filter box, and then to the runner. As the metal flows it is protected from exposure to air, eliminating the potential for air aspiration.
Downloads
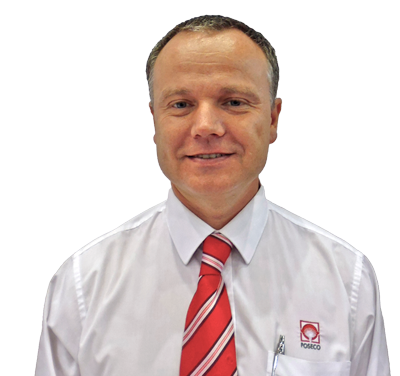
Casting clean: today’s solutions and opportunities
Learn more about improving casting quality in steel casting applications in our white paper Casting clean: today’s solutions and opportunities. This paper cuts through the noise and brings clarity to the clean steel debate: an overview of common casting defects is followed by a detailed review of the technologies currently on offer to reduce casting defects and improve cast quality at each stage of the steel casting process.