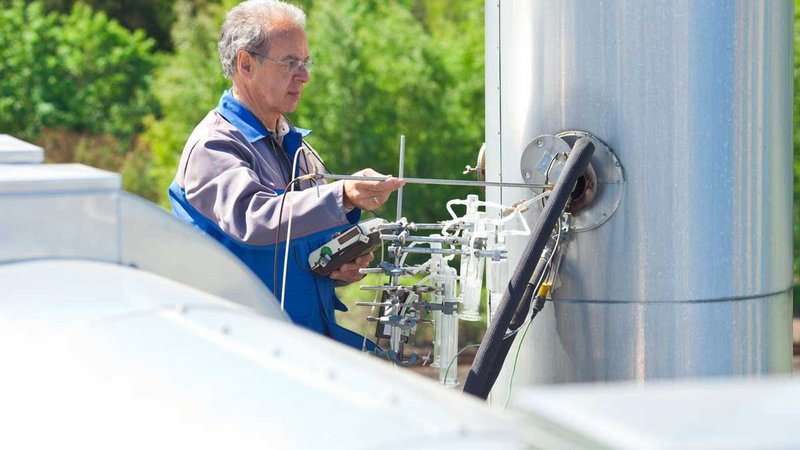
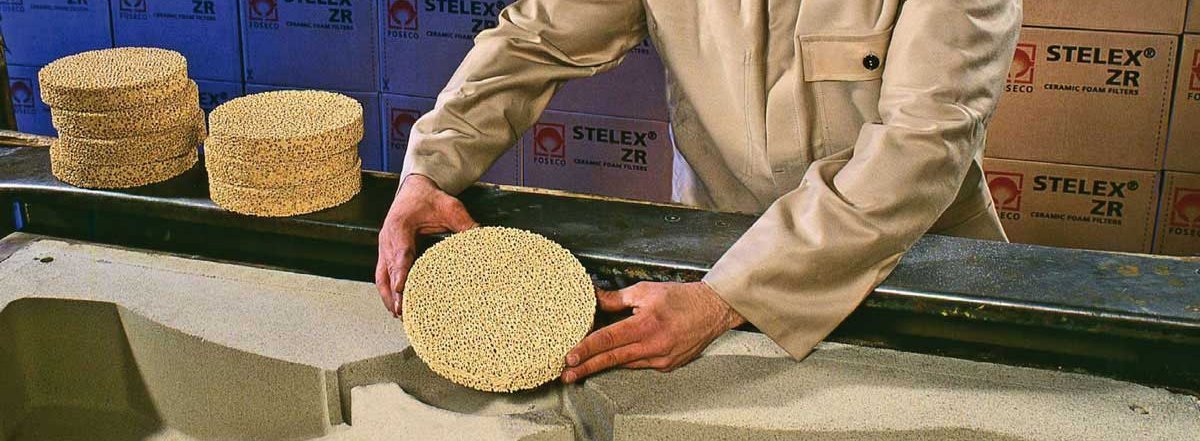
Casting clean steel: filtration
10 May 2024
Key takeaways
- Significantly reduce inclusions
- Reduce turbulence of the pour
- Protect against late reoxidation of the melt stream
Free white paper
For more on the different types of common steel casting defects, check out our white paper
Clean steel castings: a decades-long story
The clean steel concept has been discussed and worked upon in the steel casting world for many decades. And with good reason – defective casting has a tangible impact on a foundry’s bottom line. In this series of blogs, we are taking a look at some of the technologies that assist foundries in improving as-cast quality. Here, we consider the benefits of filtration.
Discover more about the challenge posed by common casting defects in the first two blogs in this series.
Filtration in steel casting
Casting filtration is not a complex idea: in essence, the melt is poured through a filtration media (traditionally ceramic foams), which allows the molten metal to pass through, but catches any unwanted elements that would result in inclusion defects in the as-cast piece. Filters also reduce the energy of the metal stream, and therefore help control the flow of metal into the mould (for more on flow control, check out our blog on the topic).
Illustrating the benefits that filters can provide, at one foundry, the use of zirconia-based filters from Foseco resulted in a:
- 50% - 70% reduction in upgrading time
- 50% - 70% reduction in welding material consumption
- Significant reduction in the value of the work in process
- Improvement in surface finish and casting machinability
So, why don’t more steel casters filter their melts?
Despite research showing the high effectiveness of filtration, market surveys estimate that less than 8% of global steel casting tonnages are filtered. It’s true that some casting applications are either unsuited to filtration or do not require it, such as when casting pieces that are currently too big to filter or have low casting quality specifications. The availability of low-cost labour for cleaning and repair also reduces the attractiveness of filtration.
However, this does not entirely explain the apparent reticence of steel casters to use filters: even among those foundries who do currently filter their castings, many only apply filters to a small proportion of their output. Such reluctance often stems from concerns that casting filtration will result in problems and inconsistencies in the casting process.
Reliable filtration solutions from Foseco
To overcome these concerns, Foseco has developed a range of steel casting filtration systems that provide consistent performance and enhanced filtration efficiency in a range of demanding casting applications.
STELEX ZR ULTRA filters, for example, were developed specifically to respond to concerns from steel casters over the process implications of filtration. Benefits include:
- Consistent capacity and flow rates
- Allowing the use of finer filters with molten steel
- Improved filtration efficiency and turbulence control
- Reduced chance that metal might bypass the filter
- Very low friability, reducing the potential incidence of filter-related defects in the casting
The Foseco range also includes STELEX PrO carbon-bonded filters for low-carbon steel and steel alloy applications, where reoxidation is a major challenge. Positioned at the ingate, rather than at the base of the downsprue, these filters ensure the removal on any inclusions formed in the running system.
Combining filtration and flow control
While all filters offer a degree of flow control, KALPUR units and HOLLOTEX CFU filtration devices from Foseco are designed specifically to combine the benefits of both processes.
A replacement for existing top or side feeder sleeve, the KALPUR unit receives the melt steam through a STELEX filter, which absorbs the impact (eliminating turbulence) and removes inclusions. When pouring is complete, the unit functions as a feeder system for improved directional solidification and reduced risk of shrinkage casting defects.
The HOLLOTEX CFU is used for the production of large ferrous castings. It comprises a refractory centrifuge system, which separates larger inclusions from the molten metal, followed by integral STELEX ZR filters, which remove any trace contaminants in the stream and smooth the flow of material into the mould.
Time to consider filtration?
With the benefits of filters now available to a wider range of steel casting applications, it may well be time to ask what they could do your foundry. Ultimately, however, selection of the appropriate solutions will depend on your specific foundry conditions and casting application. Expert advice will assist in formulating process-specific strategies for optimal results.
Interested in discovering more about common steel casting defects and the solutions available to prevent them.
Check out our white paper: Casting clean: today’s solutions and opportunities.