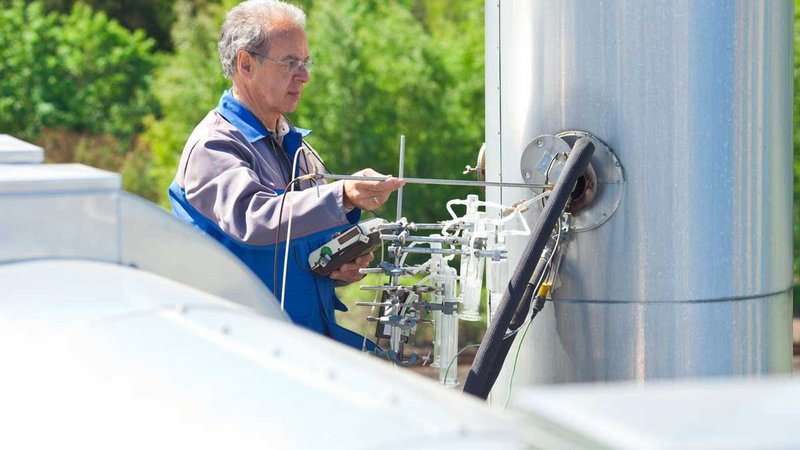
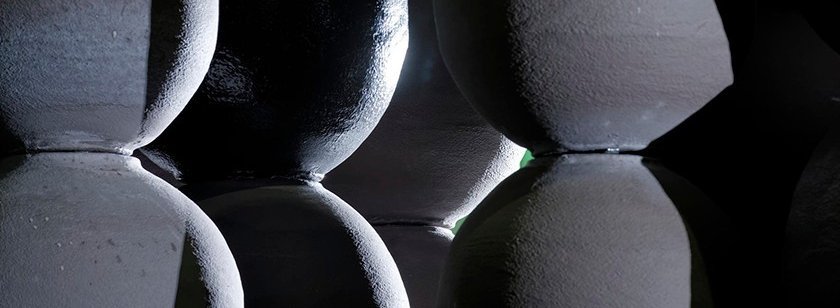
How crucible selection can lower energy bills and carbon emissions
18 Mar 2024
A crucible is just a crucible, right? We don’t agree.
We think it can be so much more.
When it comes to selecting what crucible to purchase for your metal-casting process, what do you look for? Traditionally, these items have been seen as commodity products with the purchasing decision coming down to how low the number is on the price tag. When performance metrics were taken into account, it’s often just a rudimentary check on the lifetime of the product.
But the winds of change are blowing. Energy-intensive industries are under pressure from multiple directions. Energy costs are rising in many regions. It is however the increasing scrutiny of environmental issues – and particularly carbon emissions – that poses perhaps the greatest future challenge. In the EU, for example, changes are coming to the Emissions Trading Scheme that will likely push up carbon prices, while reducing the number of free allowances available to heavy industries.
And with growing urgency to efforts to limit global temperature rises, the EU may have pre-empted global action at COP26, taken place in Glasgow, UK, in November.
With this background, now is a good time to change how you view your crucibles, making them an ally in the fight against rising energy and environmental costs. The key consideration here is not the purchase cost or lifetime; it’s thermal performance.
Thermal performance is so important for a number of reasons. The headline benefit comes down to the simple fact that the higher the energy efficiency of your crucible, the lower your energy consumption. Which is good for both your energy bills and your carbon footprint. At one aluminium foundry, for example, switching to ENERTEK energy-efficiency crucibles helped reduce energy consumption by 13.4% and carbon emissions by almost 8,000 kg per year.
But that’s only one of several advantages: energy-efficient crucibles, such as our ENERTEK range for aluminium and zinc foundry applications, can also improve productivity and product quality.
Sound interesting? Read our white paper to find out more about how your crucible selection can reduce energy bills and your environmental footprint. Or contact us to speak with one our experts.
Energy efficiency considerations for aluminium and zinc crucibles
Improving the energy efficiency of foundry operations reduces both energy costs and carbon emissions. It’s a vital win-win for foundries under pressure to reduce their environmental impact, while staying cost competitive.
Foundries should therefore consider switching to energy-efficiency crucibles, such as the ENERTEK crucible range from Foseco, even if this means challenging traditional price-based purchasing decision-making.
Reducing energy consumption in zinc oxide production
In this specific study where ENERTEK ZnO retorts were used, the company showed an annual reduction in natural gas usage of 132,000 m3 which resulted in an annual cost saving of over €52,000 and a CO2 emission reduction of 260 tons.