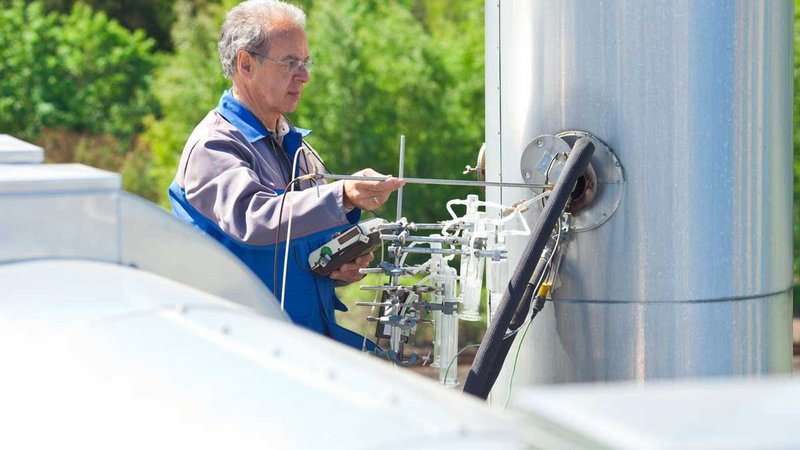
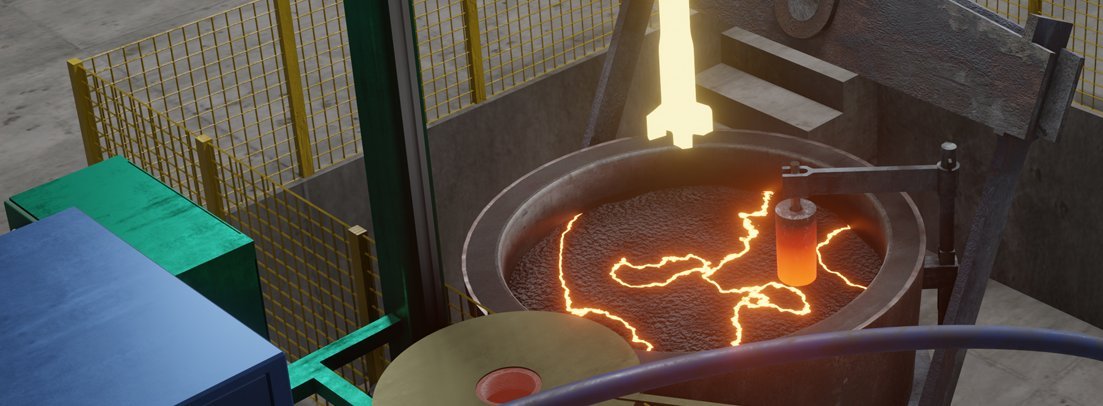
ROTLOCLENE process
Innovatiove process for the rotary treatment of molten metal in the pouring ladle
- Metal temperature homogenisation
- Removal of inclusions and bifilms
- Synthetic slag desulphurisation
- Modification of alumina inclusions by pure Ca
- Casting temperature reduction
- Shrinkage and porosity reduction
- Casting surface improvement
- Improved mechanical properties
- Faster delivery of castings due to less reworking
The ROTOCLENE process has been developed to treat molten metal effectively in the ladle
The process brings together Foseco products from across the foundry and steel making industries. The equipment used is a rotary machine, which is a modified version of the proven equipment that Foseco has supplied for many years for use in non-ferrous applications. The rotor is made from Vesuvius' VISO material and we can supply ladle linings to allow treatment with our desulphurising fluxes and cored wire.
Downloads
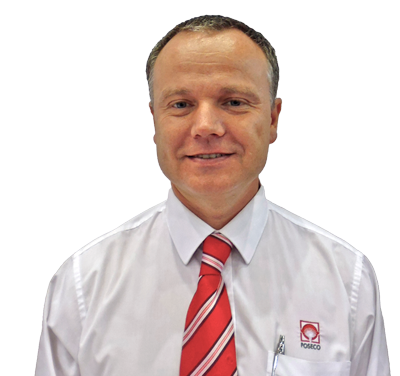
Casting clean: today’s solutions and opportunities
Learn more about improving casting quality in steel casting applications in our white paper Casting clean: today’s solutions and opportunities. This paper cuts through the noise and brings clarity to the clean steel debate: an overview of common casting defects is followed by a detailed review of the technologies currently on offer to reduce casting defects and improve cast quality at each stage of the steel casting process.