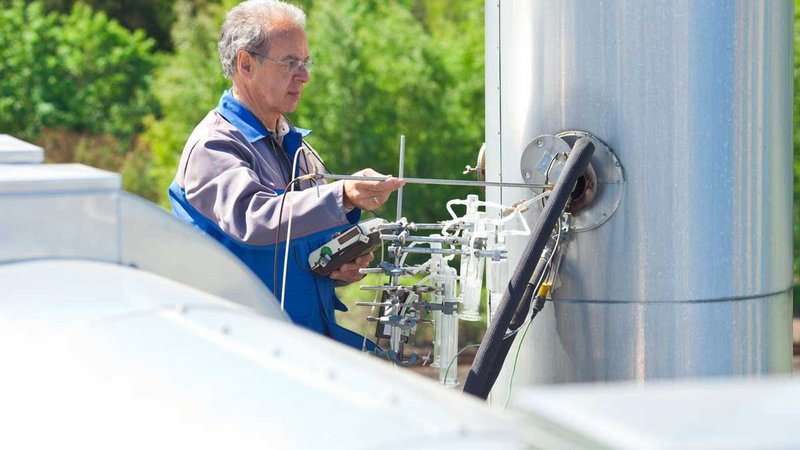
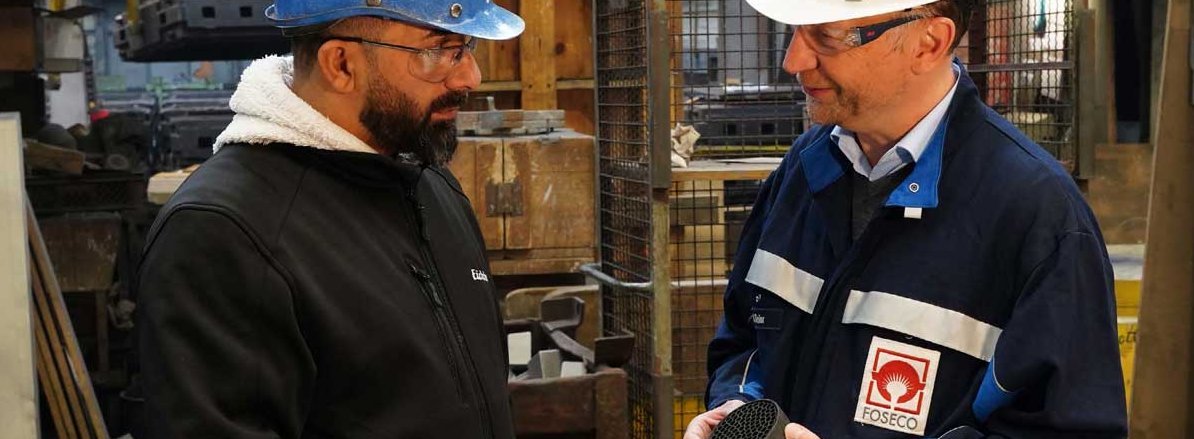
Foundry Practice 275
22 Jun 2023
This edition focuses on our Methoding Products, Feeding Systems and Filtration solutions for Ferrous castings and describes new products and application technologies to improve casting quality, reduce environmental impact and increase productivity.
The first article describes an exciting new patented technology for the filtration of Iron and Steel castings - STELEX Optiflow3D. The filters are produced using Additive Manufacturing, which allows significant freedom in terms of geometry and pore design of the structure. For the first time it is possible to design filters which can be optimised for individual castings, in terms of filtration efficiency, metal capacity and flow rate.
HOLLOTEX EG Runner ST is a new lightweight alternative to conventional holloware for jobbing steel casting applications. The runner tubes can be cut safely, quickly, and easily positioned, with minimum dust, waste, and contamination of the sand system.
Interest in expanding spot-feeding applications to vertically parted greensand lines such as DISAMATIC continues to increase. Here we present two case studies highlighting the yield and productivity advantages of using FEEDEX K sleeves directly on the swing plate.
Increasing environmental pressure on foundries, particularly in terms of waste sand disposal has driven the development of exothermic feeder sleeves which eliminate or reduce the amount of fluoride entering the sand system. Christof Volks presents a summary of the products and technologies available today.
Finally, we present the latest version the Foseco Pro Module for MAGMASOFT®, describing the improvements in the user interface and additions to the functionality.
We hope you enjoy the issue!
The incorporation of additive manufacturing technology (3D) in casting filtration, providing optimised efficiency and customization
Ceramic foam filters have become the leading choice for metal filtration in casting since the 1980s. They are extensively used across various alloys and casting technologies, providing cleaner castings with improved properties. Over the years, our understanding of filter application has advanced significantly, and guidelines have been developed to ensure their durability. Despite their limitations in pore size and design flexibility, ceramic foam filters outperform other filter types in terms of filtration efficiency and turbulence control. The emergence of additive manufacturing, particularly 3D printing, offers new opportunities for customised filter designs with precise pore sizes and structures, further optimising casting filtration.
HOLLOTEX EG runner ST - The lightweight alternative to ceramic gating systems, now also available for steel casting
HOLLOTEX EG Runner, introduced in 2009, revolutionised the construction of gating systems for hand-moulded iron castings. It eliminated the need for ceramic components and gained popularity in the European and American iron casting markets. However, it had limitations in withstanding high pouring temperatures used in steel casting. To address this, HOLLOTEX EG Runner ST was developed with an optimized formulation and a refractory coating.
Additionally, the shape of the components was modified to improve the flow distribution of molten metal.
Application of FEEDEX K on DISAMATIC moulding lines
DISA‘s introduction of vertically parted moulding machines to the foundry market in 1962 revolutionised the industry with their high productivity and low process costs. Over time, efforts were made to increase the yield of DISA castings, including the use of feeder sleeves and direct pour systems. While feeder sleeves placed on the joint line of the mould improved casting yield and productivity, challenges arose with their application. The degree of utilization on vertically parted moulding lines was lower than on horizontal lines, but market pressures have led to heavier and more complex ductile iron parts being produced on vertical lines. Spot feeding techniques have emerged as a solution, and modifications have been made to spot feeders to address these challenges. In this paper, we will explore the impact of these advancements on the foundry industry.
Fluoride emission free feeding systems solutions
Fluoride compounds have been used in foundries since the 1950s to initiate exothermic reactions in aluminum. Recently, there has been increased focus on fluorides, particularly their presence in feeder sleeves. Concerns include their impact on casting integrity and environmental legislation regarding fluoride disposal. To address these issues, a range of fluoride-emission-free formulations have been developed, providing the same performance as their conventional counterparts. In order to achieve these results extensive research and trials have been carried out.
The Foseco Pro Module for MAGMASOFT® - Update 2023
This year, Foseco and MAGMA celebrate the 20th anniversary of their strategic alliance, with the release of a new version of the Foseco Pro Module.
It features an updated interface with new sleeve types, filter prints & additional complex geometries to accelerate the design of gating and risering systems in MAGMASOFT® 6.0.