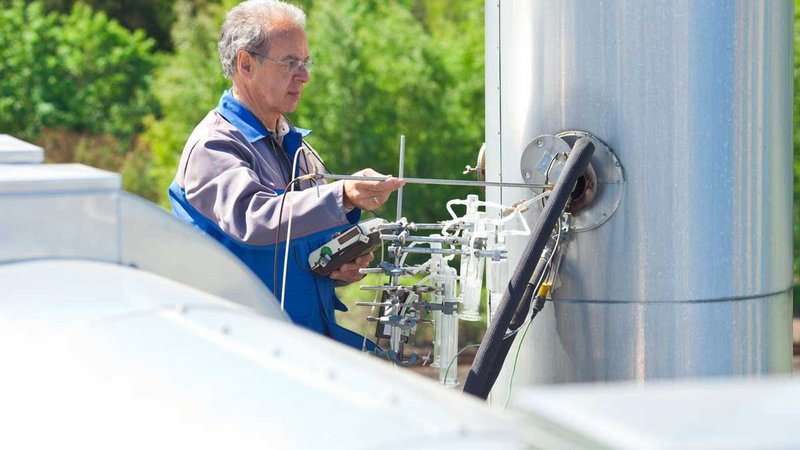
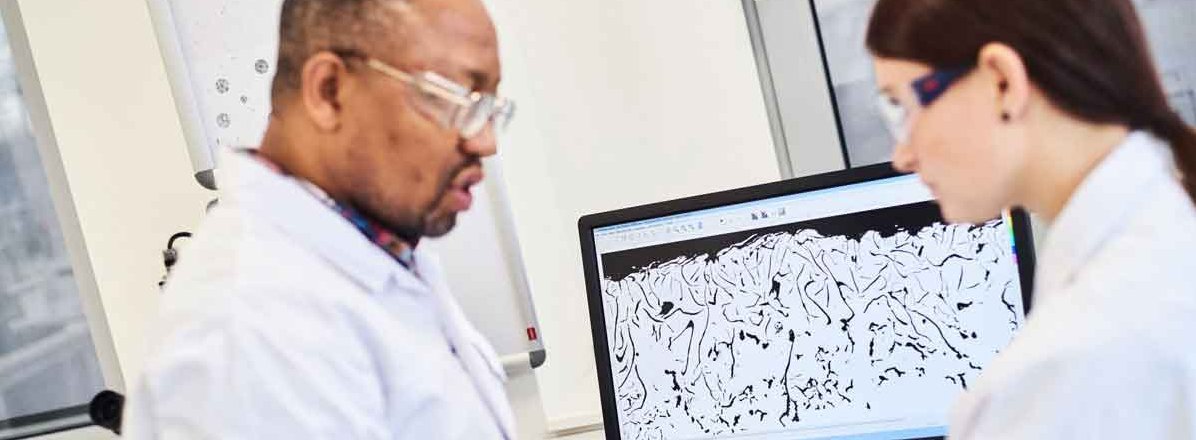
What are non-metallic inclusions and how do you avoid them?
02 Apr 2024
Non-metallic inclusions are the most common cause of casting defects. They are not, however, a homogenous group. This blog looks at some of the most common types and causes of inclusions when casting ductile cast iron, steel and aluminium alloys. We also consider some of the methods available to prevent them.
For a more detailed discussion of non-metallic inclusions, check out the recent article 'Non-metallic inclusions in ductile cast iron, steel and aluminium castings' by Dr Wolfram Stets, Foseco International Technology Manager Metal Treatment.
A general introduction to non-metallic inclusions
There are many types of non-metallic inclusions with a wide range of interrelating causes. They are generally divided into two main categories:
- Exogenous inclusions are caused by materials entering the melt. This could be the result of wear of the refractory linings or the use of substandard moulds.
- Endogenous inclusions are products of reactions between the melt and dissolved gases (e.g., oxygen, sulphur, or nitrogen).
These groups are not entirely distinct however. Borderline cases includes the products of reaction between the molten metal or alloy and atmospheric oxygen. This would be a particular issue when casting alloys that are more susceptible to oxidation or when significant turbulence is generated during handling of the melt.
It’s also important to note that non-metallic inclusions can be introduced throughout the casting process, which can make identifying the source of an inclusion defect a complicated matter. Fortunately there are now a range of solutions available to the foundry that help ensure both the cleanliness of a melt when it leaves the furnace, and that it remains so along the complete casting flowsheet – right to the point of solidification.
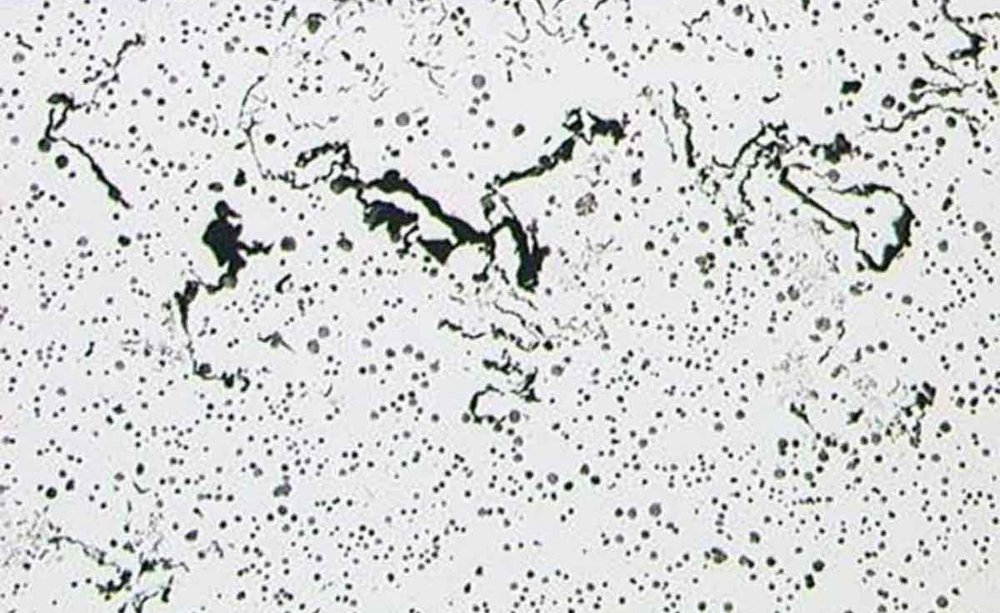
Some common non-metallic inclusions
Sand inclusions are exogenous inclusions. Formed when particles of the moulding sand dislodges into the melt, they can account for between 30% and 40% of rejected castings in application that utilize sand moulds (e.g., in ductile cast iron and cast steel) and. Moulding sand can also act as a carrier of other contaminants that may form inclusions. Sand inclusions are also problematic because they occur at the final stage of casting: as the melt is poured and solidifies in the mould. This makes it essential to adopt good mould making practices.
Slag inclusions are caused by contact between the melt surface and ambient air. They are particularly common in ductile cast iron, since slag formation is an inevitable result of nodularisation. It is therefore important to follow best practices to control slag formation and separate it from the melt, to ensure slag and dross defects are not present in the final casting. This might include the use of slag coagulants or melt filtration.
Slag inclusions also occur in cast steel, where they are caused by the reaction of elements in the melt with high affinity to oxygen with the oxygen in the ambient air. Inclusions may also be formed by reaction products of refractory lining and metallurgical slag.
Endogenous non-metallic inclusions mainly comprise compounds of oxygen (in cast steel and aluminium), sulphur and nitrogen (in cast steel). It is not possible to avoid the chemical reactions that produce these compounds; the focus is therefore on measures to minimise the quantity of these compounds that end up in the final casting as inclusions. This includes controlling the formation of these compounds (e.g., clean input materials, melt treatment, pouring shrouds), while ensuring the removal of any that have formed in the melt before pouring (e.g., filtration, slag coagulation).
Casting clean: today’s solutions and opportunities
Learn more about improving casting quality in steel casting applications in our white paper Casting clean: today’s solutions and opportunities. This paper cuts through the noise and brings clarity to the clean steel debate: an overview of common casting defects is followed by a detailed review of the technologies currently on offer to reduce casting defects and improve cast quality at each stage of the steel casting process.
Why control non-metallic inclusions?
Adopting best practices to minimise non-metallic inclusions brings a range of benefits. These include:
- Improved casting quality
- Improved casting yield
- Reduced clean-up costs
- Shorter lead times
There is also an environmental benefit that results from improved energy and materials efficiency. These benefits combine to offer the foundry a competitive edge over competitors who do not so effectively control non-metallic inclusions.
As this brief treatment of the topic has shown, however, the battle against non-metallic inclusions is multifaceted and requires a keen insight not only into the complete foundry process but the unique conditions of the casting application in question. For tailored advice on improving your foundry process, contact our expert team.
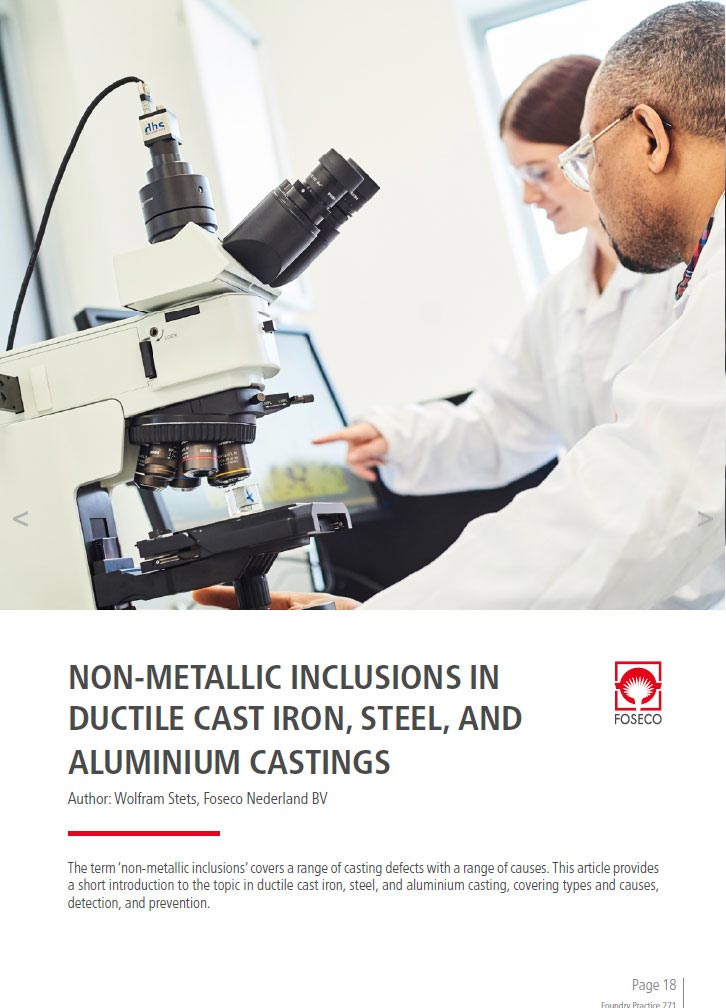
Non-metallic inclusions in ductile cast iron, steel, and aluminium castings
Discover more about non-metallic inclusions in ductile cast iron, cast steel and aluminium alloys in the article Non-metallic inclusions in ductile cast iron, steel and aluminium castings from Dr Wolfram Stets, Foseco International Technology Manager Metal Treatment. In the article, Dr Stets details the types and causes, detection and – most importantly – how to prevent non-metallic inclusions by application.