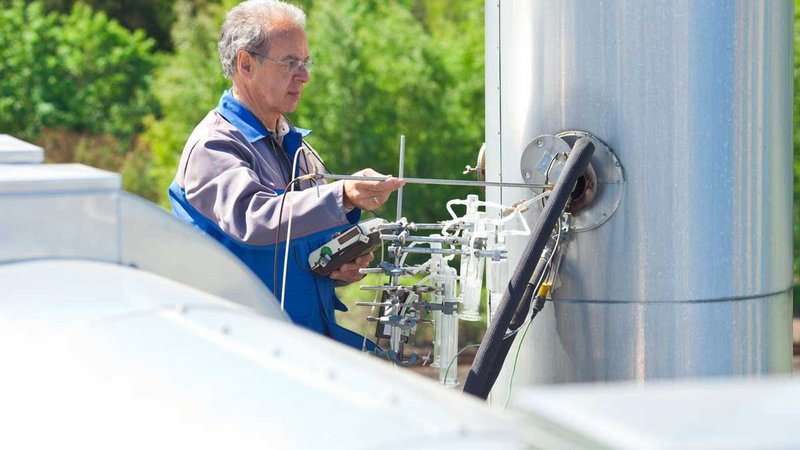
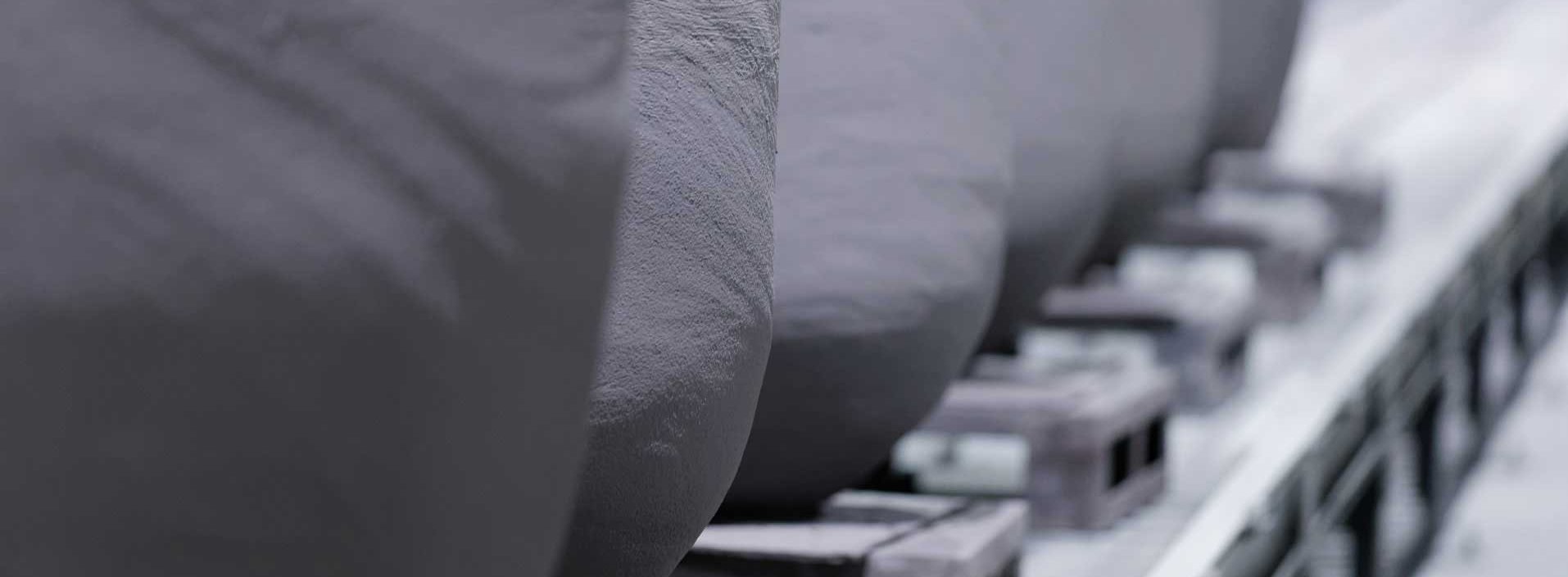
Foundry Practice 272
01 Jun 2023
This special GIFA edition of Foundry Practice is focused on a range of new technologies aimed at our aluminium and other non ferrous foundry customers. These are exciting times for aluminium castings, which, despite the upheaval in the automotive sector caused by electrification, are predicted to continue to grow for the foreseeable future.
Our first article is a study on the application of granulated cleaning and drossing fluxes in aluminium high pressure diecasting. The benefits of using granulates by means of the MTS process, can achieve better melt quality and make the process more economical and sustainable without impacting casting quality, weldability and corrosion resistance.
Our second paper, which is being presented at the GIFA forum demonstrates the value that can be derived from applying high strength exothermic feeders to aluminium and copper based castings. Significant savings in fettling can be achieved by optimising casting yield and minimising feeder contact areas, and the elimination of the need for hot topping compounds reduces emissions and improves the working environment.
The third story looks at the latest developments in crucibles. Energy consumed in the melting and holding of non ferrous alloys is a major contributor to a foundry’s CO2 footprint, and with the recent surge in energy prices, foundries are looking for ways to both help the planet and save costs. The ENERTEK range of crucibles is ideally suited to optimising energy consumption. For customers where crucible life is the main driver, we present the newly developed DURATEK Supermelt range which demonstrated a 70% increase in life at Mahle in Poland.
The final paper, which will also be presented at the GIFA Forum is focused on WASCO water soluble core binders for high pressure diecasting. The cores produced by this process are strong enough to withstand high casting pressures, yet dissolve easily in water and can easily be removed after casting. This revolutionary technology will enable both liquid metal and semi-solid high pressure die casting foundries to manufacture long series of more complex parts that were previously too difficult or too expensive to produce.
We hope you enjoy the issue!
Cleaning and drossing granulate for structural high-pressure die cast aluminum components
This paper proves in detail and with the participation of industry (Magna Cosma) and science that under today‘s technological conditions the use of granulates in die casting is not only harmless but also economically and ecologically important.
The benefits of FEEDEX NF1 exothermic sleeves in aluminium and copper casting
Since the development of FEEDEX NF1 exothermic sleeves for non-ferrous casting applications, they have demonstrated significant value in the aluminium sector. Benefits include significantly extended solidification time, increased casting yield, lower fettling and remelting, and lower emissions. The result is lower production costs and a reduced carbon footprint. These advantages have also now been demonstrated in copper casting applications, where the higher melt temperature and melt density further extends the value delivered.
Enhancing crucible performance in non-ferrous applications
Crucibles have an important role to play in improving the energy efficiency and environmental performance of non-ferrous casting operations. Recent technological advances have seen crucibles developed that increase thermal performance and improve the consistency and length of their operating life. Installation and operating practices are also critical to achieving consistent crucible performance however, and therefore careful attention to recommended procedures should be followed to ensure foundries get the most from their crucibles.
Enhancing crucible performance in non-ferrous applications
For HPDC applications, Foseco developed a new type of sand core using innovative WASCO water-soluble binder systems and optionally with adaptable coatings to avoid liquid metal penetration into the pores of the sand core. This paper focuses first on some fundamental aspects on the development of such a watersoluble binder system, followed by 2 practical examples, one producing cores for explosionproof instrument housings, and the other manufacturing sand cores for automotive applications. Irrespective of the high flexural strength of the sand cores, after the casting process the complete casting was immersed in cold water after which the binder showed excellent water-solubility. Due to the short cycle times resulting in a relatively low thermal impact, no issues occurred with the generation of volatile organic compounds (VOC’s) as the organic binder thermally decomposes.