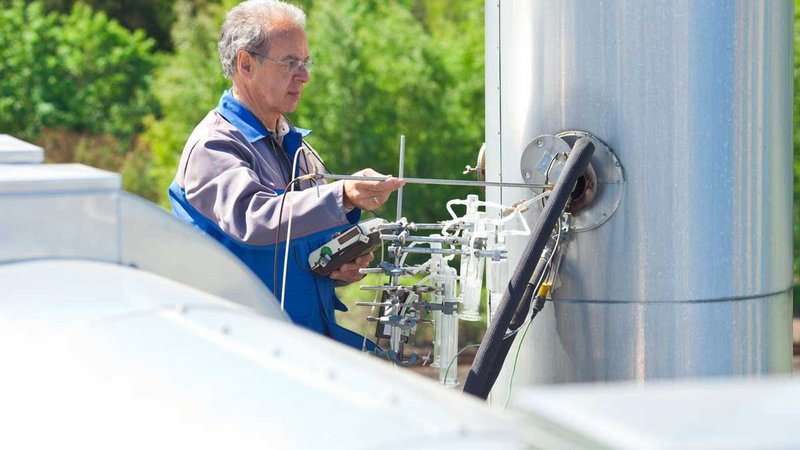
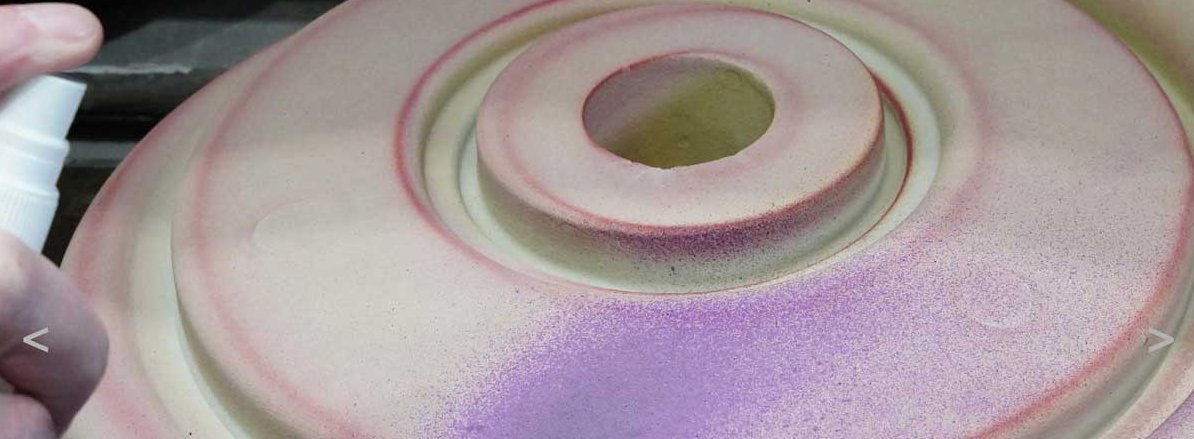
Foundry Practice 274
17 Jun 2023
Welcome to this special GIFA edition of Foundry Practice focussing on our products for the mould and core shop. It is not only about the products though, at Foseco we pride ourselves on delivering solutions to our customers that solve problems, and the product is only a small part of that solution. This approach is demonstrated effectively in the first technical article which brings together a number of underlying coating technologies to
reduce the environmental impact of the foundry process in terms of energy consumption and a reduction of formaldehyde emissions; but ultimately enabling increased productivity and generating significant savings for the foundry. This theme of sustainability is then continued through further technical papers that focus on reducing naturally occurring radiation emissions by reducing zircon consumption and reducing volatile organic compound (VOC) emissions and reducing fire risks through the implementation of more environmentally friendly release agents. In both cases these sustainable solutions do not in any way compromise the product performance or the final quality of the castings produced.
Sustainability cannot only be considered in the isolation of individual customers, but must be taken holistically in a cradle to grave approach, and it is with that in mind that I am very keen to recommend another article. The article relates to an end-use market for castings and shows how by using the best performing coatings, residual particulates in engine blocks can be minimised and those remaining particulates are less damaging to bearings, meaning that lead can be eliminated from bearing material without detriment to performance.
When considering the performance of products it is essential to ensure the correct application and control; for coatings this starts with the correct dilution and homogenisation of the product to ensure the required layer thickness is applied repeatably without runs and drips. Foseco’s dedicated team of application experts are available to offer advice and support to ensure the optimum performance of our products and this expertise is complemented by autonomous solutions such as the Intelligent Coating Unit (ICU) described in an article on pages 15-19, that will automatically control the density of the coating to ensure it is always at the correct application dilution.
We hope you enjoy the issue!
How coatings can improve economic, social, and environmental sustainability at foundries
The benefits of water-based coatings have been known for quite some time. As a result, their use has become common in the global foundry industry. However, they remain rare in some sectors of the industry, such as at jobbing foundries, where solvent-based coatings are still prevalent. The SEMCO family of coatings offers the following range of features, which overcome the challenges traditionally associated with water-based coatings (longer and more costly drying processes; reduced mould shop productivity), while improving the overall health and safety of foundries.
Zircon-free refractory coating for iron and steel castings
Zircon-based refractory coatings are widely used in foundries around the world. However, the use of zircon is problematic due to it being a naturally occurring radioactive material (NORM). Prices for zircon have also risen steeply in recent years, and remain volatile. Foundries are therefore looking for refractory coatings that reduce or eliminate the use of zircon. In response to this market demand, Foseco has developed the TENO Tec ZA zircon-free family of coatings, which have now been successfully applied at multiple foundries in Europe.
Density controlled coating or the benefits of intelligent automatic coating control
The Foseco Intelligent Coating Unit (ICU) was introduced in 2019 to improve the handling and application of mould/core coatings in ferrous foundries. It thus offers a way for foundries to improve process reliability, as well as casting quality. Further developments of the ICU concept since then have led to the launch of new modular and integrated solutions that extend its use to a wider range of foundries, and show payback on investment within a year of installation. The very latest innovation is the first handheld density measurement tool, which has been released as a replacement for traditional Baumé and flow cup testing when manual coating control is required.
New mould release agent reduces fire and environmental risk
Due to concerns about the fire safety and environmental performance of existing petroleum-based green sand mould release agents, Foseco has developed the PARTISAL 477 ECO family of release agents. These costeffective, non-toxic agents deliver improved flammability resistance, while maintaining performance standards in terms of release efficiency, ease of application, and lubrication of (vertical) moulding machine components.
Supporting the transition to lead-free bearings in large diesel engines: the challenge for foundries
The EU has restricted the use of lead-containing bearings in diesel engines. This poses a challenge for engine makers, who traditionally used lead in bearings to achieve satisfactory engine reliability. Its qualities as a dry lubricant protected the bearings from particulate contaminants, such as those left over from the casting process (moulding sand, and residues from the binder and the coating itself). To support the transition to lead-free bearings, SEMCO IC coatings are designed to significantly improve the removal of such casting debris from even the most complex of castings. In doing so, these coatings continue to set new standards when it comes to the ultra-low number of particles remaining in the as-cast condition. The latest generation of SEMCO IC coating is also formulated so that any remaining coating particles are softer than the bearings. This eliminates the risk of wear to the bearing from coating residue.