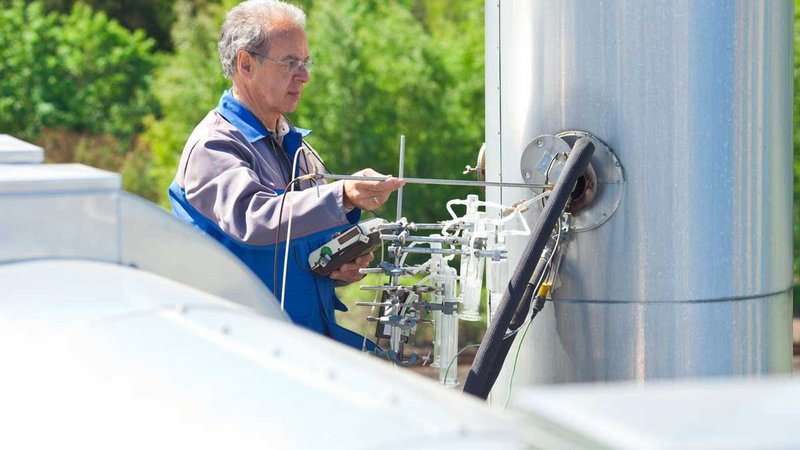
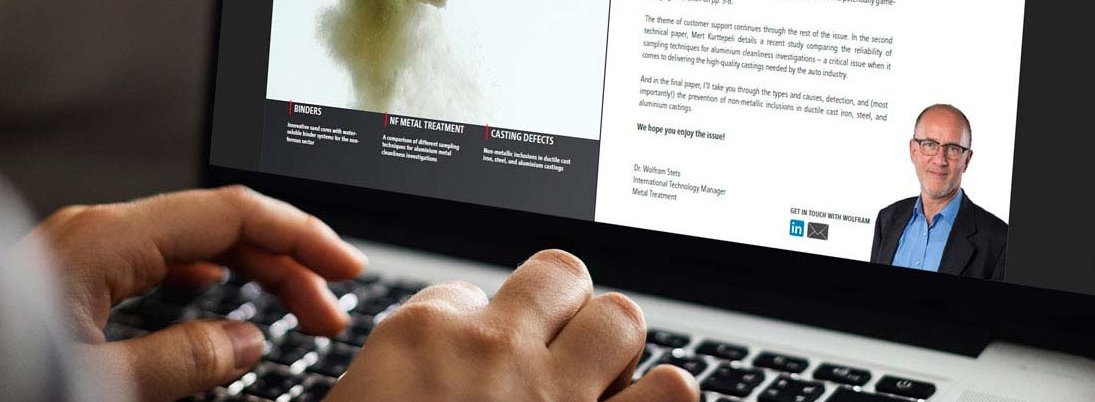
Foundry Practice 271
14 Dec 2022
The customer comes first. It might be a familiar adage, but we take it very seriously here at Foseco. Customer support is at the centre of everything we do – whether it’s correct product selection and application, or more general issues, such as problem solving and defect analysis.
This ethos also drives our approach to R&D. By listening to our customers and working with them to understand their specific needs and problems, we are able to develop solutions that directly address these issues. In this way, we help deliver enhanced competitiveness in a dynamic and rapidly-changing market.
A good example is presented in the first technical article of this issue. We start with the challenge: in this case, the electrification and lightweighting of vehicles. This is having a massive impact on the foundry industry, as ICE powertrains are replaced with electric motors. As a result, a dramatic increase in aluminium foundry output – and especially high-pressure diecasting – is needed. But growth in this sector has been limited by difficulties in manufacturing cored castings. To address this issue, we developed a novel water-soluble binder system that enables high-pressure foundries to produce cored aluminium castings economically, efficiently, and sustainably. Vincent Haanappel and Mark Stapleton introduce this potentially gamechanging innovation on pp. 5-8.
The theme of customer support continues through the rest of the issue. In the second technical paper, Mert Kurttepeli details a recent study comparing the reliability of sampling techniques for aluminium cleanliness investigations – a critical issue when it comes to delivering the high-quality castings needed by the auto industry.
And in the final paper, we take you through the types and causes, detection, and (most importantly!) the prevention of non-metallic inclusions in ductile cast iron, steel, and aluminium castings.
We hope you enjoy the issue!
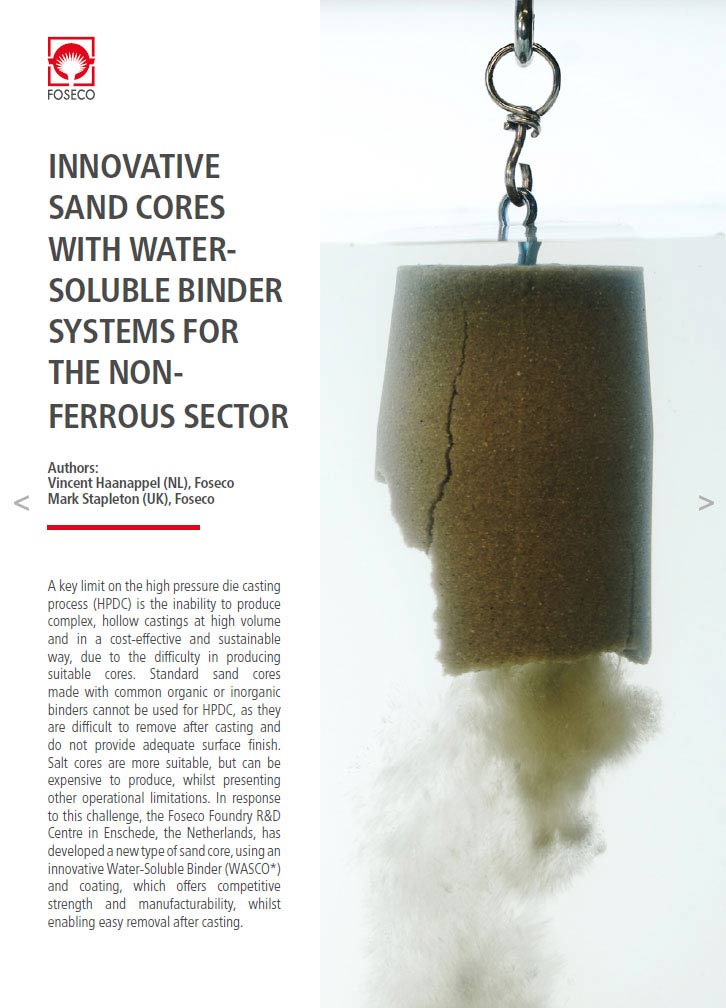
Innovative sand cores with water-soluble binder systems for the non-ferrous sector
A key limit on the high pressure die casting process (HPDC) is the inability to produce complex, hollow castings at high volume and in a cost-effective and sustainable way, due to the difficulty in producing suitable cores. Standard sand cores made with common organic or inorganic binders cannot be used for HPDC, as they are difficult to remove after casting and do not provide adequate surface finish.
Salt cores are more suitable, but can be expensive to produce, whilst presenting other operational limitations. In response to this challenge, the Foseco Foundry R&D Centre in Enschede, the Netherlands, has developed a new type of sand core, using an innovative Water-Soluble Binder (WASCO*) and coating, which offers competitive strength and manufacturability, whilst enabling easy removal after casting.
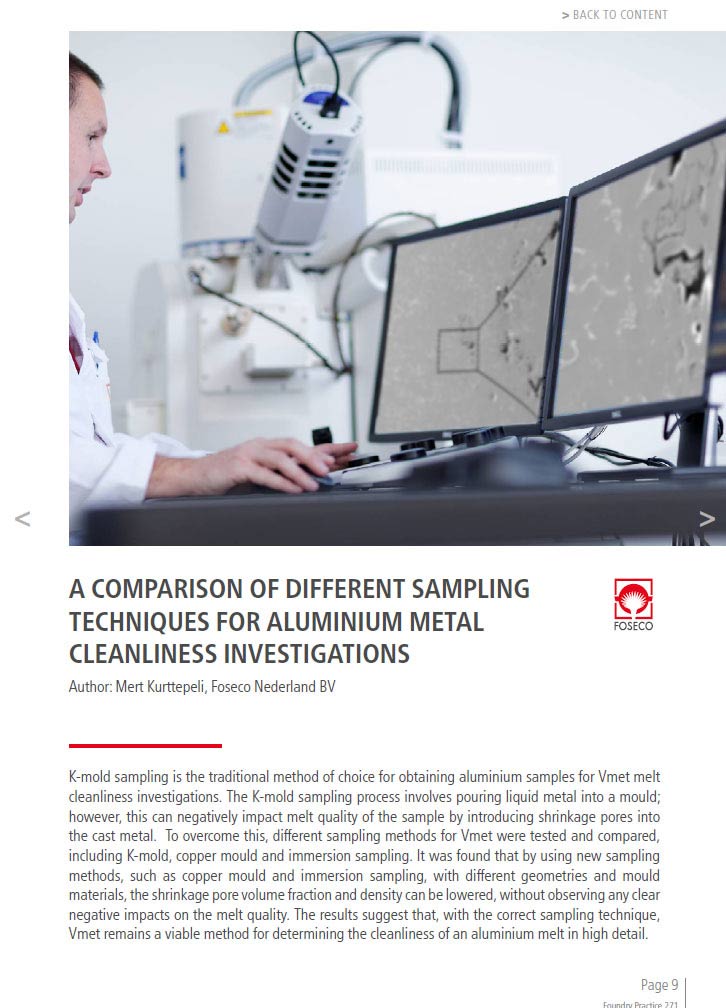
A comparison of different sampling techniques for aluminium metal cleanliness investigations
K-mold sampling is the traditional method of choice for obtaining aluminium samples for Vmet melt cleanliness investigations. The K-mold sampling process involves pouring liquid metal into a mould; however, this can negatively impact melt quality of the sample by introducing shrinkage pores into the cast metal. To overcome this, different sampling methods for Vmet were tested and compared, including K-mold, copper mould and immersion sampling. It was found that by using new sampling methods, such as copper mould and immersion sampling, with different geometries and mould materials, the shrinkage pore volume fraction and density can be lowered, without observing any clear negative impacts on the melt quality. The results suggest that, with the correct sampling technique, Vmet remains a viable method for determining the cleanliness of an aluminium melt in high detail.
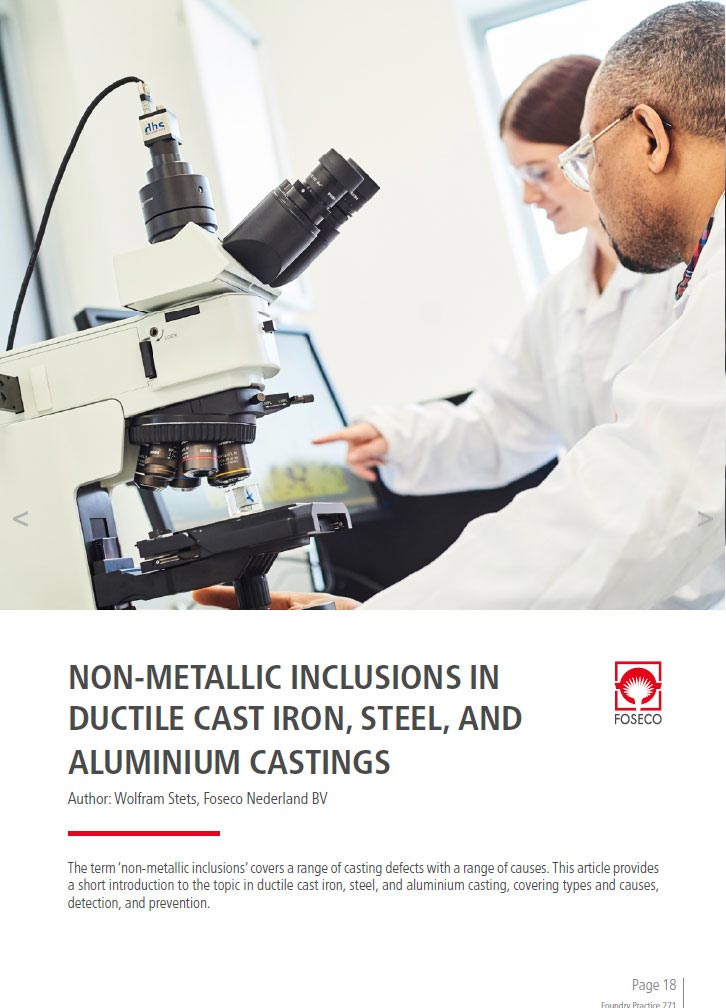
Non-metallic inclusions in ductile cast iron, steel, and aluminium castings
The term ‘non-metallic inclusions’ covers a range of casting defects with a range of causes. This article provides a short introduction to the topic in ductile cast iron, steel, and aluminium casting, covering types and causes, detection, and prevention. Non-metallic inclusions are the most common cause of casting defects; the enemy of the quality-conscious foundryman. And an elusive enemy too. Although there are some common types of inclusions (e.g., slag, sand, and oxides), as Gallo has noted, in any specific foundry application, uncovering ‘the root cause of inclusion defects may present great difficultly because of the wide range of interdependent molten metal and casting process contributing factors’. Any discussion of non-metallic inclusions must therefore be contextualised by metallurgy. This is the approach we take here to discuss the types and formation, detection, and prevention of non-metallic inclusions in some of the most-commonly cast metals and alloys. These are ductile (spheroidal graphite) cast iron, steel, and aluminium.